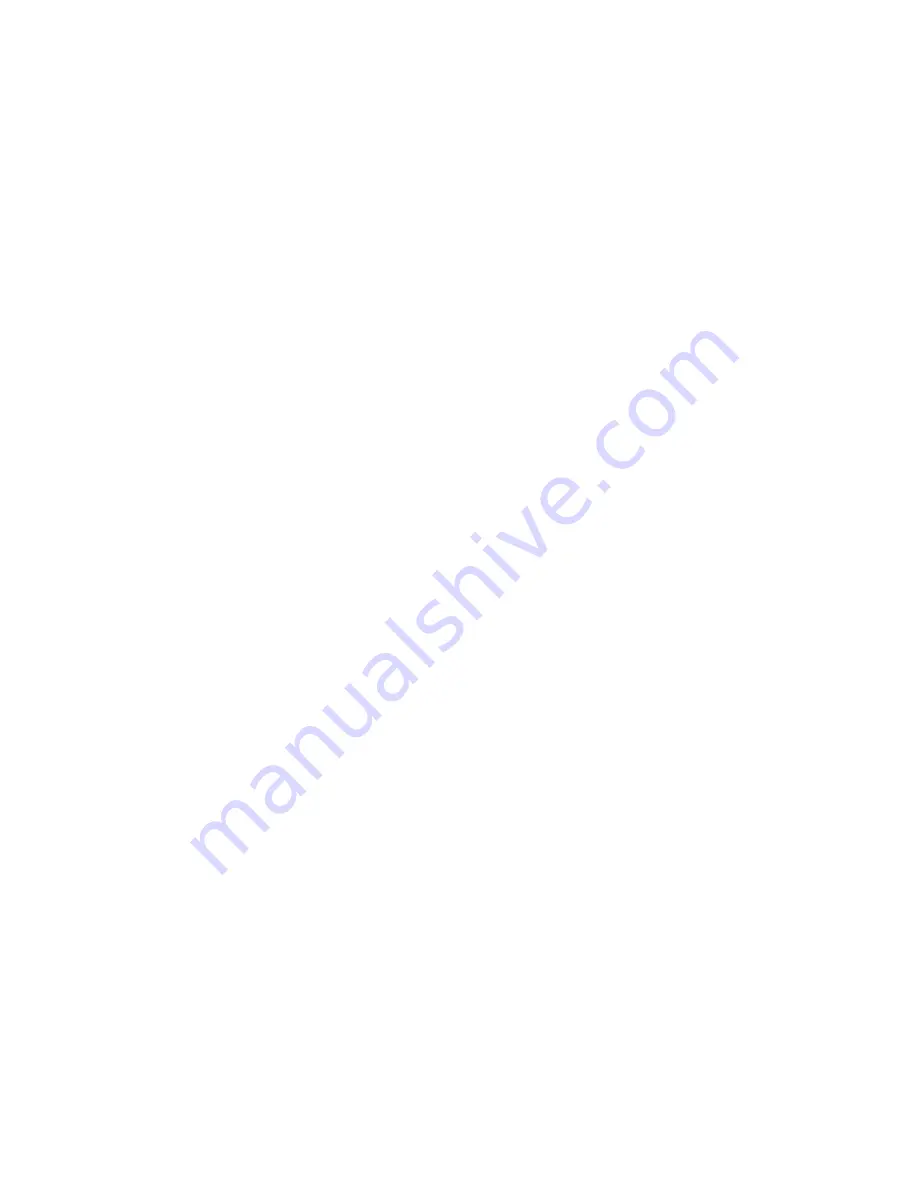
4
User Manual 80
Pro
THIS MANUAL
This manual is intended for the user of the 80
Pro
. Read this manual carefully before
starting the machine.
This manual contains important information for correct installation, operation and
maintenance of the machine.
It also contains important instructions to prevent accidents, personal injury and/or serious
damage prior to or during operation of the machine.
Familiarize yourself thoroughly with the functioning and operation of this machine and
strictly observe the directions given.
If you have any questions or need further details on specific aspects related to this
machine, please do not hesitate to contact us. The address and phone number are stated
on the copyright page.
Chapter 1
will provide you with a summary of the manufacturers warranty information.
It also describes the safety features installed on the machine and gives a number of safety
instruction and warnings.
Read this chapter carefully
.
Chapter 2
provides a general description of the machine and of the process principles to
help first time users to find their way on this machine.
Chapter 3
specifies the machine, machine dimensions and the dimensions of the
materials to be used on this machine.
Chapter 4
guides you through the installation of the machine. This chapter also provides
information for moving, transport and decommissioning of the machine.
Chapter 5
guides you through the operation in various processes to develop basic
knowledge of the machine.
Chapter 6
provides maintenance procedures for long time efficient and trouble free
operation of the machine. The trouble shooting section gives a number of suggestions in
case the results are not up to expectation.
Chapter 7
is the glossary and explains a number of terms used in this manual.
Summary of Contents for 80Pro
Page 2: ...2 User Manual 80Pro...