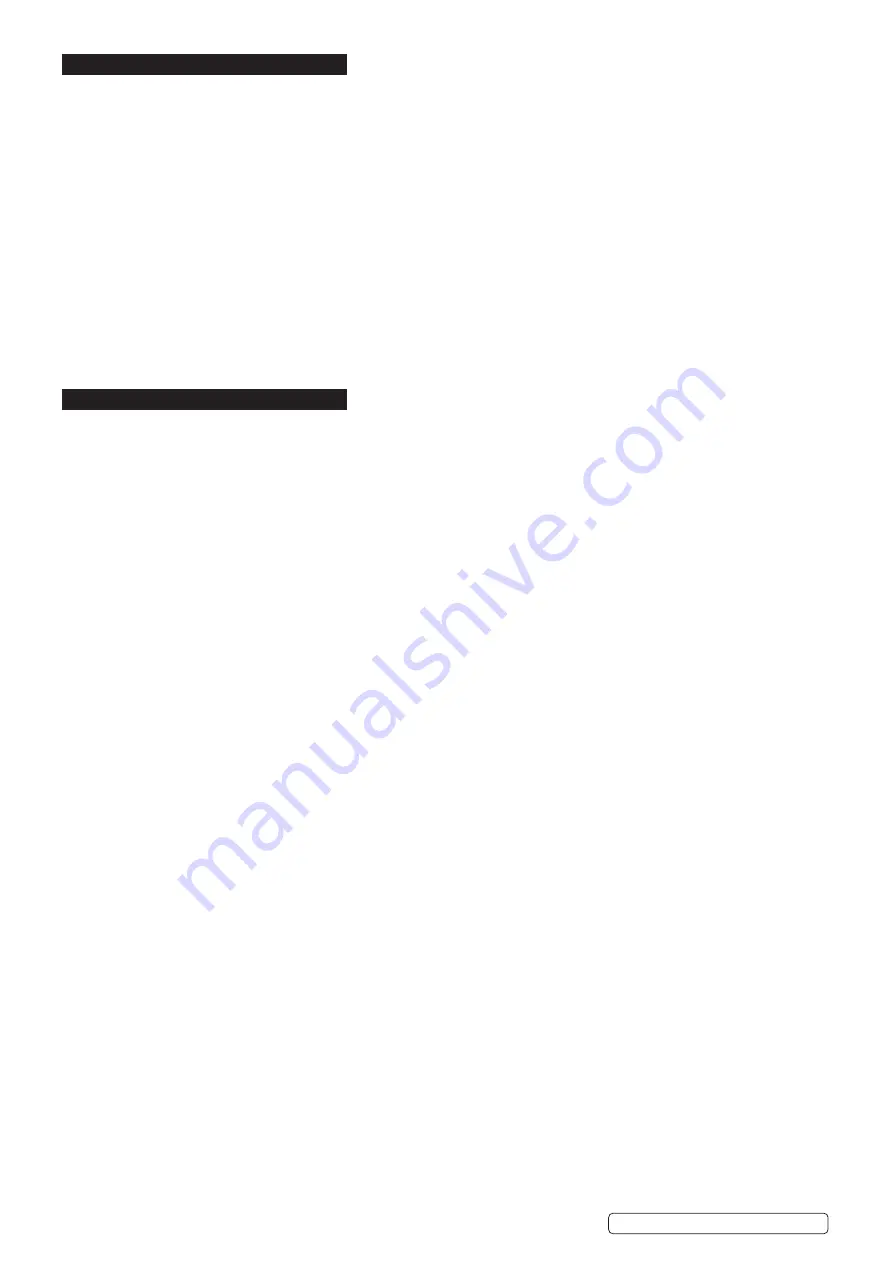
3. SPECIFICATION
Model No: ....................................................... YK759FAH.V2
Air Consumption: ........................................................... 7cfm
Bench or Floor Mounting: ...............................................Floor
Capacity: ................................................................... 75tonne
Gauge Included: ............................................................... Yes
Lateral Ram Travel: .................................................... 260mm
Maximum Height - Ram to Table: ............................... 884mm
Minimum Height - Ram to Table: ................................ 170mm
Optional Accessories: ...................... YKSG75 - Safety Guard
Optional Accessories: ........................ YKPP8 - Press Pin Set
Overall Height: ......................................................... 1925mm
Overall Width: .......................................................... 1560mm
Ram Diameter: .......................................................... Ø93mm
Ram Stroke: ............................................................... 250mm
Table Aperture: ........................................................... 251mm
Type: ..................................................................Air/Hydraulic
Working Pressure:................................................ 108-123psi
Working Table Depth: ................................................. 279mm
Working Table Width: ............................................... 1020mm
4. ASSEMBLY
Unpack the product and check contents. Should there be any damaged or missing parts contact your supplier immediately.
Take care to ensure safety when moving main frame from packing as the unit is very heavy.
Refer to attached parts list.
Seek assistance from another person on assembly of heavy parts.
Assemble press, if possible, in close proximity to where the press will be located.
4.1.
FRAME ASSEMBLY
4.1.1.
Attach load slings around the top cross member of the frame (#43) and using a suitable hoist or gantry, slowly, and in a controlled
manner lift the frame up and out of the transportation crate, into an upright position.
WARNING!
Take care when lifting the frame not to damage the pre-assembled ram assembly (#46).
4.1.2.
Keep the frame assembly in an upright position, held safely by the load slings.
4.2.
ATTACH BASE SECTION
NOTE:
The base section (#1), supports (#3), hex head screw M12 x 35 (#2), flat washer M12 (#6), spring washer M12 (#5) and
nut M12 (#4) are supplied pre-assembled.
4.2.1.
Remove the central fixings only, hex head screw M12 x 35 (#2), flat washer M12 (#6), spring washer M12 (#5) and nut M12 (#4)
from the base section (#1).
4.2.2.
Position the base section (#1) onto the frame (#43) and secure with hex head screw M12 x 35 (#2), flat washer M12 (#6), spring
washer M12 (#5) and nut M12 (#4) loosely.
4.2.3.
Remove the top fixings only, hex head screw M12 x 35 (#2), flat washer M12 (#6), spring washer M12 (#5) and nut M12 (#4) from
one of the supports (#1).
4.2.4.
Position the support (#1) onto the frame (#43) and secure with hex head screw M12 x 35 (#2), flat washer M12 (#6), spring washer
M12 (#5) and nut M12 (#4) loosely.
4.2.5.
Follow section 4.2.4 to attach the other support (#1).
4.2.6.
Repeat sections 4.2.1 to 4.2.5 to attach the other base assembly.
4.2.7.
On a flat level floor, level the frame using a good quality spirit level. Fully tighten all fixings.
4.2.8.
Remove the load slings and store them in a safe and secure location.
WARNING!
Take care and seek assistance from another person when lowering and levelling the frame assembly onto the floor.
4.3.
ATTACH THE HAND WINCH ASSEMBLY
WARNING!
Seek assistance from another person with this task as the hand winch assembly is heavy.
4.3.1.
Transfer the hand winch assembly (#12) from its transport location by firstly removing the fixings, hex head screw M12 x 35 (#2),
flat washer M12 (#6), spring washer M12 (#5) and nut M12 (#4) from hand winch support (#13). Retain the fixings.
4.3.2.
Move the hand winch assembly (#12) to the outside of the left hand post (position H on the parts diagram) and secure with the
retained fixings, loosely.
4.3.3.
Ensure that the cables are located correctly in the rollers prior to fully tightening fixings.
4.4.
ATTACH THE PUMP ASSEMBLY
WARNING!
Seek assistance from another person with this task as the pump assembly is heavy.
NOTE:
The pump assembly (#53), air hose (#59), foot pedal (#61), air hose (#65), quick coupler (male) (#75) and short hose (#56)
are supplied pre-assembled.
4.4.1.
Transfer the pump assembly (#53) from its transport location by firstly removing the fixings, hex head screw M10 x 45 (#54) and flat
washer M10 (#15). Retain the fixings.
4.4.2.
Attach the pump assembly (#53) into position at the top, right hand side of frame (#43) and secure with the retained fixings.
4.5.
ATTACH THE PUMP HOSE.
NOTE:
The short hose C (#56) is pre-assembled to the pump (#53).
4.5.1.
Remove the dust plug from the end of short hose (#56).
DO NOT
discard.
4.5.2.
Attach short hose (#56) to gauge fitting (#51) at position A on the parts diagram.
4.6.
ATTACH THE OIL HOSE
NOTE:
The oil hose B (#58) is pre-assembled to the ram (#46).
4.6.1.
Remove the dust plug from the end of oil hose (#58).
DO NOT
discard
4.6.2.
Remove the dust plug from the oil filler nut (#74) and attach the oil hose (#58), at position B on the parts diagram.
4.6.3.
IMPORTANT
: Open transit plug, for use, located on top of pump assembly.
Original Language Version
© Jack Sealey Limited
YK759FAH.V2 Issue 1 01/08/22