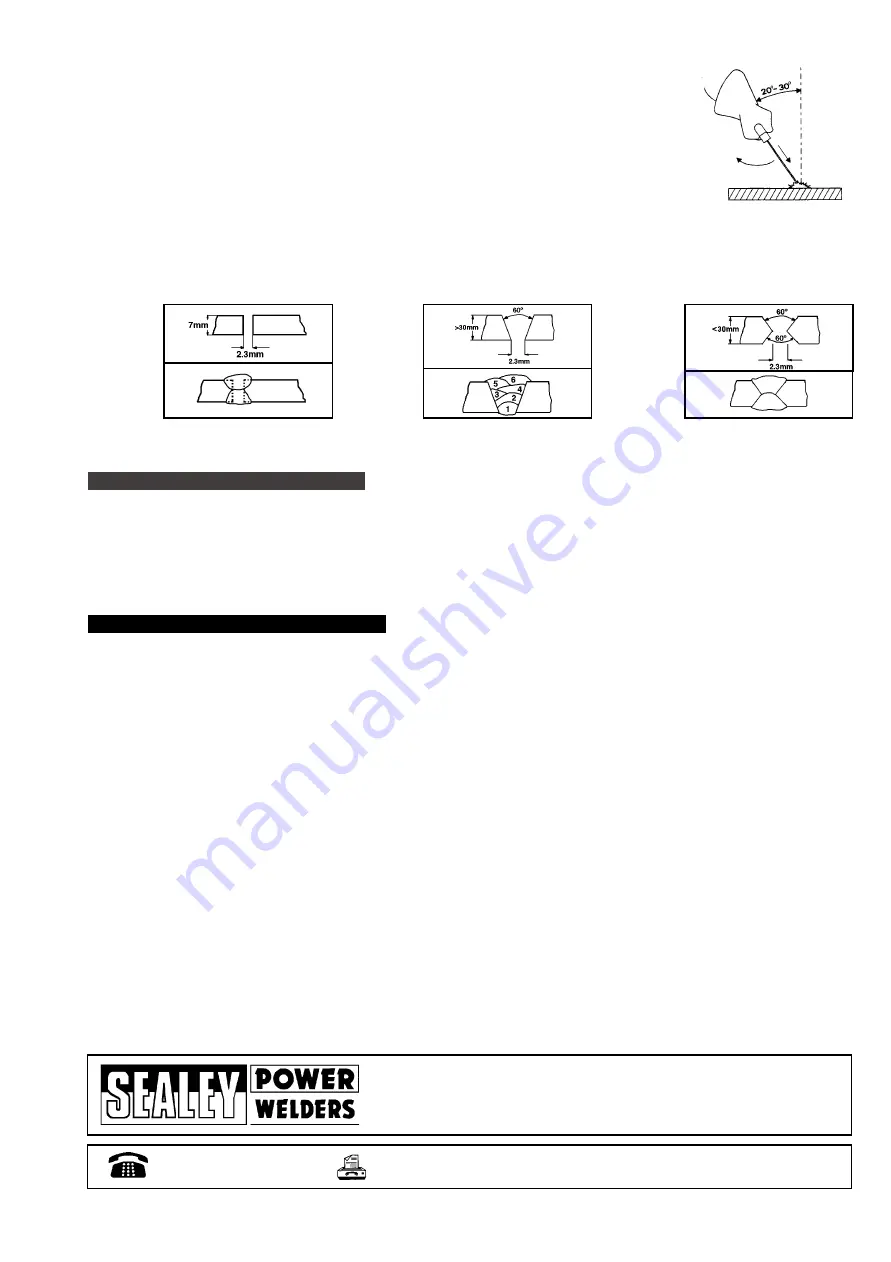
5. MAINTENANCE
6. 1.
Burning through thin metal:
On very thin sheet, e.g. car body work, the lowest amperage setting will be too fierce. In this case
you can still use your welder but you will need a brazing kit which is available from your Sealey stockist, Part Number AK4.
6. 2.
Machine frequently cuts out:
May be caused by a sticking electrode. One sticking electrode could cause the machine to cut out
for up to ten minutes. After this time it should be ready to use again. Or, the machine is being overworked causing the
thermostatic control to activate.
6. 3.
Difficulty in striking an arc:
a). The electrode is damp. Heat it up to 60º - 70º before using.
b). Wrong type of rod.
6.
TROUBLESHOOTING
4.6.1.
Metal up to
7mm thick,
keep pieces 2-
3mm apart. A
2nd run can go
underneath for
extra strength.
4.6.2.
Thickness of
up to 30mm,
make a single
butt joint, filling
up the space
with several
layers of weld.
4.6.3.
Over 30mm,
you need a
double V butt
joint fill up the
space with
several layers
of weld.
4.6. VARIOUS WELDING METHODS
p
p
p
WARNING! Ensure the welder is disconnected from the electrical mains power supply before attempting any service or maintenance.
5.1.
Keep the welder clean and dry at all times. Use a dry cloth to clean the unit.
5.2.
Keep all electrodes clean and ensure all cables are in good condition.
5.3.
Use authorised service agent for any other maintenance or service requirements.
01284 757500
01284 703534
E-mail:
NOTE:
It is our policy to continually improve products and as such we reserve the right to alter data, specifications and component parts without prior notice.
IMPORTANT:
No liability is accepted for incorrect use of this equipment
WARRANTY:
Guarantee is 12 months from purchase date, proof of which will be required for any claim.
INFORMATION:
Call us for a copy of our latest catalogue on 01284 757525 and leave your full name and address including your postcode.
Sole UK Distributor
Sealey Group,
Bury St. Edmunds, Suffolk.
A few minutes practice will ensure that you get used to this and enable you to compensate accordingly.
If the electrode sticks, you may be holding it too close to the work piece. Pull sharply to the left, and then to
the right to free the electrode. After welding, chip off the slag with a chipping hammer (fig 4).
Wear goggles.
Disconnect welder from the mains power supply before resetting the electrode holder.
p
p
p
WARNING! Due hot, use pliers to remove the consumed electrodes or to move the welded pieces.
IMPORTANT - THERMOSTATIC CONTROL:
Your welder is cooled by the circulation of air. As you use larger welding rods you will experience a temporary
current shut off. This is to protect your transformer from overheating. The larger the welding rod, the greater
the current required, consequently, the hotter the machine will become and the quicker it will cut out.
Fig 4
IMPORTANT.
Should you have no welding experience, we recommend you seek training from an expert source to ensure your personal health & safety.
You must familiarise yourself with welding applications and limitations, and specific potential hazards peculiar to welding. Good Arc welding may be achieved only
with continued, supervised practice.
For example:
NOTE:
See separate sheet for part list and diagram.
Arc Welder - (0051) - (1) - 010100