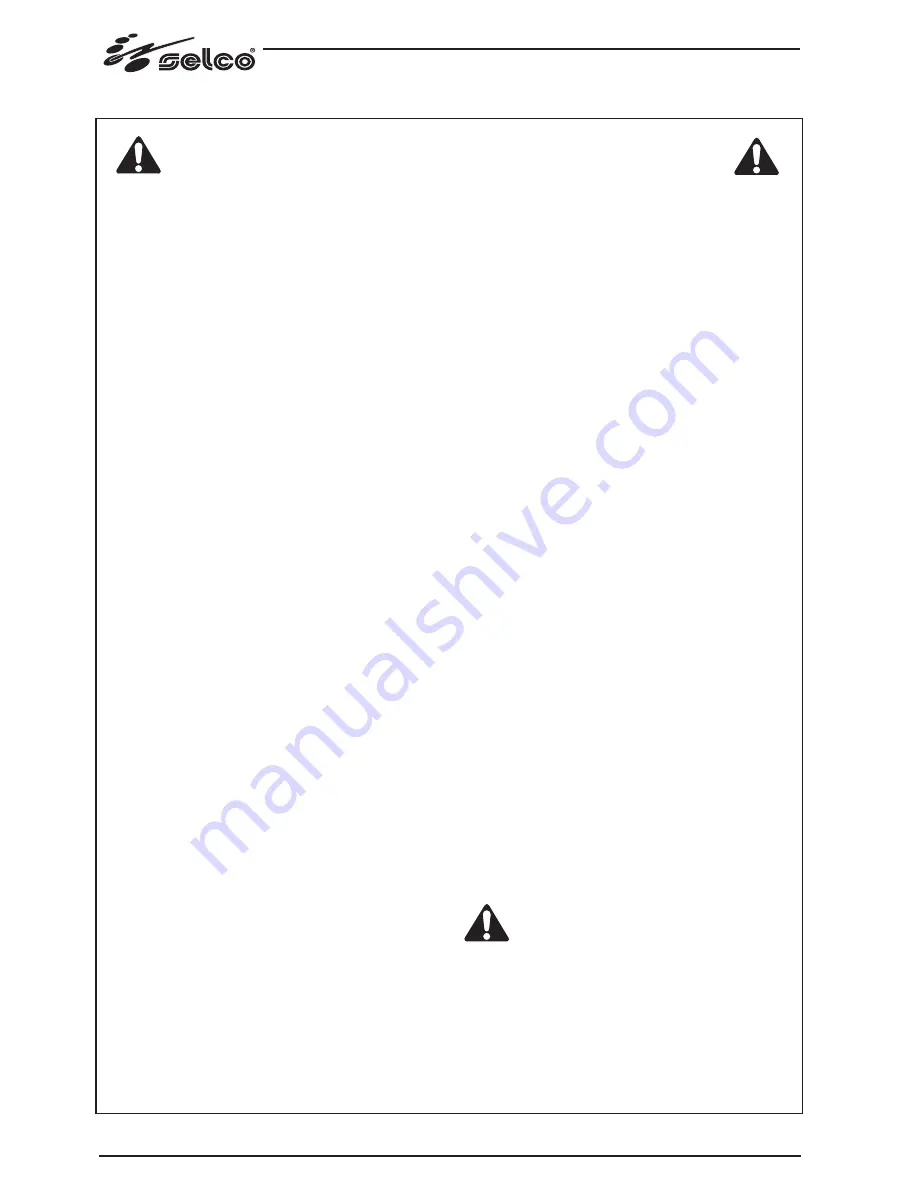
1.0 SAFETY
Prior to performing any operation on the machine, make sure that you
have thoroughly read and understood the contents of this manual.
Do not perform modifications or maintenance operations which are not
prescribed.
For any doubt or problem regarding the use of the machine, even if not
described herein, consult qualified personnel.
The productor cannot be held responsible for damage to persons or pro-
perty caused by the operator's failure to read or apply the contents of
this manual.
1.1 Operator and other persons' protection
The welding (cutting) process is a noxious source of radiations, noise,
heat and gas emissions. Persons fitted with pacemakers must consult
their doctor before undertaking arc welding or plasma cut operations. If
the above prescription is not observed, the manufacturer accepts no lia-
bility for any damages sustained in the event of an accident.
Personal protection:
- Do not wear contact lenses!!!
- Keep a first aid kit ready for use.
-
Do not underestimate any burning or injury.
- Wear protective clothing to protect your skin from the arc rays, sparks
or incandescent metal, and a helmet or a welding cap.
- Wear masks with side face guards and suitable protection filter (at
least NR10 or above) for the eyes.
- Use headphones if dangerous noise levels are reached during the
welding (cutting).
Always wear safety goggles with side guards, especially during the
manual or mechanical removal of welding (cutting) slags.
lf you feel an electric shock, interrupt the welding (cutting) operations
immediately.
Other persons' protection:
- Position a fire-retardant partition to protect the surrounding area from
rays, sparks and incandescent slags.
- Advise any person in the vicinity not to stare at the arc or at the incan-
descent metal and to get an adequate protection.
- lf the noise level exceeds the limits prescribed by the law, delimit the
work area and make sure that anyone getting near it is protected with
headphones or earphones.
1.2 Fire/explosion prevention
The welding (cutting) process may cause fires and/or explosions.
- Compressed gas cylinders are dangerous; consult the supplier befo-
re handling them.
Protect them from:
- direct exposure to sun rays;
- flames;
- sudden changes in temperature;
- very low temperatures.
Compressed gas cylinders must be fixed to the walls or to other sup-
ports, in order to prevent them from falling.
- Clear the work area and the surrounding area from any infiammable
or combustible materials or objects.
- Position a fire-fighting device or material near the work area.
- Do not perform welding or cutting operations on closed containers or
pipes.
- lf said containers or pipes have been opened, emptied and carefully
cleaned, the welding (cutting) operation must in any case be perfor-
med with great care.
- Do not weld (cut) in places where explosive powders, gases or
vapours are present.
- Do not perform welding (cutting) operations on or near containers
under pressure.
- Don’t use this machine to defrost pipes.
1.3 Protection against fumes and gases
Fumes, gases and powders produced during the welding (cutting) pro-
cess can be noxious for your health.
-
Do not use oxygen for the ventition.
- Provide for proper ventilation, either natural or forced, in the work
area.
- In case of welding (cutting) in extremely small places the work of the
operator carrying out the weld should be supervised by a colleague
standing outside.
- Position gas cylinders outdoors or in places with good ventilation.
- Do not perform welding (cutting) operations near degreasing or pain-
ting stations.
1.4 Positioning the power source
Keep to the following rules:
- Easy access to the equipment controls and connections must be pro-
vided.
- Do not position the equipment in reduced spaces.
- Do not place the generator on surfaces with inclination exceeding 10°
with respect to the horizontal plane.
1.5 lnstalling the apparatus
- Comply with the local safety regulations for the installation and carry
out the maintenance service of the machine according to the con-
structor's directions.
- Any maintenance operation must be performed by qualified person-
nel only.
- The connection (series or parallel) of the generators is prohibited.
- Before operating inside the generator, disconnect the power supply.
- Carry out the routine maintenance on the equipment.
- Make sure that the supply mains and the earthing are sufficient and
adequate.
- The earth cable must be connected as near the area to be welded
(cut) as possible.
- Take the precautions relevant to the protection degree of the power
source.
- Before welding (cutting) , check the condition of the electric cables
and of the torch, and if they are damaged repair or change them.
- Neither get on the material to be welded (cut), nor lean against it.
-
The operator must not touch two torches or two electrode holders
at the same time.
1.6 Precautions against risks connected with the
use of compressed air
Connect the air supply to the coupling provided, making sure pressure
is at least 6 bars (0.6 MPa) with a minimum flow rate of 200 l/min. If the
air supply comes from pressure reducer of a compressor or a central
system, the reducer must be set to the maximum outlet pressure that
must not, however, exceed 8 bars (0.8 MPa). If the air supply comes
from a compressed air canister it must be equipped with a pressure
regulator.
A compressed air canister must never be directly
coupled to the machine pressure reducer. Pressure
might exceed the capacity of the reducer which might
consequently explode.
12
WARNING