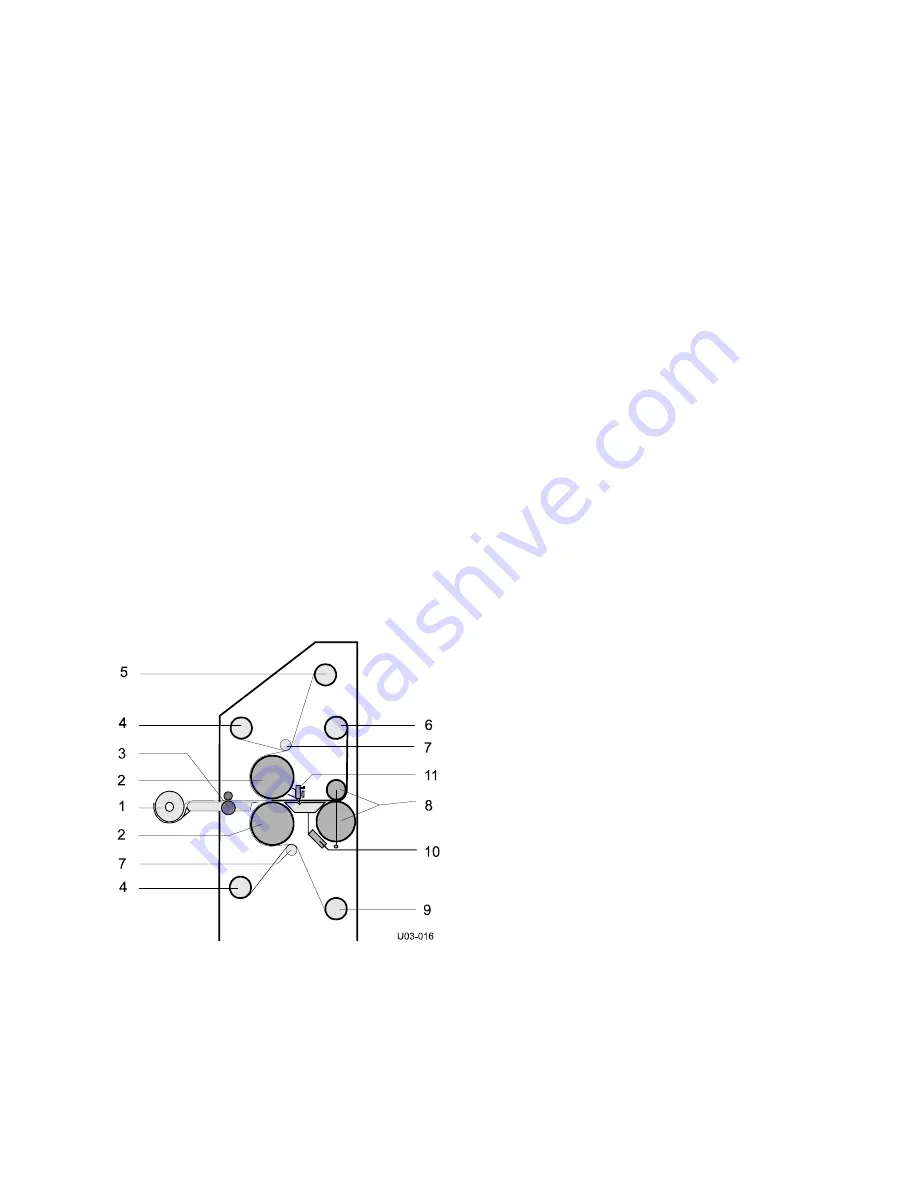
14
User Manual 80
Pro
2.3 Process
principle
In all processes the materials are fed through the nip from the front side to be joined
together by pressure and/or temperature.
A process that makes maximum use of the machine is shown in Figure 4. Shown is an
image roll to roll process with a heat sensitive top and bottom layer.
The image that has to be coated on both sides is unwound from a roll in the in-feed table
trough (1) and fed between the main rollers (2) via the in-feed table rollers (3). The upper
unwind/wind-up shaft (6) is set as a wind-up to roll up the finished product.
The top coating film is taken from a supply roll on the top unwind shaft (5). The bottom
coating film is taken from a supply roll on the lower unwind/wind-up shaft (9).
When using a pressure sensitive laminate, it often has a release liner (as shown in the
upper section) that has to be removed. It runs over a splitter bar (7) where the release liner
is removed. This release liner is rolled up onto a cardboard core placed on the wind-up
shaft (4) in the upper section.
When using a pressure sensitive laminate without a release liner, it must not run via the
splitter bar to avoid getting adhesive residue on it.
The main rollers can be heated. The heat sensitive film is fed under the splitter bar
providing maximum contact surface with the heated main rollers.
When encapsulating (hot sealing images), an additional set of pull rollers (8) is used to
prevent wrinkles after cooling down.
When continuously encapsulating (roll to roll) the pull rollers will warm up slowly. To
prevent this, the cooling unit can be turned on. This cooling unit (10) keeps the bottom pull
roller at room temperature, which in its turn absorbs the heat from the encapsulation result.
The slitters (11) can be used to cut off the edges when processing roll to roll.
Figure 4: Creating Pop-up art, including image supply from roll.
Summary of Contents for 80Pro
Page 2: ...2 User Manual 80Pro...