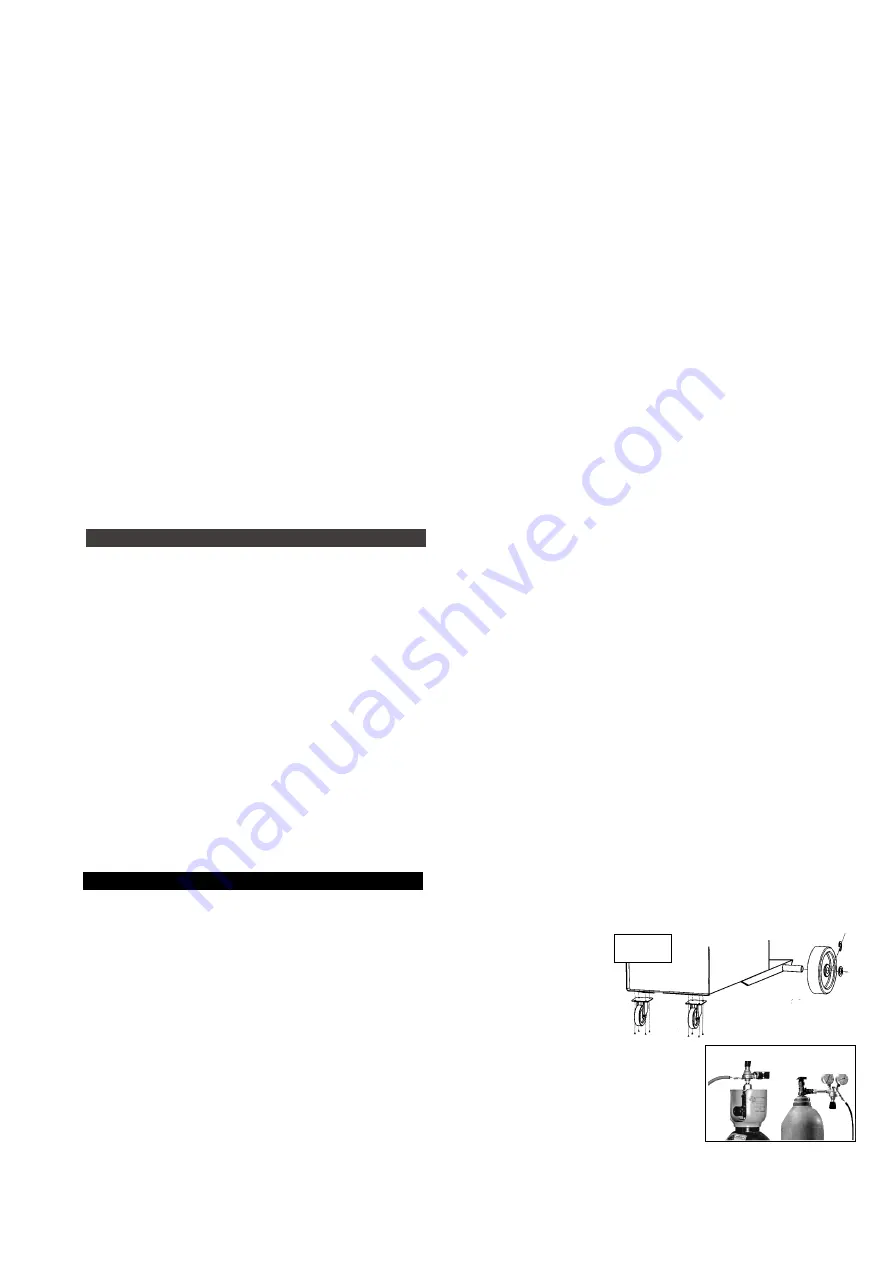
Tried and trusted by fabricators and professional car repair shops across the UK. Superb quality, Swedish made electronic wire drive motors and heavy duty
transformers make these machines unmatched in performance and value. The Powermig 2500 is the most powerful mig in our range capable of operating on 230
Volt single phase input. Just check the specifications. Ideal for industrial use where 400/440V 3ph is not available. Other models are 415V 3 phase machines. Each
unit comes with 0.8mm steel wire, non live torch and industrial Argon/CO
2
regulator. All can be used with CO
2
, Argon or Argon mix gas and accept any bottle size.
2. INTRODUCTION & SPECIFICATIONS
IMPORTANT:
These instructions contain information you require to prepare your machine for welding, together with maintenance and a trouble shooting section.
If you have no previous experience the instructions are not intended to show you how to become a welder. Should you have no experience, we recommend that you
seek training from an expert source. Mig welding is relatively easy to perform, but does require a steady hand and time practising under supervision with scrap metal
as it is only with continued practice that you will achieve the desired results.
1.4
GENERAL SAFETY
s
s
s
DANGER!: unplug the welder from the mains power supply before performing maintenance or service.
3
Keep the welder and cables in good working order and condition.
(Take immediate action to repair or replace damaged parts).
3
Use genuine parts and accessories only.
(Non recommended parts may be dangerous and will invalidate the warranty).
3
Use an air hose to regularly blow out any dirt from the liner, and keep the welder clean for best and safest performance.
3
Check and spray the gas cup and contact tip regularly with anti-spatter spray available from your Sealey dealer.
3
Locate welder in adequate working area for its function. Ensure area has adequate ventilation as welding fumes are harmful.
3
Keep working area clean, tidy and free from unrelated materials. Also ensure the working area has adequate lighting, and that a fire extinguisher is at hand.
p
p
p
WARNING: use welding head shield to protect eyes and avoid exposing skin to ultraviolet rays given off by electric arc. Wear safety welding gauntlets.
3
Remove ill fitting clothing, remove ties, watches, rings, and other loose jewellery, and contain long hair.
3
Ensure the workpiece is correctly secured before operating the
welder.
3
Avoid unintentional contact with workpiece. Accidental or uncontrolled use of the torch may be dangerous and will wear the nozzle.
3
Keep non essential persons away from the working area. Any persons working within the area must use protective head shield and gloves.
3
Operators must receive adequate training before using the welder. The welder must only be operated under supervision.
3
Stand correctly keeping a good footing and balance, and ensure the floor is not slippery, and wear non-slip shoes.
3
Turn voltage switch to "0" or off when not in use.
7
DO NOT operate the welder if it or its cables are damaged and DO NOT attempt to fit any non genuine torches, components, or parts to the welder unit.
7
DO NOT get welder wet or use in damp or wet locations or areas where there is condensation.
s
s
s
DANGER! DO NOT weld near inflammable materials, solids, liquids, or gases, and DO NOT weld containers or pipes which have held flammable
materials or gases, liquids or solids. Avoid operating on materials cleaned with chlorinated solvents or near such solvents.
7
DO NOT stand welder on a metal workbench, car bodywork or similar object.
7
DO NOT touch any live metal parts of the torch or electrode while the machine is switched on.
7
DO NOT pull the welder by the cable, or the torch, and DO NOT bend or strain cables, protect from sharp or abrasive items, and DO NOT stand on cables
or leads. Protect from heat. Long lengths of slack must be gathered & neatly coiled. DO NOT place cables where they endanger others.
7
DO NOT touch the torch or workpiece immediately after welding as they will be very hot. Allow to cool.
7
DO NOT operate welder while under the influence of drugs, alcohol or intoxicating medication, or if fatigued.
3
When not in use store the welder in a safe, dry, childproof area.
1.5.
GAS SAFETY
3
Store gas cylinders in a vertical position only and ensure the storage area is correctly secured.
7
DO NOT store gas cylinders in areas where temperature exceeds 50°C. DO NOT use direct heat on a cylinder. Always keep gas cylinders cool.
7
DO NOT attempt to repair or modify any part of a gas cylinder or valve, and DO NOT puncture or damage a cylinder.
7
DO NOT obscure or remove any official labels from a cylinder. Always check the gas identity before use. Avoid getting gas cylinders oily or greasy.
7
DO NOT try to lift or handle cylinder by its cap, guard or valve. Always keep caps and guards in place and close valve when not in use.
The gas cylinder is heavy, use mechanical lifting equipment. Ensure the cylinder is correctly situated on the welder base stand and secured with chain.
12 level rotary control power selection.
Output Range:
. . . . . . . . . . . .30-250 Amps
Duty Cycle:
. . .25% @ 250A, 30% @ 200A
. . . . . . . . . . .60% @ 150A, 100% @ 120A
Power Supply:
. . . . . . . . . . . .230 Volt 1ph
Power Efficiency:
. . . . . . . . . . . . . .6.6 kVA
Cooling System:
. . . . . . . . . . . .Turbo Fan
Accepts Bottle Size:
. . . . . . . . . . . . . . .All
Spot Welding:
. . . . . . . . . . . . .Timer Fitted
Weight:
. . . . . . . . . . . . . . . . . . . . . . .67 kg
Model POWERMIG2500
10 level rotary power selection.
. . . . . . . . . . . . .35-275 Amps
. .10% @ 260A, 30% @ 240A
.60% @ 160A, 100% @ 130A
. . . . . . . . . . . . . .415 Volt 3ph
. . . . . . . . . . . . . . . . . .8.0 kVA
. . . . . . . . . . . . . . . .Turbo Fan
. . . . . . . . . . . . . . . . . . . . . .All
. . . . . . . . . . . . . .Timer Fitted
. . . . . . . . . . . . . . . . . . .60 kg
Model POWERMIG2750
. . . . . . . .12 level rotary power selection.
. . . . . . . . . . . . . . . . . . . . . .35-350 Amps
. . . . . . . . . . .10% @ 330A, 15% @ 320A
. . . . .25% @ 300A, 60% @ 200A, 100% @150A
. . . . . . . . . . . . . . . . . . . . . .415 Volt 3ph
. . . . . . . . . . . . . . . . . . . . . . . . .12.5 kVA
. . . . . . . . . . . . . . . . . . . . . . . .Turbo Fan
. . . . . . . . . . . . . . . . . . . . . . . . . . . . . .All
. . . . . . . . . . . . . . . . . . . . . . . . . . . .95 kg
Model POWERMIG3500
. .18 level rotary power selection.
. . . . . . . . . . . . . . . .35-450 Amps
. . . . .10% @ 430A, 15% @ 420A
25% @ 400A, 60% @ 260A, 100% @ 200A
. . . . . . . . . . . . . . . .415 Volt 3ph
. . . . . . . . . . . . . . . . . . .18.5 kVA
. . . . . . . . . . . . . . . . . .Turbo Fan
. . . . . . . . . . . . . . . . . . . . . . . .All
. . . . . . . . . . . . . . . . . . . . .110 kg
Model POWERMIG4500
3. ASSEMBLY
Carefully remove outer carton and packing. Be very careful when removing the welding unit from the packing base as the unit is very heavy, we recommend that
unpacking the base and wheel assembly is undertaken by two persons. Check the welder and contents. Should there be any damaged or missing parts contact
your supplier
immediately.
3.1. WHEEL
ASSEMBLY
(fig 3).
3.1.1. For models that do not already have the front caster wheels attached, locate the caster wheels in the
parts box and fix them to the front of the unit.
3.1.2. Take the rear axle and pass through holes in the back gas bottle stand, place wheels on each side
of axle then slip the washer on each end and fix with cir-clips.
3.2. CONNECTING THE GAS CYLINDER.
3.2.1. Stand the gas cylinder on the base at the rear of the welder and secure with chain supplied.
3.2.2. If using Argon or Argon mixtures, you will need to use the bull nose adaptor enclosed. If you intend to use CO2 gas the
regulator will fit directly onto the cylinder. If using the bull nose, fit nose adaptor to the cylinder and tighten with a spanner.
3.2.3. Remove regulator from box and screw it to the bull nose (or CO2 cylinder). Place the small jubilee clip over the rubber hose
from the welder, connect the hose to the regulator BP output and secure with the jubilee clip (fig 4).
3.2.4. Set the regulator flow rate to 4litres/min depending on the material to be welded, also taking into consideration any
draughts which are strong enough to disturb the gas flow.
3.2.5. If the welder is to be stored for a long time always remove the flow regulator.
3.3.
TORCH Euro Connection.
Your welder is fitted with a Euro Connection quick release torch. Simply line the pins in the torch
up with appropriate holes on the front panel connector and push in and tighten the locking nut.
To fit the mains power plug see safety instructions (Chapter 1.).
fig 3
fig 4
POWERMIG2500, 2750, 3500, 4500. - (0051) - (1) - 270100