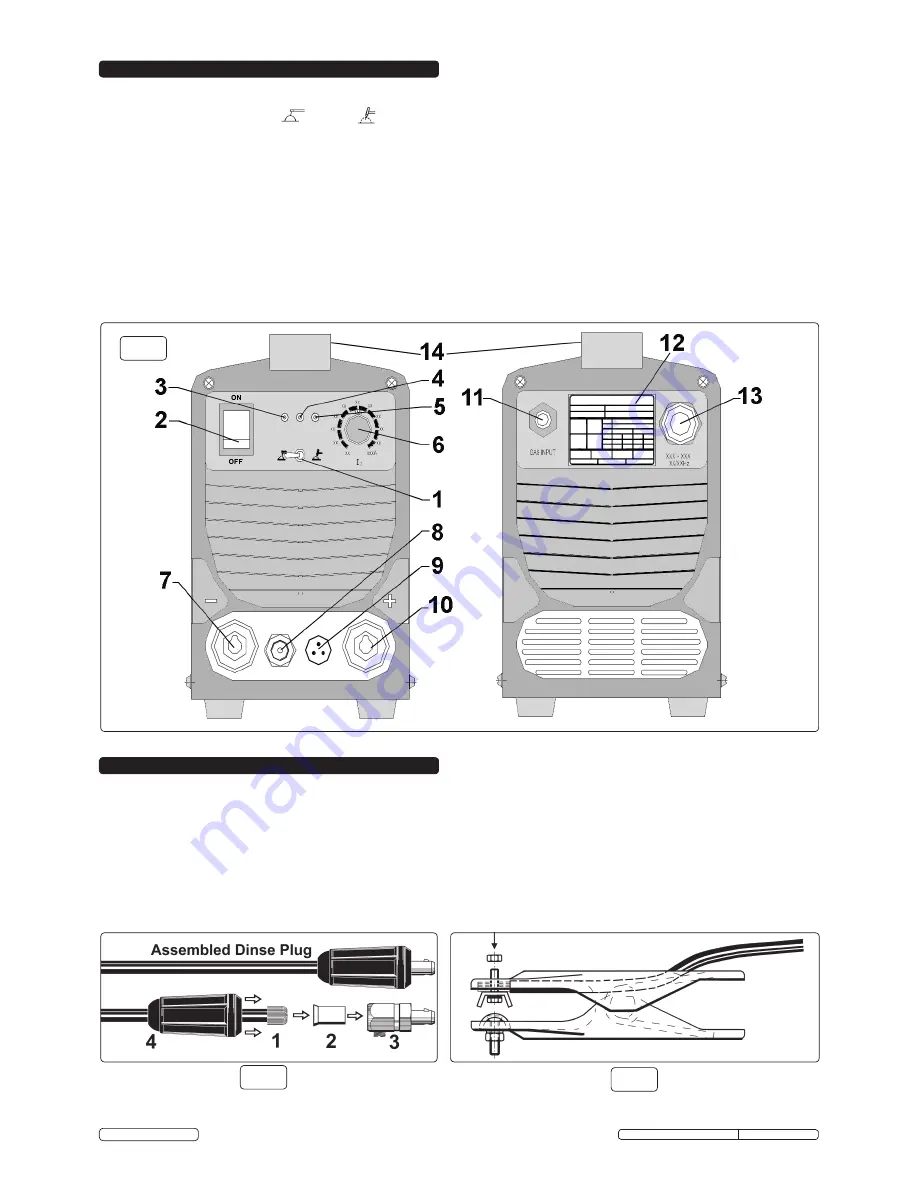
4. PREPARING INVERTER FOR USE
3. CONTROLS
3.1. FRONT AND REAR PANEL LAYOUT (fig.2).
1.
OPERATING SWITCH - MMA
(left) /
TIG
(right) selection.
2.
MAIN ON/OFF SWITCH
.
3.
GREEN LED
- illuminates to indicate that power is on.
4.
YELLOW LED -
illuminates to indicate that the machine is locked:
Thermal Relay.
The temperature inside the welder is too high. The welder will
reset its standard default settings automatically when cool (duty cycle, see section 2.2 for duty cycle percentages).
5.
RED LED -
illuminates to indicate welder is working.
6.
CURRENT SELECTOR DIAL.
7.
DINSE SOCKET
(negative
-
). For the connection of a welding cable Dinse plug.
8. GAS OUTPUT.
9. TORCH CONTROL WIRE CONNECTION.
10. DINSE SOCKET
(positive
+
). For the connection of a welding cable Dinse plug.
11. GAS INPUT.
12. RATINGS PLATE.
13. MAINS INPUT CABLE.
14. HANDLE.
4.1.
CONNECTION TO THE MAINS.
Connection to at least a 32Amp fused supply is recommended. Seek the advice of a qualified electrician for
connection to a suitable supply.
4.2.
WELDING CABLE CONNECTIONS.
The torch cable is supplied ready assembled but it may be necessary for you to assemble the work clamp cable.
Attach the work clamp to one end of the cable as shown in fig.4. To connect the Dinse Plug as shown in fig.3 first thread the cable through the outer
cover of the plug (see fig.3 - 4). Now remove 20mm of insulation sheath from the end of the cable and fold back the copper wire all around the outside of
the sheath (1). Push the cable end into the copper sleeve (2) so that the folded back wire makes good contact with the inside of the sleeve. Push the
copper sleeve into the brass plug body (3) and tighten the large grub screw until the cable is firmly held. Now slide the outer plug cover up the cable and
press the brass body into it as shown in fig.3.
fig.3
fig.4
fig.2
Original Language Version
TIG160S, TIG180S, TIG200S Issue: 1 - 05/06/13
© Jack Sealey Limited