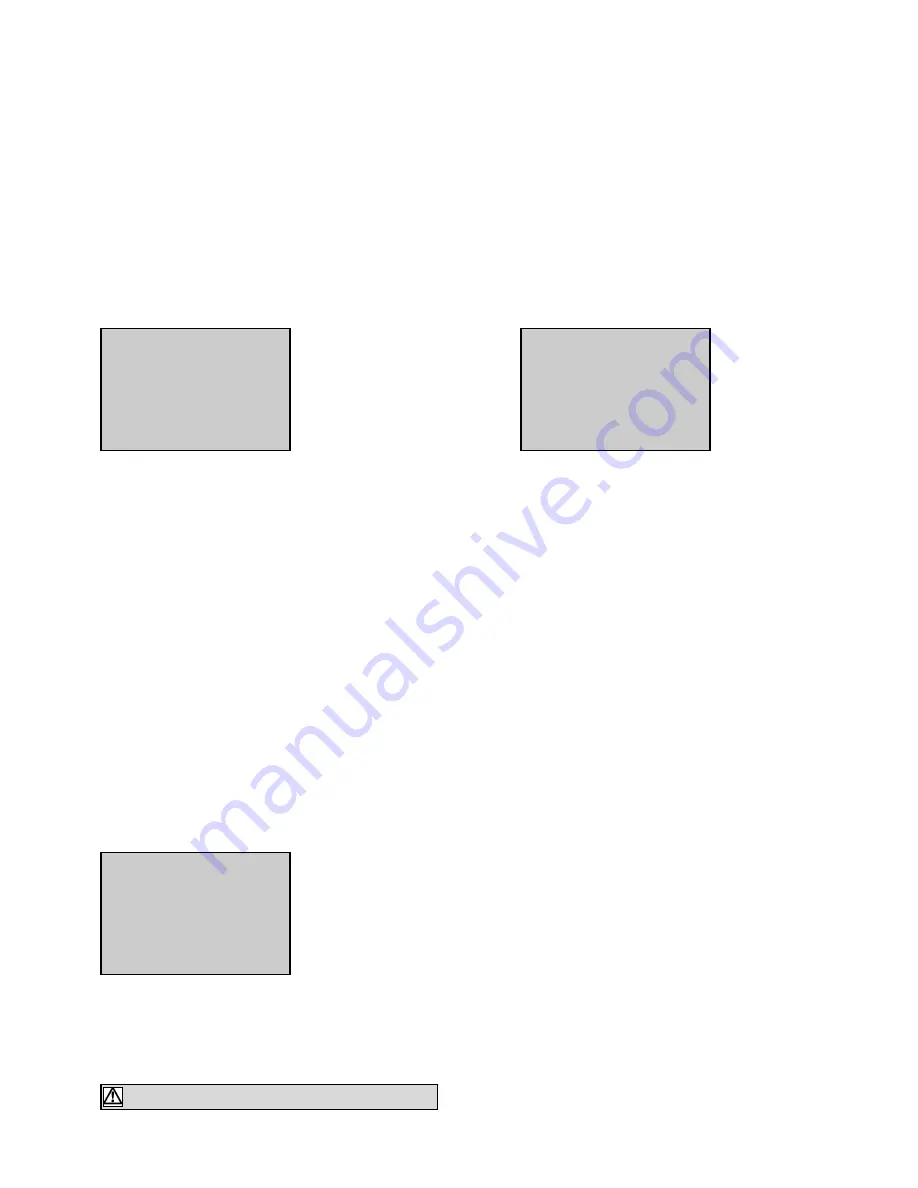
10/01
25
_________________________________________________________________________________________________________________________________Generating set operation
1177..44.. SSttaarrtteerr ccoonnttrrooll
On appearance of the external command (immediate or associated with the end of the power failure delay) or at the end of the engine
preglow period, the starter is cranked for an adjustable time (factory programmed). The following can happen:
The engine cranks sufficiently to start
The whole attempt is not sufficient to start the engine
In the first instance, the starter trips (see paragraph 17.5). In the second instance, the starter automatically trips at the end of the starting
attempt and for an adjustable time (factory programmed). At the end of the preset number of attempts, if the engine has not started, the over-
cranking fault appears on screen.
Several choices are possible at the start-up level (factory programmed) :
- One electrical starter (simple start)
- Two electrical starters (twin start)
- One electrical starter and one pneumatic starter (twin start)
- Consecutive start (1)
- Alternated start (2)
In case (1), activates x times starter 1 output, then activates y times starter 2 output (x is starter 1 number of attempts and y is starter 2 num-
ber of attempts).
In case (2), alternately activates the two starter outputs up to the biggest of the two values entered in memory (x or y).
x = starter 1 number of attempts
y = starter 2 number of attempts
Below, two screen examples showing the starters activation.
Fuel Lev(%)
E.Speed(RPM)
Batt.(Volts)
starting
attempt 1 starter 1
24
.
2
65
0
Fuel Lev(%)
E.Speed(RPM)
Batt. (Volts)
starting
attempt 3 starter 2
24
.
2
65
0
screen 1
screen 2
1177..55.. SSttaarrtteerr ttrriippppiinngg
If the engine starts, the starter control output is automatically tripped when the engine reaches the set threshold (factory programmed):
- For an electrical starter
- For a pneumatic starter
1177..66.. RRPPM
M aanndd VVoollttss ssttaabbiilliissaattiioonn
Stabilisation is a normal physical phenomenon in any regulation system. When the engine reaches the (electrical or pneumatic) starter trip-
ping threshold, the engine speed and alternator voltage stabilisation process is launched. When the delay elapses (factory programmed)
and if the low frequency and low alternator voltage thresholds are reached, the green LED comes on. This light tells the operator that the
Stand-by contactor or motorised C/B can be manually controlled. In the case of an Auto mode operation, the LED coming on activates
the Stand-by contactor delayed closure (see paragraph 18).
If the green LED does not come on, an alarm or fault will be signalled at the end of one of the four following delays: low frequency, high
frequency, low alternator voltage, high alternator voltage.
During operation, if the green LED goes out, this means that the generating set no longer operates within one of the two intervals:
- Low/high frequency
- Low/high alternator voltage
The appearance of an alarm or fault (depending on the configuration) will be displayed on screen.
1177..77.. G
Geenneerraattiinngg sseett oouuttppuutt
In Auto mode, when the Stand-by contactor is closed, the generating set delivers the installation.
In Manu mode and without ATS, as soon as the green LED comes on, the generating set can deliver the installation. The operator must
then manually close the output circuit breaker mounted on the generating set.
When the generating set delivers the installation, the screen below appears.
The message on the last line indicates that the genset delivers the installation. The output is easily
checked by viewing the currents in each phase.
Phase I1
current I2
(Amps) I3
ext command=1 17:10
gen running
12/01/00
436
425
420
1177..88.. EEnnggiinnee ccoooolliinngg ddoow
wnn aanndd sshhuuttddoow
wnn
Engine cooling down and shutdown are triggered in three different ways; in Manu mode, in Auto mode, in Test mode.
In Manu mode, the operator opens the Stand-by contactor by pressing the 0 button (if there is an ATS) or cuts off the load by manually
opening the generating output circuit-breaker. The operator must then let the engine run for a few minutes to let it cool down, before pres-
sing Stop.
The cooling down phase is required in Manu mode