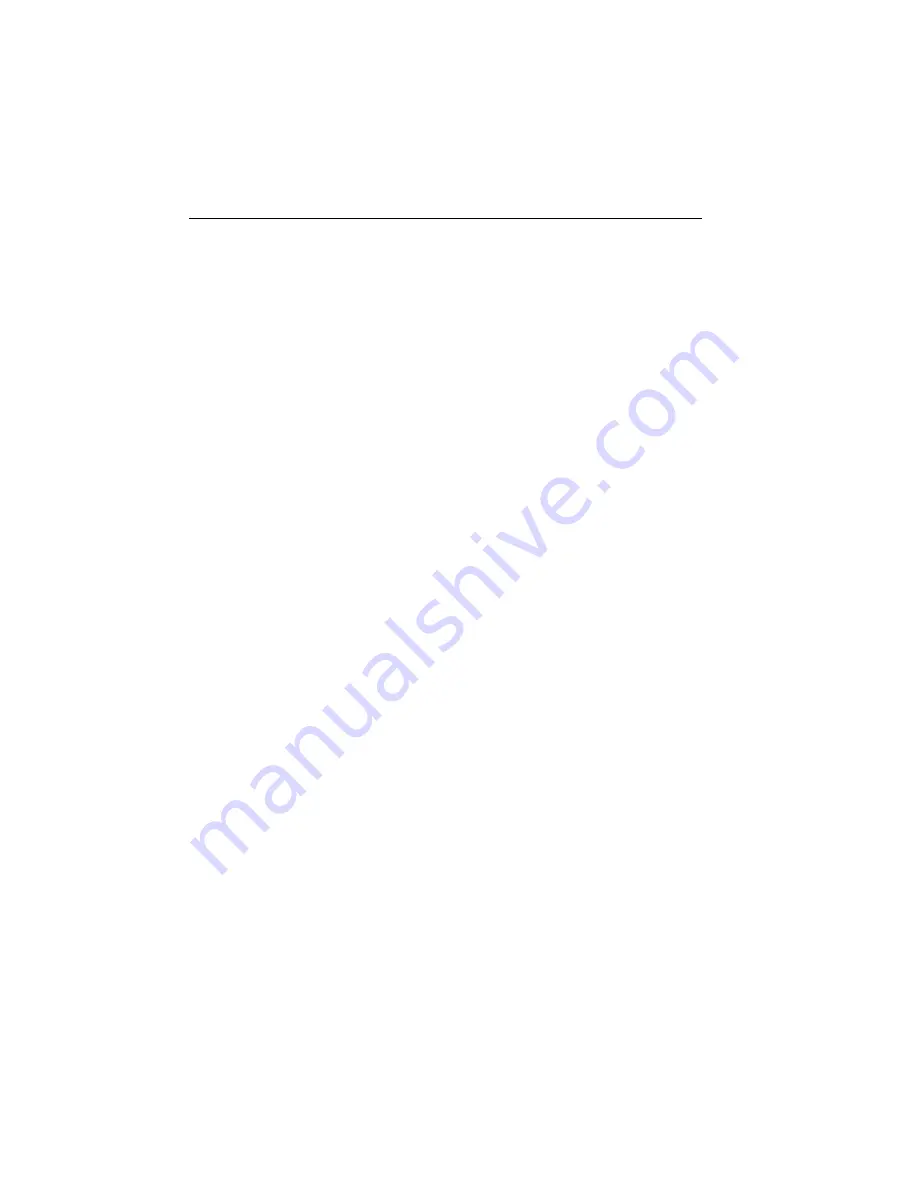
iv
Important safety information and precautions
Caution. Use forced-air ventilation when bench-testing the drive to ensure
proper cooling of drive components.
Use proper safety and repair techniques for safe, reliable operation of this unit.
Service should be done only by qualified persons. We recommend the proce-
dures in this manual as effective ways of servicing the unit. Some procedures
require the use of special tools. For proper maintenance and safety, you must
use these tools as recommended.
The procedures in this manual and labels on the unit contain warnings and
cautions that must be carefully read and followed to minimize or eliminate the
risk of personal injury. The warnings point out conditions or practices that may
endanger you or others. The cautions point out conditions or practices that may
damage the unit, possibly making it unsafe for use.
You must also understand that these warnings and cautions are not exhaustive.
We cannot possibly know, evaluate, and advise you of all the ways in which
maintenance might be performed or the possible risk of each technique.
Consequently, we have not completed any such broad evaluation. If you use a
non-approved procedure or tool, first ensure that the method you choose will not
risk either your safety or unit performance.
Always observe the following warnings and precautions:
• Perform all maintenance by following the procedures in this manual.
• Follow all cautions and warnings in the procedures.
• Use sound safety practices when operating or repairing the unit.
• Use caution when troubleshooting a unit that has voltages present. Turn off
power to the unit before servicing it.
• Wear safety shoes when removing or replacing heavy parts.
• Provide a means to isolate the drive from the main power in case of fire or other
emergency.
• Ensure that the internal temperature of the rack or cabinet does not exceed
the limits defined for the drive, when the drive is mounted in an equipment rack
or cabinet. When units are stacked vertically, pay special attention to the top
where temperatures are usually highest.
• Follow the precautions listed above in “Electrostatic discharge protection.”
• Do not remove any circuit boards from the drive chassis. Return the entire
drive for depot repair if any circuit board is defective. Removal of circuit boards
by personnel not performing depot repair will damage components and may
void the warranty.
Summary of Contents for Elite ST43400N
Page 1: ...Elite Disc Drive ST43400N ND User s Manual...
Page 47: ...42...
Page 48: ...Maintenance 43...