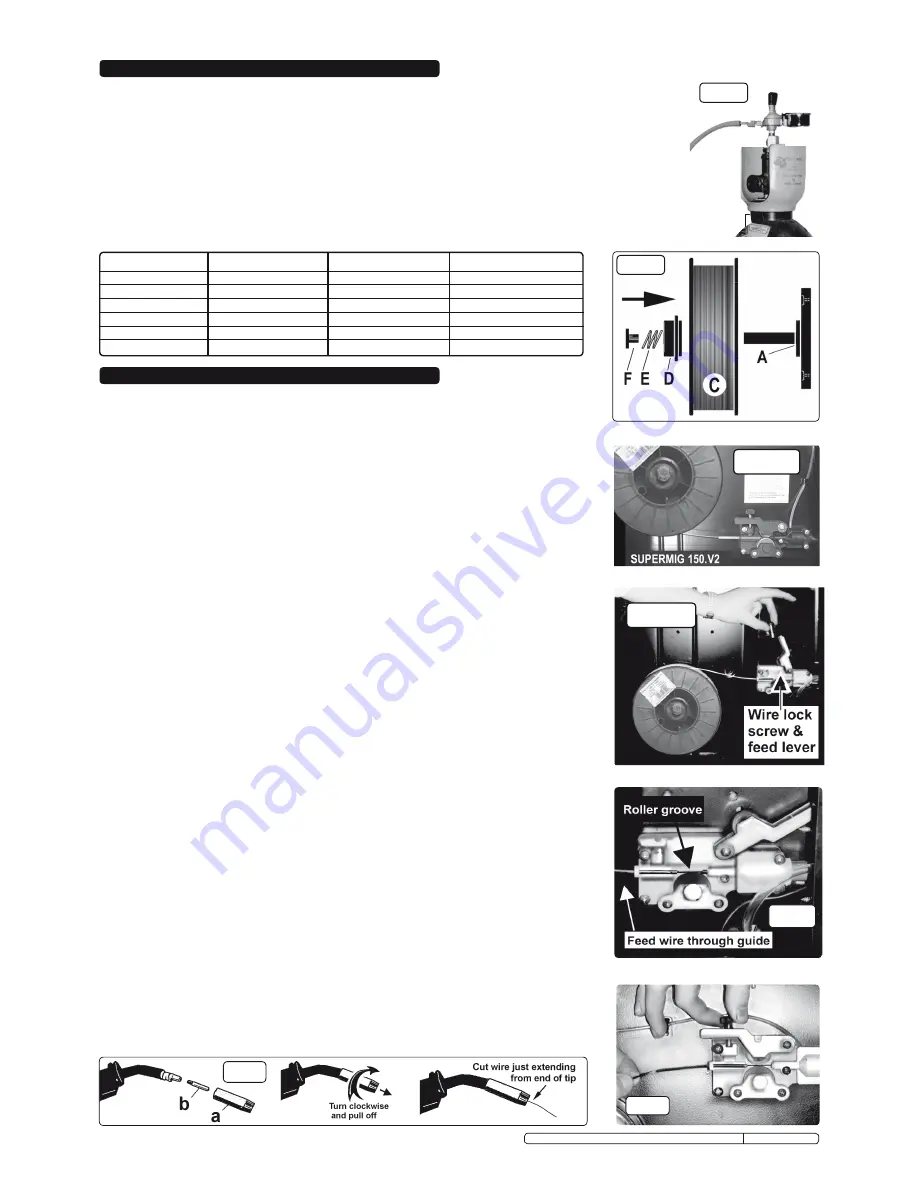
3. 1.
Wheel Assembly
3. 1. 1.
Turn machine upside down and remove the screws attached to the bottom front, use these screws
to attach the front castor wheels.
3. 1. 2.
Take the rear axle and fit a wheel to one end by placing a washer, then the wheel, a second
washer and then insert a split pin.
3. 1. 3.
Pass the axle through the tube under the gas cylinder carrier, then fit the other washer, wheel,
washer, and split pin.
3. 2.
Connecting the gas cylinder
3. 2. 1.
When using Argon or Argon mixtures, you will need to use the “bull nose adaptor”. Fit the bull
nose adaptor to the cylinder with a spanner. (If you intend to use CO² gas the regulator will fit
directly onto the cylinder.)
3. 2. 2. Fit the gas regulator on to the bull nose adaptor and connect it to the machine gas hose (fig.1).
3. 2. 3. When you are ready to weld set the regulator flow rate to 5-8 litres/min depending on the material
to be welded, and whether there are draughts which are strong enough to disturb the gas flow.
3. 3.
Fitting a reel of wire.
The welder is supplied with a mini spool of mild steel wire, but will accept
spools of up to 5kg without modification.
3. 3. 1.
Small reels of wire will run on the spindle itself. The larger 5kg wire reel will run on the larger
diameter flange at the base of the reel spindle. Place the wire reel (C) onto the spindle ensuring
that the spool rotates anticlockwise with the wire drawing off the bottom of the reel for the
SUPERMIG 150.V2 (see fig.3a) and clockwise, with the wire drawing off the reel from the top for
the 160.V2 and 180.V2 models (see fig.3b). Place the plastic reel ring nut (D) over the end the
spindle followed by the reel spring (E). Push the ‘handwheel’ stub (F) into the end of the spindle
against the spring pressure and turn and release it to lock it in position.
3. 3. 2.
Undo the wire lock screw and lift the wire feed lever up to the right (fig 3b).
3. 3. 3. Straighten 40-50mm of spool wire (
do not allow wire to uncoil
), and gently push wire through the
plastic guide and through the 6 or 8mm feed roller groove and into the torch liner (fig 4). Refer to
section 6.3 on how to reverse the roller for either 6 or 8mm wire
3. 3. 4.
Carefully return the wire feed lever and secure with the wire lock screw.
3. 3. 5.
Feeding the wire through to the torch.
(See fig.5)
Remove gas cup (a) and contact tip (b) from end of torch as follows:
a) Take torch in left hand with the torch tip facing to the right.
b) Grasp gas cup firmly in your right hand.
c) Turn gas cup
clockwise only (c)
and pull cup out to the right.
WARNINg!
do not turn gas cup anti-clockwise, as this will damage internal spring.
d) Unscrew the copper contact tip (
right hand thread
) to remove.
3. 3. 6. Check welder is switched off “0”, and that the earth clamp is away from the torch tip. Connect the
welder to the mains power supply and set the voltage switch to one.
3. 3. 7. Set the wire speed knob to position 5 or 6. Keeping the torch cable as straight as possible and
press the torch switch. The wire will feed through the torch.
3. 3. 8.
When wire has fed through, switch welder off, unplug from mains.
a) Take torch in left hand and screw contact tip back into place.
b) Grasp gas cup in right hand, push onto torch head and turn
clockwise only
.
WARNINg!
do not turn gas cup anti-clockwise, as this will damage internal spring.
c) Cut wire so that it is just protruding from the cup.
3. 4.
Setting wire tension
IMPORTANT: You must set the correct tension, too little or too much tension
will cause problematic wire feed and result in poor welding.
3. 4. 1. For mild steel 0.6mm wire the wire lock screw must be fully tightened and undone approximately
two complete turns (fig 6).
3. 4. 2. Correct tension between the rollers is checked by slowing down the wire between the fingers. If the
top feed roller skids the tension is correct. Try to use the lowest tension possible as too high a
tension will disfigure the wire and may result in blowing a fuse on the printed circuit board. When
you have completed welding, remove the torch and store in a safe, dry place.
Note: Damaged torches and cables are not covered under warranty.
Fig.6
Fig.3b
Fig.4
Fig.5
3. ASSEMBlY
To fit the mains power plug see safety instructions (Chapter 1).
c
2. INTROdUCTION & SPECIFICATION
SPECIFICATION
SUPERMIG 150.V2
SUPERMIG 160.V2
SUPERMIG 180.V2
Welding Current
30-150 Amps
30-160 Amps
30-180 Amp
Duty Cycle
100% @ 30A
100% @ 45A
100% @ 60A
80% @ 50A
60% @ 80A
60% @ 80A
50% @ 70A
20% @ 130A
20% @ 140A
10% @ 150A
10% @ 150A
10% @ 155A
Absorbed Power
4.3 kW
3.7 kW
5.2kW
IMPORTANT:
These instructions contain information you require to prepare your machine for welding, together with maintenance
and a trouble shooting section.If you have no previous experience the instructions are not intended to show you how to become a
welder . Should you have no experience, we recommend that you seek training from an expert source. Mig welding is relatively
easy to perform, but does require a steady hand and time practising under supervision with scrap metal as It is only with continued
practice that you will achieve the desired results.
All our Supermig models are suitable for welding with either CO2, Argon or CO2/Argon mix gas. Each uses a forced air cooling
system to slow transformer heating in order to increase duty cycle and a non live torch to prevent the risk of accidentally striking an
arc. All models are supplied with an industrial Argon/CO2 regulator. Welders are illustrated with gas bottles to give an indication of
size only; gas is not included. A contract for the supply of gas should be arranged with your local gas distributor. These Supermigs
are compact power sources with integral wire feed which protects the wire from dust and dirt (especially in Body Shops). Your
Supermig is designed to operate with two diameters of welding wire, 0.6mm, & 0.8mm. (We recommend that 0,8mm wire is used for
welding stainless steel and aluminium).
ALL MODELS ARE EqUIPPED WITh:
Torch,
Mini reel of 0.6mm wire,
Regulator,
Gas hose.
Fig.1
Fig.2
Fig.3a
Original Language Version
SUPERMIG150.V2, SUPERMIG160.V2, SUPERMIG180.V2 Issue: 3 - 09/04/10