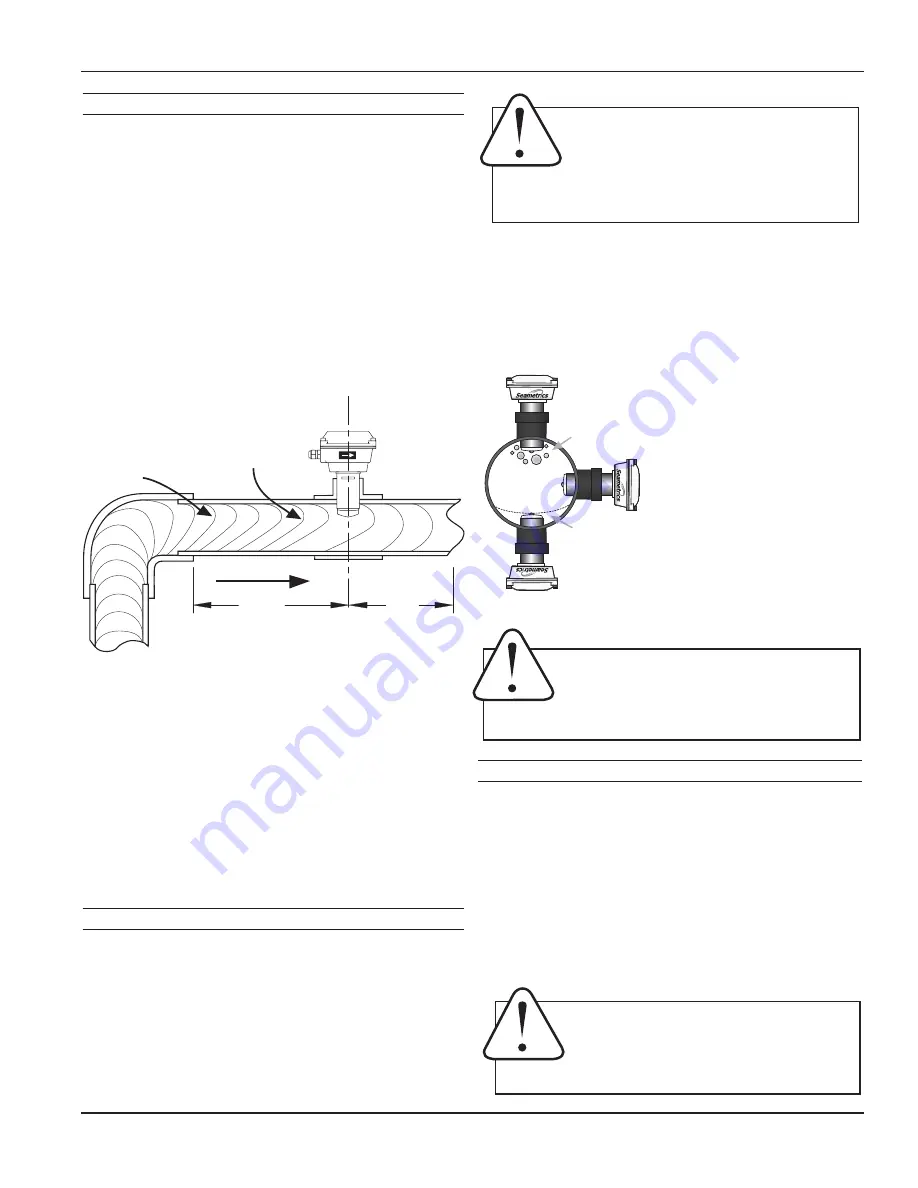
Seametrics • 253.872.0284
Page 5
seametrics.com
EX800-SERIES INSTRUCTIONS
Horizontal (3 o’clock or 9 o’clock position) is the preferred
installation orientation, since it improves low-flow
performance and avoids problems with trapped air and
sediment. (See Orienting the Meter diagram below.)
Bottom (6 o’clock), top (12 o’clock), and vertical pipe
installations are all acceptable if required by the piping
layout.
Orienting the Meter
Chemical Injection or Fertigation
When any magmeter, by any manufacturer, is used in a
chemical injection application (including fertigation), the
chemical injection point must be placed downstream of
the magmeter OR far enough upstream for complete
mixing to occur before the fluid reaches the meter. When
unmixed chemical or fertilizer alternates with water passing
through the meter, the rapid changes in conductivity may
cause sudden spikes and drops in the meter’s reading,
resulting in inaccurate measurement. The magmeter will
restabilize, however, with a steady flow of fluid of uniform
conductivity.
Caution:
These flow sensors are not
recommended for installation downstream of a
boiler feedwater pump where installation fault
may expose the flow sensor to boiler pressure
and temperature. Maximum recommended temperature
is 130°F (Plastic), 200°F (Metal).
Fair
Unacceptable if pipe
contains air
Best
Position
Air bubbles
Sediment
Fair
Unacceptable if pipe
contains sediment
Caution:
Never remove the U-clip retainer when
the pipe is under pressure. Always remove
pressure from the pipe before you attempt to
remove the meter. Removal under pressure
may result in damage or serious injury.
Caution
: In chemical injection or fertigation
applications, install chemical injection point
downstream of magmeter, or far enough
upstream to allow complete mixing of fluids
before the meter.
Fitting Installation
EX800-Series meters require special fittings that ensure
that the flow sensor is installed to the correct depth. The
fitting must be installed in the pipeline before the meter
can be installed. For best results, install with at least ten
diameters of straight pipe upstream of the meter and five
diameters downstream (or more under specific adverse
circumstances). See diagrams, next page.
If there is not enough straight run to smooth out the
turbulence caused by valves, fittings, and changes in
direction, some decrease in accuracy may result. This does
not mean that the flow meter’s reading is meaningless,
however. In some applications (control systems, valve
operation, chemical addition), a repeatable reading may
be more important than a highly accurate one.
Distorted Flows
Although EX800-Series PVC meter tees are supplied with
some straight pipe, additional straight pipe should be
added to meet straight pipe recommendations. It is not
advisable to connect a flow-disturbing device (e.g. valve or
elbow) directly to the end of these fittings.
A PVC fitting is usually installed by solvent welding. The
stainless steel and brass meter fittings have female pipe
threads, requiring the appropriate male threaded fittings.
Saddle or weld fittings (3” and above) require a hole to be
cut in the pipe. Recommended hole size is 1-3/4”.
Meter Installation
After the meter fitting is installed in the pipeline, the meter
can be installed in the fitting. After noting the direction
of the flow arrow, press the meter into the fitting as far
as it will go. Retain the meter in place by inserting the
U-clip. The clip can be installed from either side. It may
be necessary to rotate the probe back and forth slightly to
start the clip into the slots on the probe. Slide the clip in
as far as it will go.
5X
Distorted
Flow Profile
Faster Flow
Causes Meter
To Read High
10X
INSTALLATION