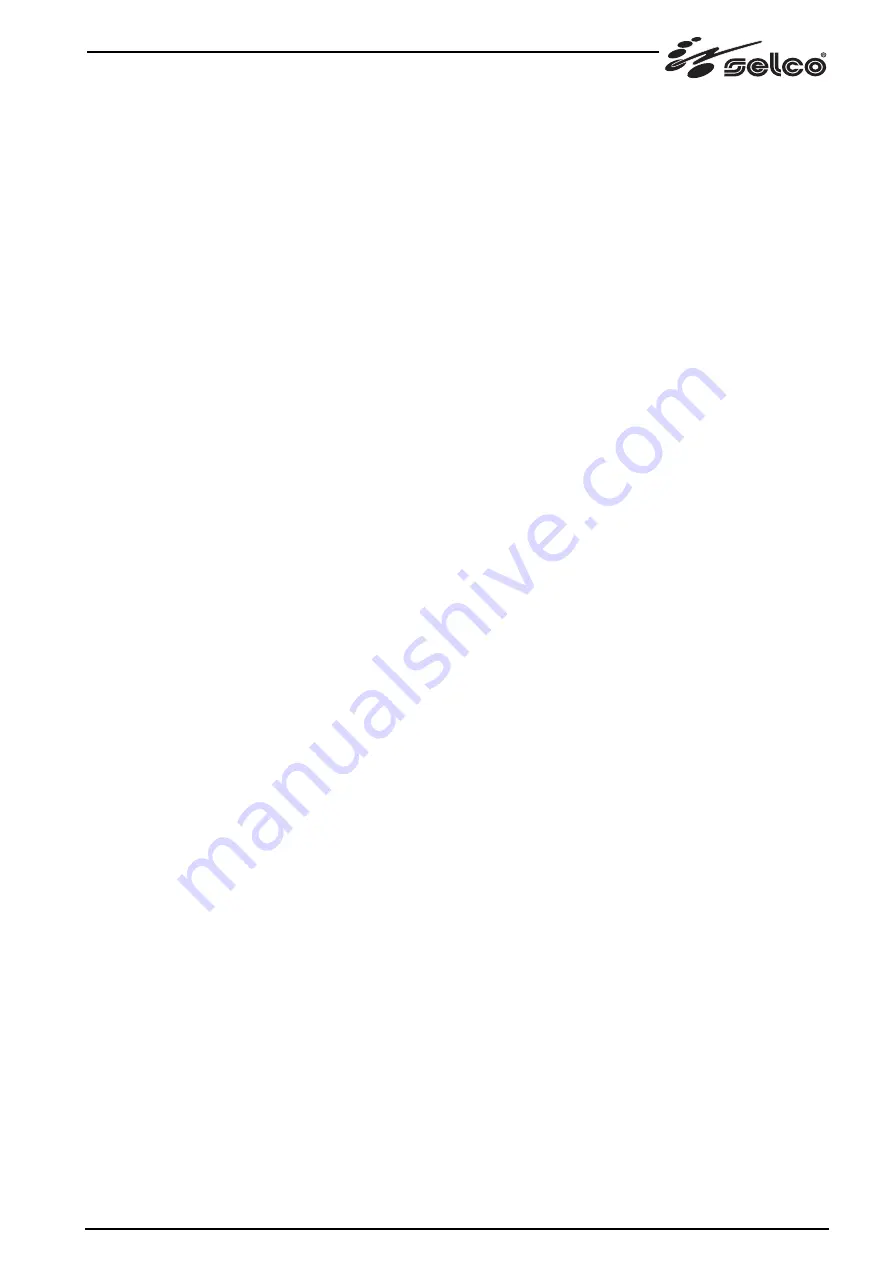
31
Cause
Incorrect welding parameters.
Solution
Increase the welding current.
Cause Incorrect
electrode.
Solution
Use a smaller diameter electrode.
Cause
Incorrect edge preparation.
Solution
Increase the chamfering.
Cause
Incorrect earth connection.
Solution
Earth the system correctly
Read the paragraph “Installation “.
Cause
Pieces to be welded too big.
Solution
Increase the welding current.
Slag inclusions
Cause Poor
cleanliness.
Solution
Clean the pieces accurately before welding.
Cause
Electrode diameter too big.
Solution
Use a smaller diameter electrode.
Cause
Incorrect edge preparation.
Solution
Increase the chamfering.
Cause
Incorrect welding mode.
Solution
Decrease the distance between the electrode and
the piece.
Move regularly during all the welding operations.
Tungsten inclusions
Cause
Incorrect welding parameters.
Solution
Decrease the welding voltage.
Cause Incorrect
electrode.
Solution
Always use quality materials and products.
Sharpen the electrode carefully.
Cause
Incorrect welding mode.
Solution
Avoid contact between the electrode and the weld
pool.
Blowholes
Cause Insufficient
shielding
gas.
Solution
Adjust the gas flow.
Sticking
Cause
Incorrect arc length.
Solution Increase the distance between the electrode and
the piece.
Cause
Incorrect welding parameters.
Solution
Increase the welding current.
Cause
Incorrect welding mode.
Solution
Angle the torch more.
Cause
Pieces to be welded too big.
Solution
Increase the welding current.
Undercuts
Cause
Incorrect welding parameters.
Solution
Decrease the welding voltage.
Cause Incorrect
arc
length.
Solution Increase the distance between the electrode and
the piece.
Cause Incorrect
welding
mode.
Solution
Decrease the side oscillation speed while filling.
Decrease the travel speed while welding.
Cause
Insufficient shielding gas.
Solution
Use gases suitable for the materials to be welded.
Oxidations
Cause
Insufficient gas protection.
Solution
Adjust the gas flow.
Porosity
Cause
Grease, varnish, rust or dirt on the workpieces to
be welded.
Solution
Clean the workpieces carefully before welding.
Cause
Grease, varnish, rust or dirt on the filler material.
Solution
Always use quality materials and products.
Keep the filler metal always in perfect condition.
Cause
Humidity in the filler metal.
Solution
Always use quality materials and products.
Keep the filler metal always in perfect condition.
Cause Incorrect
arc
length.
Solution
Decrease the distance between the electrode and
the piece.
Cause
Humidity in the welding gas.
Solution
Always use quality materials and products.
Ensure the gas supply system is always in perfect
condition.
Cause
Insufficient shielding gas.
Solution
Adjust the gas flow.
Cause
The weld pool solidifies too quickly.
Solution
Decrease the travel speed while welding.
Pre-heat the workpieces to be welded.
Increase the welding current.
Hot cracks
Cause Incorrect
welding
parameters.
Solution
Decrease the welding voltage.
Cause
Grease, varnish, rust or dirt on the workpieces to
be welded.
Solution
Clean the workpieces carefully before welding.
Cause
Grease, varnish, rust or dirt on the filler metal.
Solution
Always use quality materials and products.
Keep the filler metal always in perfect condition.
Cause Incorrect
welding
mode.
Solution
Carry out the correct sequence of operations for
the type of joint to be welded.
Cause
Pieces to be welded have different characteristics.
Solution
Carry out buttering before welding.
Summary of Contents for Genesis 1700 BLH
Page 182: ...182 1 3 1 4 11 35 1 5 1 6...
Page 183: ...183 8 1 7 EN IEC 60974 10 B A A EN60974 10 A pace maker Point of Commom Coupling PCC...
Page 184: ...1 8 IP S IP23S 12 5 mm 60 2 2 1 2 2 10 2 3 230V 115V GENESIS 1700 BLH 15 15 15 2 1 5 184...
Page 190: ...190 4 4 RC 120 SET UP 5 6...
Page 191: ...191 Reset encoder...
Page 192: ...192 7 7 1 MMA Hot Start Arc Force...
Page 198: ...198 GENESIS 1700 BLH...
Page 208: ...208...