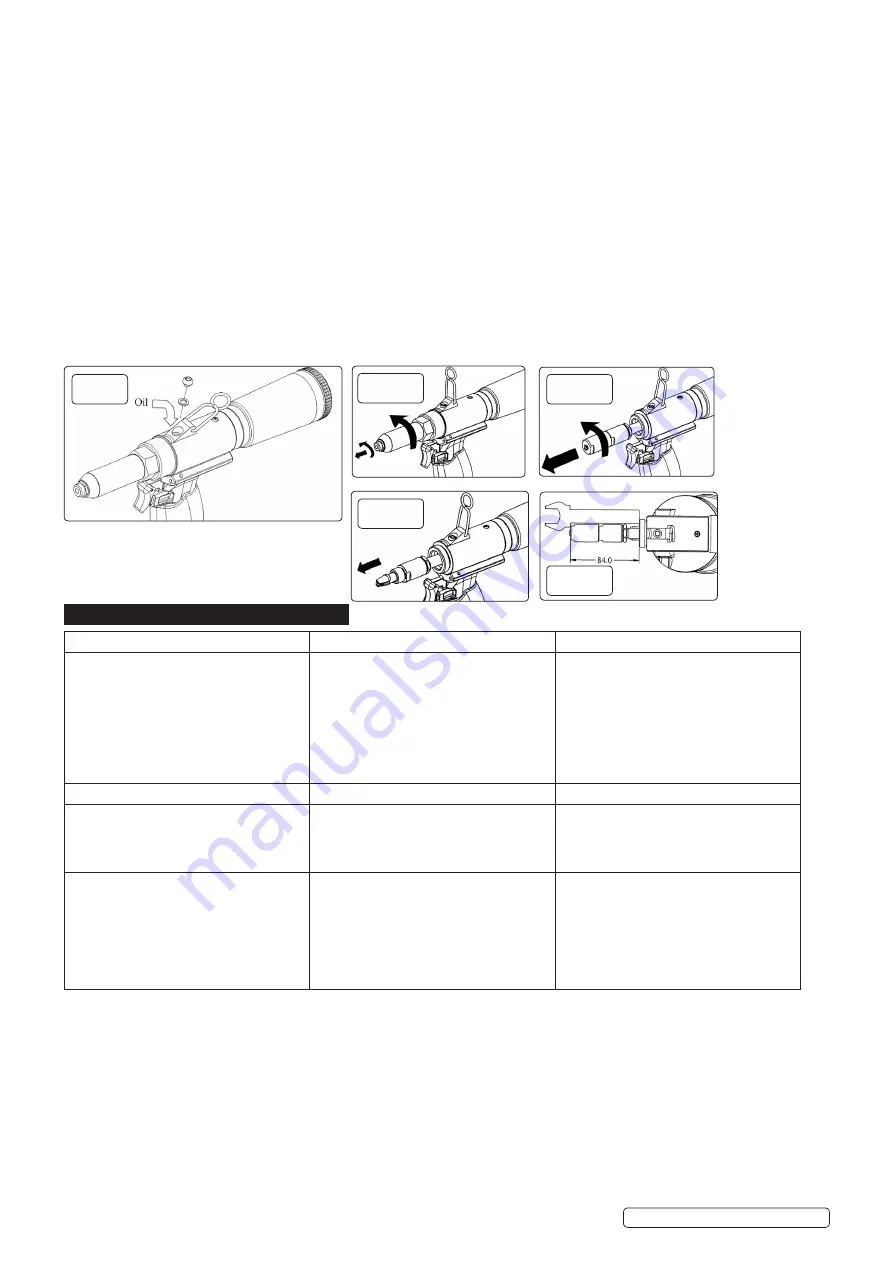
6.3.
JAW REPLACEMENT
6.3.1.
Eventually the jaws will wear and require replacement.
6.3.2.
Remove the nozzle and frame head (Fig.6) using the supplied spanners.
6.3.3.
Undo and remove the jaw housing from the jaw housing coupler (Fig.7).
6.3.4.
Withdraw the jaws and replace with a new set. If the jaw pusher and spring fall out, put the spring back first and then the jaw
pusher followed by the jaws. For a further reference consult the parts diagram at the back of this manual for correct part
orientation.
6.3.5.
Fit the frame head and tighten.
6.3.6.
When the jaws are replaced check that the jaw distance from the main body is 84mm using the guide on the spanner as shown in
Fig.9.
6.4.
FACTORS THAT MAY INHIBIT PERFORMANCE
6.4.1.
Loss of power or erratic action may be caused by reduced compressor output, an excessive drain on the air line, moisture or
restrictions in air pipes or the use of hose connections of improper size.
6.4.2.
Grit or gum deposits in the tool may cut power and can be corrected by cleaning the air strainer and flushing out the tool with gum
solvent oil or an equivalent de-greaser.
6.4.3.
If all outside conditions are in order, disconnect the tool from the air supply, disassemble and replace any worn or damaged parts
with Sealey original parts.
6.4.4.
Clean all parts, reassemble the tool and lubricate.
6.5.
Store the tool in a safe, dry, secure environment.
7. TROUBLESHOOTING
Oil
Fig.5
Problem
Cause
Remedy
R
ivet jammed.
Wrong size rivet/nozzle.
F
ilings jammed in jaw housing.
F
ilings jammed in nozzle.
Use correct size nozzle for the rivet.
S
nap off rivet head, dismantle jaw housing
and pull out the rivet mandrel. Use an
airline to blow out the filings, oil and
reassemble the jaw housing.
Clean out the nozzle.
No suction.
T
he shut-off valve has not been opened.
O
pen shut-off valve.
Air leaking.
Loose screws.
D
amaged O-rings.
Tighten screws.
O
-rings must be replaced.
Tool runs slow or suffers a loss of power.
Air line is loose.
Exhaust port is blocked.
Operating pressure is too low.
R
e-install and tighten air line.
Clean out exhaust port.
I
ncrease the operating pressure to 85-
95psi. If the pressure exceeds 105-110psi,
the safety valve will operate.
Fig.6
Fig.7
Fig.8
S
A316.V3 | Issue 1 12/05/15
Original Language Version
© Jack Sealey Limited
Fig.9