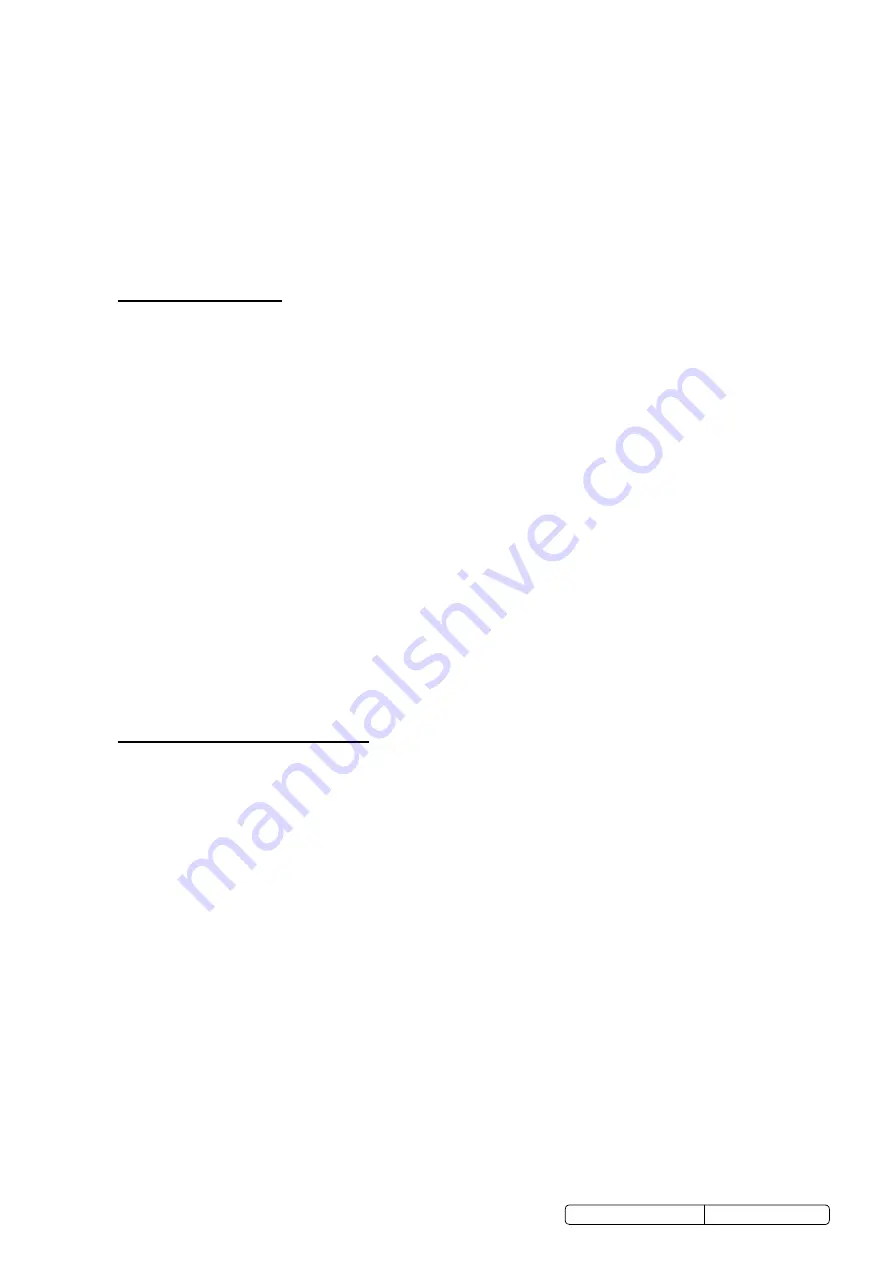
fig.9B
6.8.3.
if the light does not illuminate release the emergency off switch by twisting the button clockwise until it disengages.
6.8.4.
rotate the rotary speed switch slowly clockwise. As the knob is turned a click will be heard and the motor will start. As the knob is
turned further the speed will increase. set the knob to the desired speed.
6.8.5.
Stop modes.
there are three ‘stop’ modes as described below.
(A). to stop the machine for a short while and then restart, simply return the rotary speed switch to the ‘0’ position. When you are
ready to restart, rotate the switch clockwise to the desired speed.
(B) if the machine is to be left unattended for any length of time, switch the forward/reverse switch to ‘off’ as well as returning the
speed switch to ‘0’.
(c) in an emergency hit the large red emergency button which automatically cuts the electrical supply to the machine. Before the
machine will start again the rotary speed switch must be returned to the ‘0’ position and the emergency switch must be released.
6.8.6.
in case of an irregularity, the machine will shut off (the emergency switch will cut the power) and the fault light (see fig.3-2A) will
illuminate. in order to restart the process, attend to what caused the irregularity, turn the forward/reverse switch to the off
‘0’ position, turn the speed switch to ‘0’ and turn the emergency switch clockwise. the fault light should go out and the lathe
can be started as in 6.8.4. above.
6.9.
Setting Up for Drilling. (Disconnect the machine from the power supply while setting up.)
6.10.
engaging rapid drill feed.
the rapid drill feed is controlled with the lever on the right hand side of the head, (see fig.3-17.) the rapid
drill feed will not operate if the vertical fine feed wheel used for milling is still engaged. to make the rapid drill feed operative pull the
feed selector knob outwards,
(see fig.3-8)
6.11.
mounting the chuck and arbor.
if the milling cutter and arbor are currently mounted, remove them by loosening the arbor bolt by two
turns and giving it a tap with a rubber mallet. Access the arbor bolt by pulling off the plastic cap which covers the top of the spindle
shaft and place an 8mm spanner onto the flats at the top of the shaft. insert a rod into the hole in the side of the spindle shaft (see
fig.4-4) to prevent it turning and loosen the arbor bolt by two turns. Give the arbor bolt a sharp tap with a rubber mallet in order to
release the arbor from the internal taper. continue to unscrew the arbor bolt by hand whilst supporting the milling cutter and arbor until
they become loose and can be removed. (
wear protective gloves.
) insert the chuck arbor into the bottom of the spindle shaft and
retain it with the arbor bolt. do not over tighten. the drill chuck is a shallow taper fit onto the end of the drilling arbor. using the chuck
key open the jaws of the chuck until they withdraw inside the chuck body. Place a piece of wood onto the cross feed bed and position
the chuck on it below the spindle shaft. using the drill feed, wind the spindle shaft down until the arbor enters the chuck. exert firm but
not excessive downward pressure on the chuck to retain it on the arbor.
6.12.
Drill bits.
insert an appropriate drill bit into the chuck and tighten the chuck with the chuck key. remove the chuck key.
6.13.
attaching the workpiece
. the cross feed bed of the machine has 2 inverted 8mm ‘t’ slots in it for fixing the workpiece or any vice/
clamping arrangement used to hold the workpiece.
6.14.
altering the height of the head.
if the tip of the drill bit is not close enough to the workpiece alter the height of the head on the
column as described in section 6.5.
6.15.
Speed control and on/off operation.
refer to section 6.8 for the operation of the main on/off switch and speed setting.
6.15.1. Avoid subjecting drills and cutting tools to excessive strain. do not apply undue force on the handle in order to cut the workpiece.
maintain a controlled cutting speed through the workpiece
.
6.16.
Setting Up for CUtting on the lathe.
(disconnect the machine from the power supply while setting up.)
6.17.
the chuck.
the chuck is attached to the faceplate with 3 studs and nuts. check that these fixings are secure before proceeding. the
chuck is provided with two sets of jaws for either external or internal holding of objects to be turned. select and fit the appropriate
jaws. using the chuck key wind out the jaws to their maximum extent at which point they can be pulled out by hand. the thread
segments are staggered differently on each jaw and therefore the jaws are numbered 1 to 3. insert the jaws in sequence beginning
with no1 and in an anti clockwise direction as you face the chuck. Hold them under pressure whilst turning the key until they are
picked up by the mechanism and start to move towards the centre of the chuck. check that the three jaws come together correctly at
the centre of the chuck. if not, wind the jaws out again and press on the misaligned jaw until it drops into place.
6.18.
tailstock/centre.
material/stock that is too long to be held in the chuck alone can be steadied by a centre fitted into the tailstock.
once one end of the workpiece is fixed into the chuck loosen the two socket cap screws holding the tailstock and slide it up to the
unsupported end of the workpiece so that the centre is close to it. tighten the tailstock socket cap screws. now wind the tailstock
wheel so that the centre makes contact with the end of the workpiece and lock its position by tightening the tailstock lock, (see
fig.3-20.)
6.19.
toolrest.
mount the toolrest utilising the ‘t’ slots in the cross feed table. insert an appropriate cutting tool into the split carrier and
mount the tool and carrier into one side of the toolrest. now make any necessary adjustments to the position of the toolrest and
carrier to allow the cutting edge of the tool to be correctly presented to the workpiece. the tool should be cutting in a plane that
passes through the centre axis of the workpiece or just below it.
the angle of the tool when viewed from above may be changed by loosening the central holding bolt on the toolrest and twisting the
whole rest on the bed to obtain the desired angle.
6.19.1. one side of the toolrest will clamp the tool and carrier parallel to the bed of the machine. on the other side of the toolrest the tool and
carrier rests on a contoured block which allows the tool to be inclined upwards or downwards by a few degrees. the angle of tilt is
controlled by adjusting the two socket cap bolts which bear on the tool carrier.
6.19.2. Adjust the crossfeed wheel and longitudinal feed so that the tip of the tool is in the correct position to commence cutting when the
machine is turned on. Before turning on check that all fixings holding the tool are tight.
sm2503A, sm2503B issue:1 - 21/09/15
Original Language Version
© Jack sealey limited