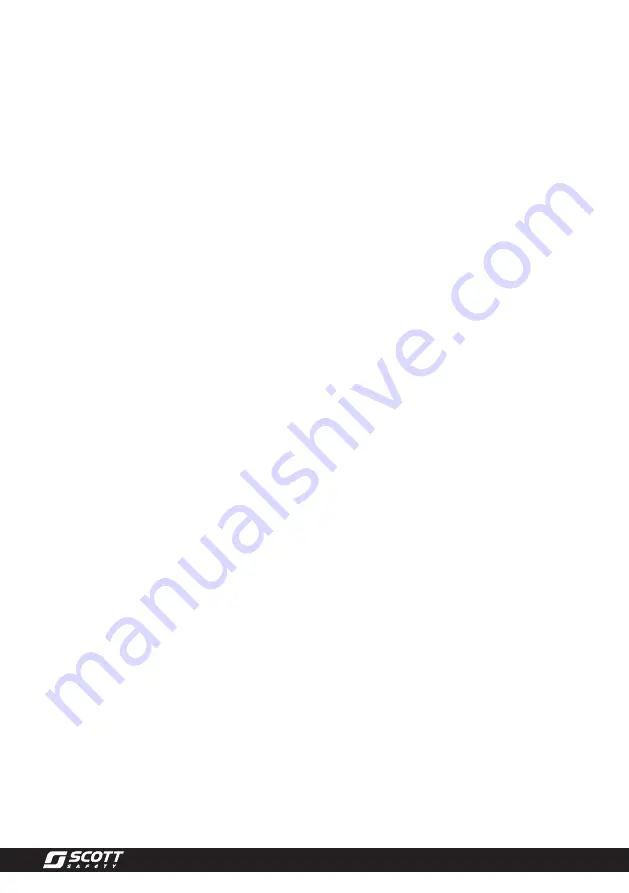
PROPAK i / f / fx
11
Facemask
Disconnect the DV (12) from the facemask.
Wash and disinfect the mask thoroughly in
a solution of
Distel
and warm water (see
following note).
Rinse the mask thoroughly in clean running
water. Pay particular attention to flushing out
the exhale valve.
Hang the mask by its neck-strap and allow
to dry thoroughly, away from direct heat or
sunlight.
When dry, wipe facemask seals with
Distel
disinfectant wipes.
Polish the visor inside and out with a clean, lint-
free cloth and slacken the head-harness, ready
for use.
Note:
Distel
liquid and
Distel
disinfecting wipes
are available from
Scott Safety
.
Demand Valve (DV)
CAUTION: DO NOT immerse the DV in liquids.
Fit the yellow cap on the DV outlet.
If required, use a small brush (eg toothbrush)
and a mild solution of soap and warm water to
clean around the locking catch (27) and bypass
knob (26).
Clean the valve body using a lint-free cloth
moistened in a mild solution of soap and warm
water. DO NOT store apparatus until completely
dry.
Operate the DV locking catch (27) and bypass
knob (26) several times and ensure that they
move freely. If either is not free-moving, attach
explanatory note and return for servicing.
Harness and Back-plate
Check that the harness webbing and fittings
are not worn or damaged; and that buckles and
fastenings are fully operational. Apparatus with
major defects must be returned for servicing,
with an explanatory label attached.
The harness and back-plate (1) can be sponged
clean with a mild solution of soap and warm
water or, following removal of the pneumatics
can be manually cleaned in a bath containing
cleaning or disinfecting solutions.
To remove the pneumatics:
Unfasten the shoulder press studs (4), and
release the rubber clips (17).
Remove the blank plate (15).
Turn the reducer (20) clockwise through 90
degrees and remove complete pneumatics
from the reducer mounting bracket (23).
CAUTION: Do not attempt to remove the
pneumatics with the hose still retained.
When the harness and back-plate (1) are
completely dry, re-fit the pneumatics.
To re-fit the pneumatics:
Feed hoses through the blank plate gap.
Locate the reducer (20) into the mounting
bracket (23) and turn through 90 degrees so
that the hoses face towards the top of the
back-plate (1).
Locate hoses in channels, ensuring that the
high-pressure gauge (14), whistle (13) and hose
(3) is on the left-hand shoulder strap and the
medium-pressure hose (11) and DV (12) is on
the right-hand shoulder strap.
Secure the hoses with the rubber clips (17), and
hose retaining flaps (4).
Slide blank plate in place (15).
CAUTION: Take care to not catch the hoses
on the edges when feeding through the gap.
Feed the DV hose (11), then pressure gauge
hose (3) through the blank plate gap.