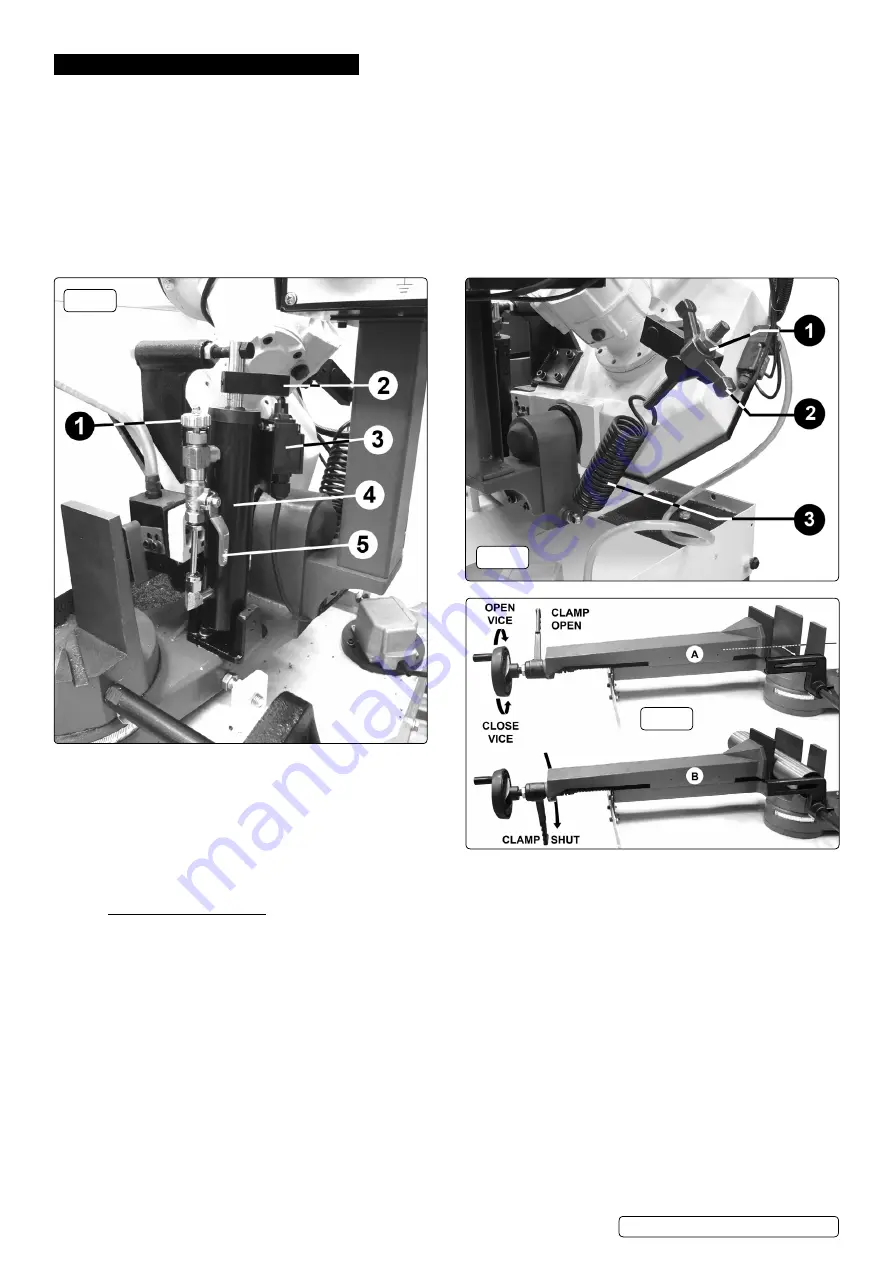
5. ADjUSTMENTS
5.1.
COOLANT
5.1.1.
The use of a water soluble coolant will increase cutting efficiency and prolong blade life. Five litres of soluble cutting oil can be
ordered under sealey Part. no. sco5l (follow instructions on pack regarding use and precautions).
5.1.2.
coolant is drawn from the coolant tank by the coolant pump (see fig.4 - 19) and fed through a clear plastic tube to a valve situated
on the top edge of the bow casting (see ‘8’ in Fig.4). When the valve is opened the coolant is fed down two separate pipes which
deliver the coolant directly into each blade guide. The coolant is then deposited onto the machine bed where it flows to the lower level
and returns to the coolant tank through the grill situated above it for recirculation.
5.1.3.
The coolant tank can be first filled by pouring the liquid directly through the grill. When the coolant becomes dirty and particle laden it
can be drained from the tank through a drain plug situated at the bottom edge of the machine bed on the right hand side. remember to
replace the drain plug before filling with fresh coolant.
5.2.
HYDRAULIC BOW DAMpER
5.2.1.
the rate of descent of the main cutting arm (bow) is controlled by the cylinder (4) shown in fig.5 below.
5.2.2.
By turning the knob (1) clockwise the rate of descent is slowed down. By turning the knob anticlockwise the rate of descent is
increased. The bow can be locked in any position by turning the hydraulic flow off using the tap (5). When the tap is at 90° to
the cylinder the flow is off and the bow will stop moving.
5.2.3.
Automatic electric shut off.
When the bow reaches its lowest point the actuation arm (2) operates the microswitch (3) and the power
is shut off bringing the blade to a halt.
5.3.
ADjUSTING BOW WEIGHT
(See fig.6)
5.3.1.
Bow weight is one of the most important adjustments on the saw. Incorrect bow weight can result in poor performance
including rough
or crooked cuts and premature dulling of the blade. The hydraulic feed rate unit will not compensate for improper bow weight. Bow weight
is factory set and should not normally require adjustment.
5.3.2.
if performance problems are encountered adjust the bow as follows:
5.3.3.
turn the hydraulic cylinder valve on and place the saw arm in the horizontal position.
5.3.4.
turn the feed rate valve at the top of the cylinder anticlockwise until it stops.
5.3.5.
Adjust the spring tensioner in Fig.6 to the required setting for the stock being cut. Turn handle ‘2’ clockwise to slow down the rate of
descent.
5.4.
VICE SET-Up AND ADjUSTMENT (See fig.7)
5.4.1.
Adjust the vice opening to be larger than the material to be cut using the hand wheel at the left hand side of the vice assembly. turn the
handwheel clockwise to close the vice. turn the hand wheel anticlockwise to open the vice.
5.4.2.
Adjust the position of the stop bracket on the stop rod so that the distance from the end of the bracket to the blade is the same as the
length of material to be cut as shown in ‘A’.
5.4.3.
lift the bow so that the blade is not passing through the vice and lock the position with the tap on the hydraulic unit. Place the metal stock
to be cut into the vice so that it is up against the stop bracket as shown in ‘B’. Close the vice to within 2mm of the material. Finally
clamp the material in place by sharply moving the clamp lever downwards (anticlockwise).
Fig.5
Fig.6
Fig.7
s
M354CE | Issue:4 (H,F) 16/02/18
Original Language Version
© Jack sealey limited