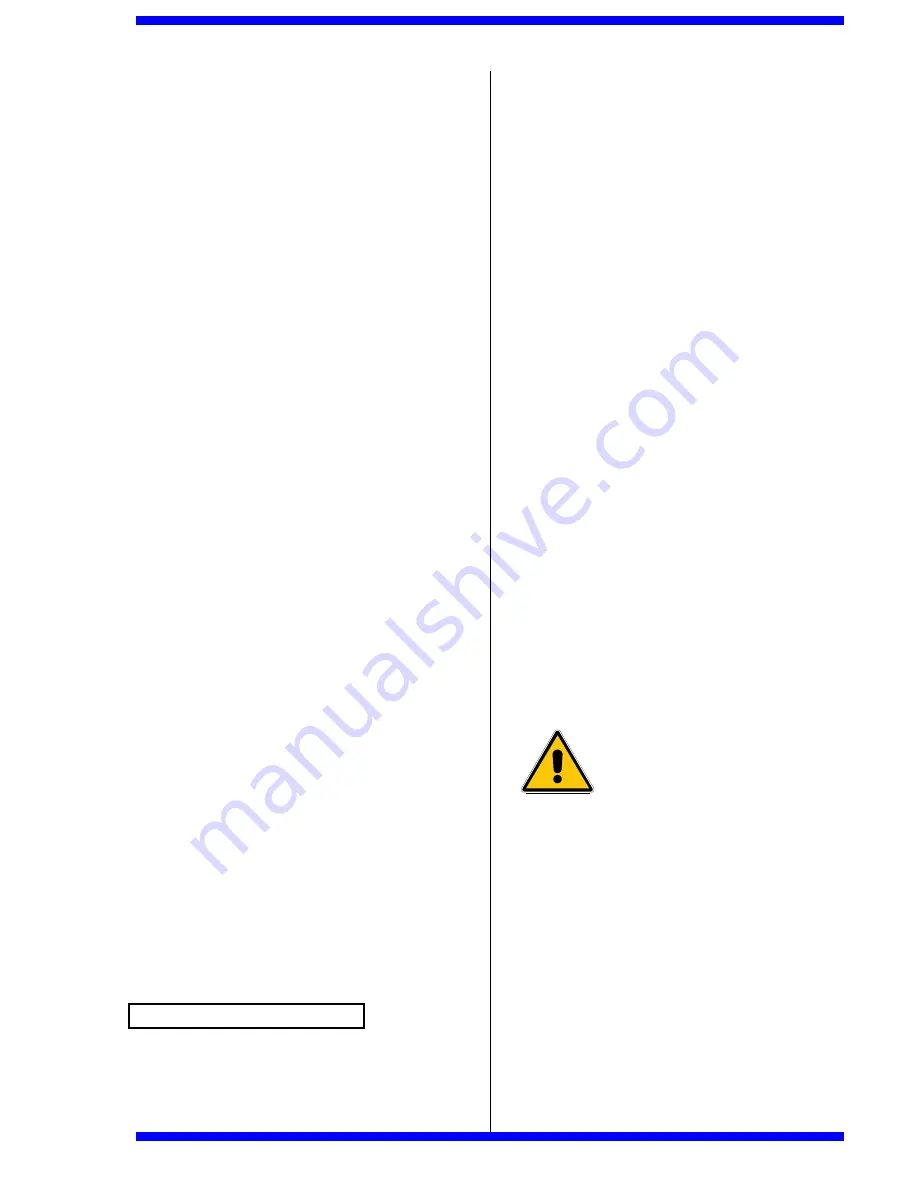
Selwood Seltorque S150 Manual
11
NOTE:
An impeller removal tool (Part No.
0015WRS781) is available to facilitate removal of the
impeller, refer to Section 6.10 Remove Impeller.
Removal of the impeller will allow the mechanical seal
spring to expand. Do not touch the shaft sleeve (C06)
or spring if the mechanical seal has been functioning
correctly and only the impeller is to be replaced.
Premature failure of the mechanical seal assembly
could result if the seal's faces are disturbed by moving
the shaft sleeve.
7. When fitting a new impeller, ensure that key (C05)
is not a tight fit in the impeller keyway. If
necessary, remove very small amounts of metal
from the sides of the key to achieve a close sliding
fit that will not allow any perceptible rotation of the
impeller on the shaft, and yet allow the impeller to
slide into place by hand. Apply Rustilo 431 grease
(or approved equivalent) to all impeller mounting
surfaces.
8. Check condition of nylon patch on impeller screw
(C01). It is
essential
that this screw should be stiff
to turn in the thread of the shaft. On no account
use a screw that moves freely. Use a new screw
if the head of the original component is abraded or
if the screw is not a friction fit in the shaft thread.
Do NOT lubricate these threads.
9. Ensuring that the mechanical seal spring is in
position, replace impeller (C04), washer (C03) two
washers (C02) with concave faces towards
impeller and impeller screw (C01), and tension
screw to 80lbf ft (11kgf m) torque. It is essential
that this screw is correctly tensioned. During this
operation, it will be necessary to lock the impeller
by means of a wooden block wedged between the
impeller blades and pump body (C09). Remove
block after use.
10. Use Rustilo 431 on inside of pump register. Fit
new gasket (B28), position suction tube on studs,
fit washers (B30) and (B39) and fully tighten nuts
(B29) and (B36). Grease should be smeared on
the inside of the dome nuts (B36), which must be
correctly positioned on studs inside suction tube.
11. Renew gasket (B25), reposition separator body
sub-assembly on suction tube, and fit separator
cap assembly. Assemble washers (A12) and nuts
(A11) and alternatively tighten each nut a small
amount to ensure that the cap is pulled down
evenly. Do NOT overtighten.
12. Reposition air hose (A01) on spigot of separator
cap (B01) and tighten hose clip (A02).
13. Replace drain plug (D34) using PTFE tape as a
sealant, and fill flushing chamber with new oil to
level of plug. Replace plug and ‘O’ ring (D08) and
(D07). Refer to Section 3.1 Pump Lubrication for
details of the oil required for the flushing chamber.
The mechanical seal should be replaced if the flushing
chamber oil continuously leaks into the pumped fluid,
or if the oil becomes contaminated with the product.
This latter condition is sometimes indicated by leakage
of fluid out of a breather cap (D12). Under extreme
conditions, pumped fluid may be seen escaping out of
the vent at the bottom of flushing chamber (D33).
In the event of abrasive materials being detected in the
oil, it is likely that lip seal (D04) will have become worn
and necessitate replacement in accordance with
Section 5.4.3 Bearings and Lip Seal (D15, D18 and
D04).
Daily checks on oil condition should ensure that seal
failure is detected before damage occurs to related
components.
If the mechanical seal leaks, proceed as follows:
1. Drain oil from flushing chamber (D33) by removing
its filler cap (D08) and drain plug (D34).
2. Remove impeller (C04) in accordance with
Section 5.3.1 Impeller (C04) Instructions 1 to 6
inclusively, and remove impeller key (C05).
3. Withdraw shaft sleeve (C06) together with rotating
mechanical seal parts and spring. It is likely that
‘O’ ring (C07) will be withdrawn with the sleeve
remove it and check condition. Replace ‘O’ ring if
unsuitable for further service.
4. Using seat removal tool (Part No. 0015166000),
withdraw mechanical seal stationary seat from its
housing in pump body (C09). Also remove the
seat's rubber joint ring. Refer to Section 6.3
Removal of Mechanical Seal Stationary Seat and
Joint Ring.
5. The rotating parts of mechanical seal (C08) should
now be removed from the shaft sleeve and
discarded, taking care not to damage the sleeve's
surfaces. This operation should be carried out by
hand using a tool that will not scratch the sleeve.
Once removed, examine condition of sleeve and
replace with new component if unacceptably
corroded or worn.
IMPORTANT ADVICE
New mechanical seal components must
be handled with great care, in
particular, the seal faces must not be
touched by hand and must only come
into contact with clean soft paper that is
free
from
abrasive
materials.
Premature seal failure is likely to occur
if this advice is not heeded.
6. Thoroughly clean recess in pump body (C09) and
also the surrounding surfaces. Smear lubricant
(soft soap or washing up liquid, but not grease) in
recess and also on outside diameter of rubber
joint ring. Using several layers of clean soft paper
to protect the seating face, press seat into recess
by applying even finger pressure. Make sure that
the highly polished sealing face is on the impeller
side of the recess, that the new joint ring has been
used, and that the seat is positioned directly
against the shoulder at the bottom of the recess.
7. Smear oil on drive shaft diameters and ‘O’ ring
(C07). Position ‘O’ ring on shaft taking care to
prevent it contacting the shaft's keyway. If a new
shaft sleeve (C06) is being used, ensure that it is
capable of sliding freely along the shaft and
correctly trapping the ‘O’ ring in the recess
provided.
Summary of Contents for SELTORQUE S150
Page 25: ...Selwood Seltorque S150 Manual 25 THIS PAGE INTENTIONALLY BLANK ...
Page 28: ...Selwood Seltorque S150 Manual 28 ...
Page 30: ...Selwood Seltorque S150 Manual 30 ...
Page 32: ...Selwood Seltorque S150 Manual 32 ...
Page 34: ...Selwood Seltorque S150 Manual 34 ...
Page 36: ...Selwood Seltorque S150 Manual 36 ...
Page 38: ...Selwood Seltorque S150 Manual 38 ...
Page 40: ...Selwood Seltorque S150 Manual 40 ...
Page 42: ...Selwood Seltorque S150 Manual 42 ...
Page 44: ...Selwood Seltorque S150 Manual 44 ...
Page 46: ...Selwood Seltorque S150 Manual 46 ...
Page 48: ...Selwood Seltorque S150 Manual 48 ...
Page 50: ...Selwood Seltorque S150 Manual 50 ...
Page 52: ...Selwood Seltorque S150 Manual 52 ...
Page 54: ...Selwood Seltorque S150 Manual 54 ...
Page 56: ...Selwood Seltorque S150 Manual 56 ...
Page 58: ...Selwood Seltorque S150 Manual 58 9 WIRING DIAGRAMS 9 1 Isuzu 4JG1 Engine Canopy ...
Page 60: ...Selwood Seltorque S150 Manual 60 9 3 Deutz Wiring Diagram ...
Page 62: ...Selwood Seltorque S150 Manual 62 THIS PAGE INTENTIONALLY BLANK ...