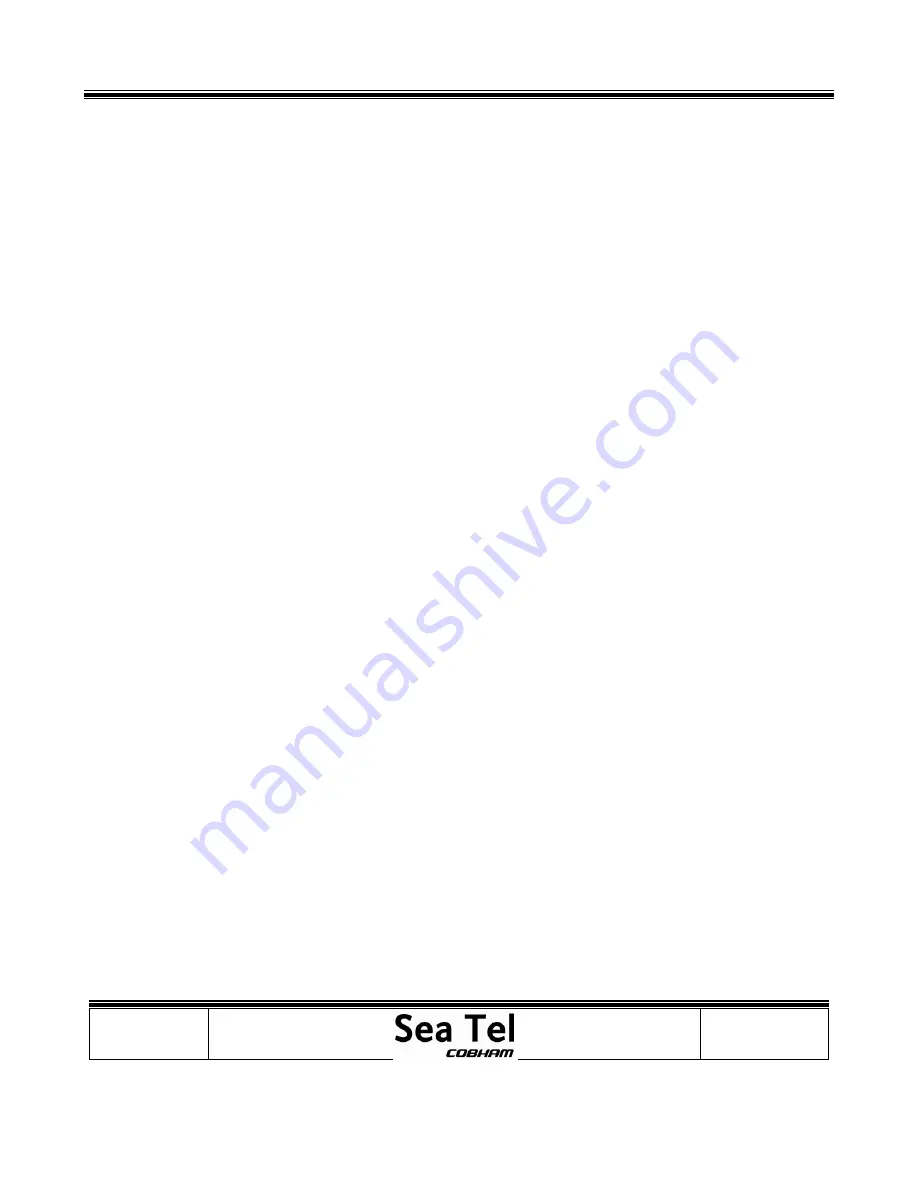
Field Service Procedure – Replacement PCU Kit, ST88, ST94 & ST144
Page
4
of
22
Document No
137738 Rev A
Copyright © Sea Tel, Inc 2012 - The information contained in this document is proprietary to Sea
Tel, Inc. This document may not be reproduced or distributed in any form without prior written
consent of Sea Tel, Inc.
7.2.
Error
Types.
The
3
types
of
pedestal
error
are.....
1.
Servo
Limit
(CL,
LV
and
AZ
)
–
A
servo
limit
error
means
the
PCU
motherboard
is
issuing
the
command
to
the
motor
driver
enclosure
to
drive
the
relevant
axis
harder
than
it
should
under
normal
operation
(the
servo
limit
has
been
reached).
This
could
be
whilst
the
antenna
is
trying
to
maintain
its
pointing
angle,
or
whilst
the
antenna
is
driving
the
axis
to
a
target
position.
2.
Stability
Limit
–
A
stability
limit
error
means
the
antenna
has
mispointed
from
its
desired
target
position
by
more
than
half
a
degree.
When
a
stability
limit
error
is
flagged
on
a
VSAT
antenna
the
DAC
will
send
the
TX
Mute
command
to
inhibit
the
transmit
function
of
the
satellite
modem
(It’s
common
to
see
the
servo
limit
and
stability
limit
errors
together).
3.
AZ
Reference
Error
–
An
azimuth
reference
error
means
there
is
a
corrupt
reading
in
the
antennas
relative
scale.
This
could
be
caused
by
the
system
completing
a
360
degree
rotation
without
the
sensor
coming
into
contact
with
the
home
flag,
the
sensor
coming
into
contact
with
the
home
flag
too
early,
or
a
physical
problem
such
as
the
chain
or
belt
slipping
on
the
motor
pulley
or
the
pulley
slipping
on
the
motor
shaft.
7.3.
Troubleshooting
Pedestal
Errors
–
Servo
Limit
and
Stability
Limit.
1.
Reinitialize
the
pedestal.
Does
it
drive
correctly
or
not
at
all?
‐
If
none
of
the
axis
drive
verify
the
N0
and
motor
gain
parameters
(N1
=
CL,
N2
=
EL
and
N3
=
AZ)
are
correctly
configured
in
the
PCU
through
the
Remote
Command
window
of
the
DAC.
2.
Verify
the
balance
of
the
antenna
and
check
for
physical
restrictions
on
the
pedestal.
If
the
axis
isn’t
correctly
balanced
the
PCU
will
be
outputting
additional
drive
commands
to
maintain
the
antennas
level
position.
3.
If
the
motor
isn’t
driving
correctly
or
no
motor
drive
is
present,
test
the
motor
for
faults
using
the
procedure
in
section
8
of
this
document.
If
you
find
the
motor
is
defective
replace
it
and
then
test
the
function
of
the
motor
driver.
If
the
axis
still
fails
to
drive
correctly
the
motor
may
have
damaged
it.
Replace
the
motor
driver.
4.
Verify
if
the
brakes
have
released
properly.
If
the
movement
of
the
axis
is
restricted
measure
the
output
to
the
motor
to
verify
if
the
12VDC
is
present.
If
so
the
brake
hasn’t
released
the
motor
is
defective.
If
the
12VDC
isn’t
present
trouble
shoot
the
harness
/
motor
driver
enclosure.
5.
Another
potential
problem
could
be
a
damaged
or
intermittent
harness
connection.
Remove
the
harness
back
shells
and
verify
all
the
pins
are
seated
correctly,
check
continuity
from
pin
to
pin
and
also
across
the
pins
to
verify
there
is
no
short
in
the
connections.
7.4.
Troubleshooting
Pedestal
Errors
–
Azimuth
Reference
Error.
1.
Reinitialize
the
system
and
verify
the
sensor
comes
into
contact
with
the
home
flag
as
the
system
drives
clockwise
in
azimuth
(the
LED
will
illuminate).
If
not
verify
if
the
home
flag/sensor
is
present,
if
correct
then
it’s
a
sensor/feedback
failure.
2.
Drive
the
azimuth
axis
in
90
degree
increments
and
verify
that
the
antenna
points
correctly
and
that
the
DAC
displays
the
correct
relative
position.
Also
verify
that
there
is
no
physical
restriction
on
the
azimuth
axis
such
as
the
chain
or
belt
slipping
on
the
motor
pulley
or
the
pulley
slipping
on
the
motor
shaft.
Summary of Contents for ST144
Page 1: ......