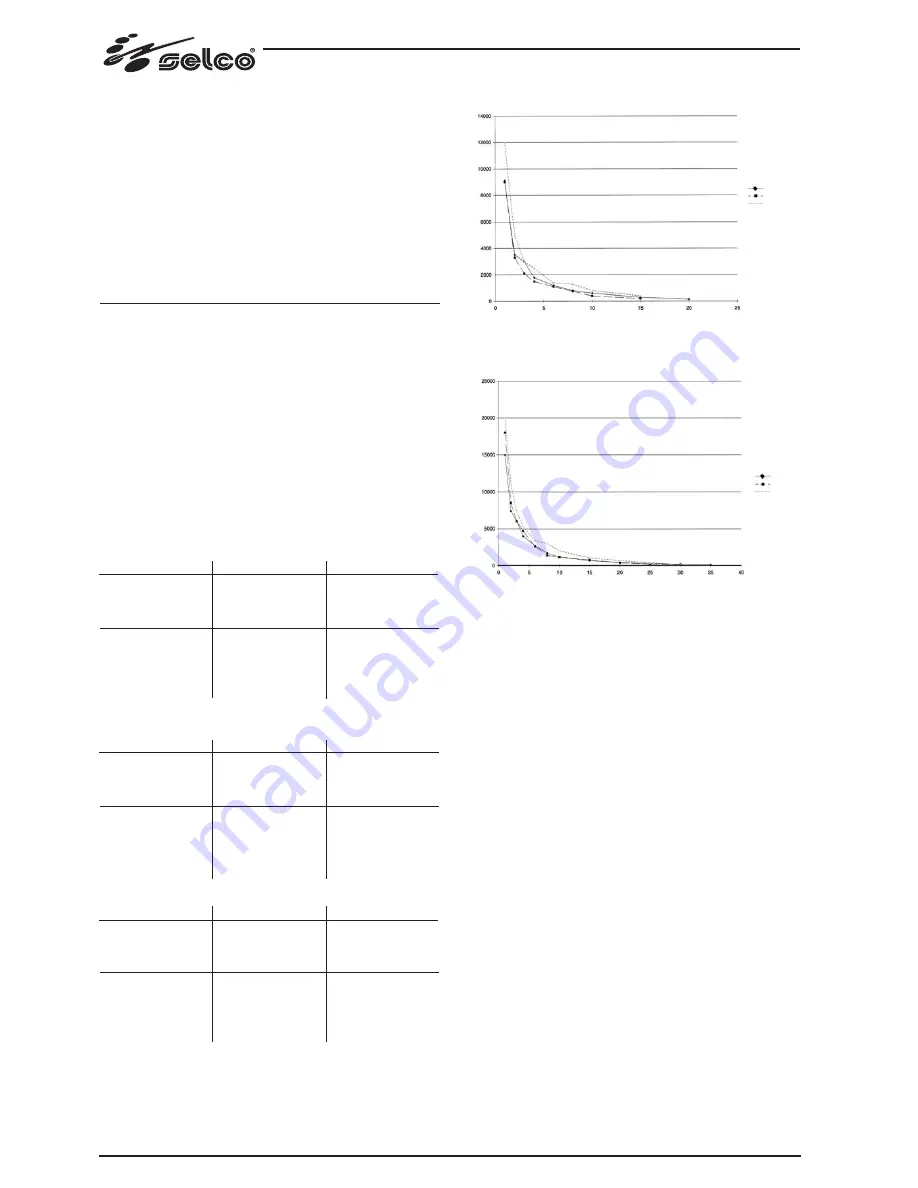
18
12.1 Plasma cutting process
The cutting action is obtained when the plasma arc, made very
hot and highly concentrated by the design of the torch, transfers
onto the conductive piece to be cut, closing the electrical circuit
with the generator. The material is first melted at a high tempe-
rature of the arc, and then removed by the high exit velocity of
the ionized gas from the nozzle.
The arc can have two different states: that of the transferred arc,
when the current passes through the piece to be cut, that of the
pilot arc or non-transferred arc, when this is sustained between
the electrode and the nozzle.
13.0 CUTTING SPECIFICATIONS
In plasma cutting, the thickness of the material to be cut, the
speed of cutting and the current supplied by the generator have
values which are related to each other; these depend on the type
and quality of the material, type of torch as well as the type and
condition of the electrode and nozzle, distance between nozzle
and piece, pressure and impurity of the compressed air, cut qua-
lity required, temperature of the piece to be cut, etc.
In the diagrams as in Fig.8, 9 we can see that the thickness to be
cut is inversely proportional to the cutting speed, and that both
these values can be increased with an increase in current.
The cutting tests have been performed in standard operating
conditions using a Trafimet torch at 90A.
MILD STEEL
STAINLESS STEEL
ALUMINIUM
* High quality cut
Fig. 8
Fig. 9
Thickness (mm)
3
6
10
15
3
6
10
20
30
Current (A)
50
50
50
50
80
80
80
80
80
Speed (mm/min)
3000
1200
600
300
6000
2700
1200
450
200
Thickness (mm)
3
6
10
15
3
6
10
20
25
Current (A)
50
50
50
50
80
80
80
80
80
Speed (mm/min)
2100
1000
400
200
6000
2600
1200
400
200
Thickness (mm)
3
6
10
15
3
6
10
20
25
Current (A)
50
50
50
50
80
80
80
80
80
Speed (mm/min)
3000
1400
800
400
7300
3400
2000
700
400
CUTTING SPEED WITH 50A
SPEED (mm/min)
SPEED (mm/min)
CUTTING SPEED WITH 80A
THICKNESS (mm)
MILD STEEL
STAINLESS STEEL
ALUMINIUM
MILD STEEL
STAINLESS STEEL
ALUMINIUM
THICKNESS (mm)