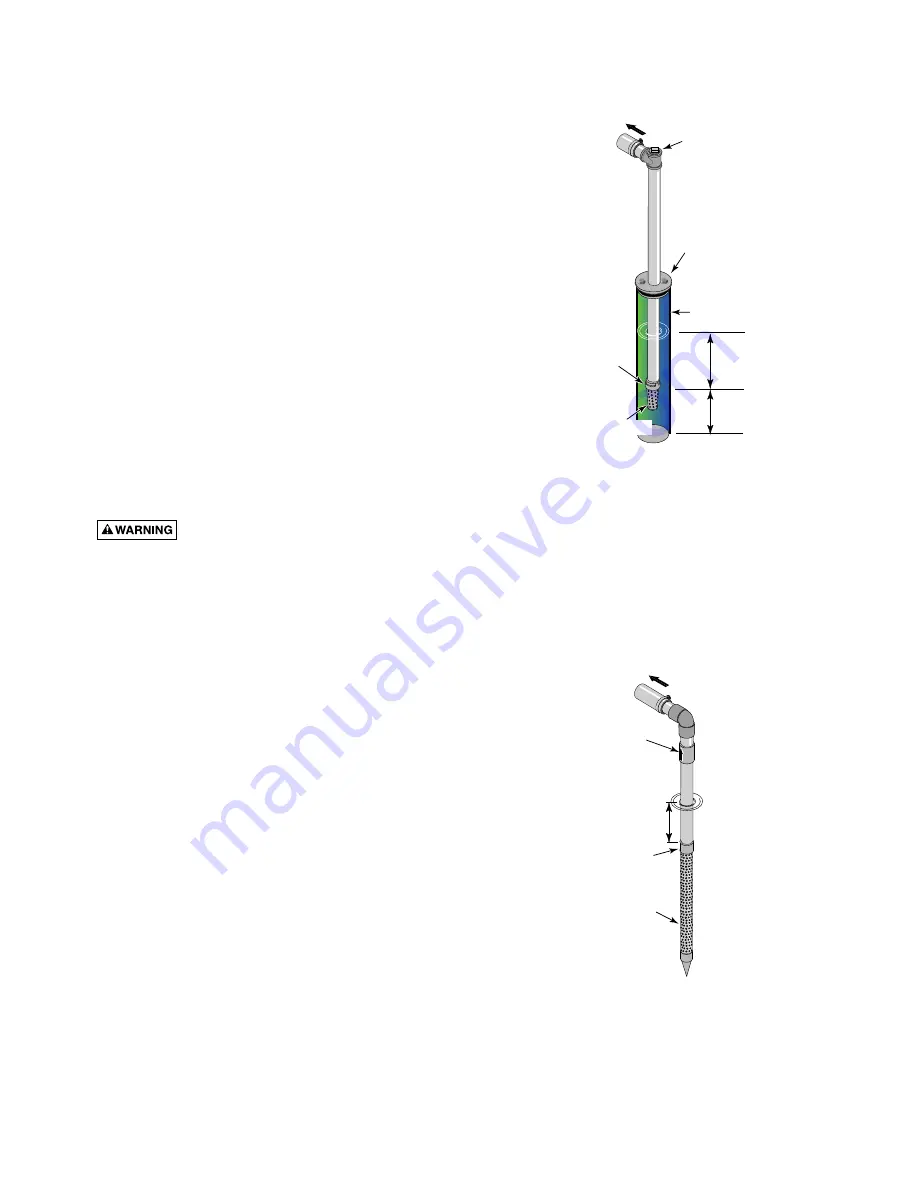
PREPARATION
INSTALLATION (Continued)
BASIC TOOLS AND MATERIALS NEEDED
Pipe Wrenches
Screwdriver
Hacksaw
Check Valve
Adjustable Wrench
Teflon Tape
Knife
NOTICE:
Depth to water must not be more than 20’.
1. Long runs and many fittings increase friction and reduce
flow. Locate pump as close to water source as possible:
use as few elbows and fittings as possible.
2. Be sure water is clear of sand. Sand will plug the pump
and void the warranty.
3. Protect pump and all piping from freezing. Freezing will
split pipe, damage pump and void the warranty. Check lo-
cally for frost protection requirements (usually pipe must
be 12” below frost line and pump must be insulated).
4. Be sure all pipes and foot valve are clean and in good
shape.
5. No air pockets in suction pipe.
6. No leaks in suction pipe. Use Teflon tape or Plasto-Joint
Stik
1
to seal pipe joints.
7. Unions installed near pump and water source will aid in
servicing. Leave room to use wrenches.
8.
Pump body may explode if used as a
booster pump. DO NOT use in a booster application.
1
Lake Chemical Co., Chicago, Illinois.
INSTALLATION
NOTICE:
Use the installation method below which matches
your well type.
CASED WELL INSTALLATION
1. Inspect foot valve to be sure it works freely. Inspect
strainer to be sure it is clean.
2. Connect foot valve and strainer to the first length of suc-
tion pipe and lower pipe into well. Add sections of pipe
as needed, using Teflon tape on male threads. Be sure that
all suction pipe is leakproof or pump will lose prime and
fail to pump. Install foot valve 10 to 20 feet below the low-
est level to which water will drop while pump is operat-
ing (pumping water level). Your well driller can furnish
this information.
3. To prevent sand and sediment from entering the pump-
ing system, the foot valve/strainer should be at least 5 feet
above the bottom of the well.
4. When the proper depth is reached, install a sanitary well
seal over the pipe and in the well casing. Tighten the bolts
to seal the casing.
5. When using a foot valve, a priming tee and plug as shown
in Figure 1 are recommended.
DUG WELL OR OPEN WATER
INSTALLATION
1. Follow cased well installation, steps 1, 2, 3 and 5.
DRIVEN POINT INSTALLATION
1. Connect the suction pipe to the drive point as illustrated in
Figure 2. Keep horizontal pipe run as short as possible. Use
Teflon tape on male pipe threads. Multiple well points may
be necessary to provide sufficient water to pump.
2. Install a check valve in piping as shown in Figure 2. Flow
arrow on check valve must point toward pump.
HORIZONTAL PIPING FROM WELL TO
PUMP
1. Never install a suction pipe that is smaller than the suc-
tion tapping of the pump.
3
Well
Casing
Foot
Valve
Sanitary
Well Seal
Suction Pipe
10'
Min.
5–10'
Strainer
2590 0996
Priming Tee
and Plug
Figure 1 – Cased/Dug Well Installation
Drive
Coupling
Drive
Point
Check
Valve
Drive point
below water
level
Suction Pipe
to Pump
2589 0996
Figure 2 – Driven Point Installation