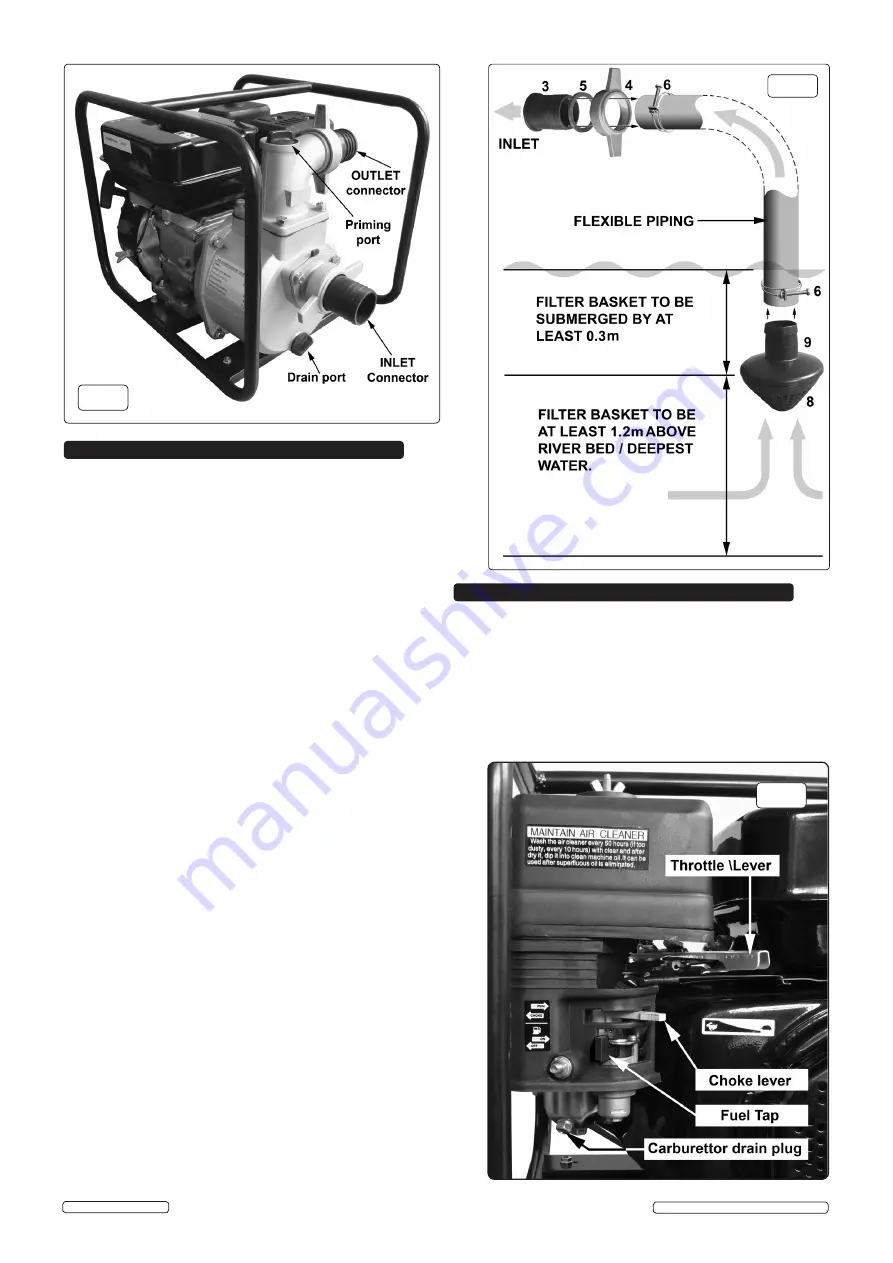
4.1 ASSEMBLE CONNECTORS ONTO PUMP
(See fig.2)
4.1.1 Take the two inlet/outlet connectors (3) and stretch a sealing
washer (5) over each connector and push it down over the ribs
so that it comes to rest on the connector flange.
4.1.2 Insert each connector into the back of a connector locking ring
(4) and push fully home.
4.1.3 Screw one connector assembly onto the pump inlet as shown
above in fig.2. Screw the other assembly onto the pump outlet
as shown above and hand tighten both.
4.1.4 Snap the filter basket cover (9) onto the top of the filter basket
(8) as shown in fig.3.
4.2 CONNECTION TO FLEXIBLE PIPING
(See fig.3)
4.2.1 Bearing in mind the depth of the water to be pumped and the
distance of the pump from the pumping site cut a suitable length
of flexible piping (int.Ø 50mm)
.
4.2.2 Slide a wire hose clamp over one end of the pipe and push the
filter basket assembly fully into the end of the pipe
.
Slide the
wire hose clamp back down over the joint and fully tighten to
retain the filter basket.
4.2.3 Slide a wire hose clamp over the other end of the pipe and push
the pipe fully onto the pump inlet connector
.
Slide the wire
hose clamp back down over the joint and fully tighten.
4.2.4 Cut the required length of flexible pipe for the outlet side of the
pump. Slide a wire hose clamp over the end of the pipe and
push the pipe fully onto the pump outlet connector
.
Slide the
wire hose clamp back down over the joint and fully tighten.
4.2.5 Submerge the filter basket in the water to be pumped. The filter
basket must be at least 0.3m below the surface of the water and
1.2m above the deepest part of the water to prevent debris
blocking the filter basket. (See fig.3). Ensure that the suction
pipe remains in the position intended.
4.2.6 Ensure that the outlet pipe is correctly placed to discharge into
the intended area.
4.2.7
IMPORTANT! Unscrew the cap from the priming port at the
top of the pump and fill the chamber with water. (See fig.2)
Replace the cap.
4.3 CONNECTION TO RIGID PIPING
4.3.1 If the pump is required to service a particular situation on a
permanent or semi-permanent basis it may be plumbed in using
rigid piping connected directly to the threaded inlet and outlet
collars on the pump.
4.3.2 In this situation the pump must be sited on a level, stable
surface such as concrete and the connecting pipework must be
rigidly supported.
4.3.3 The pump must not be placed in an unventilated enclosure
where the exhaust gases cannot escape or may be a breathing
hazard to the operator.
4.3.4 The pump must also be sited to allow good access to all sides
of the unit in order to easily use and service the petrol engine.
4. CONNECTING THE PUMP
5. OPERATING THE PUMP
fig.2
fig.3
fig.4
5.1. MANUAL STARTING PROCEDURE.
5.1.1
IMPORTANT! If the pump has not been primed, do it now,
otherwise the pump may be damaged. See section 4.2.7.
5.1.2 When the machine is new it should be 'run in'. This means
running the unit at low speed and low load for the first 20
hours.
5.1.3 Check engine oil level before each use.
5.1.4 Check that the inlet and outlet hoses are laid straight and
untwisted. Check to ensure there are no leaks from hoses or
connections.
EWP050 Issue :4(L) -10/07/17
© Jack Sealey Limited
Original Language Version