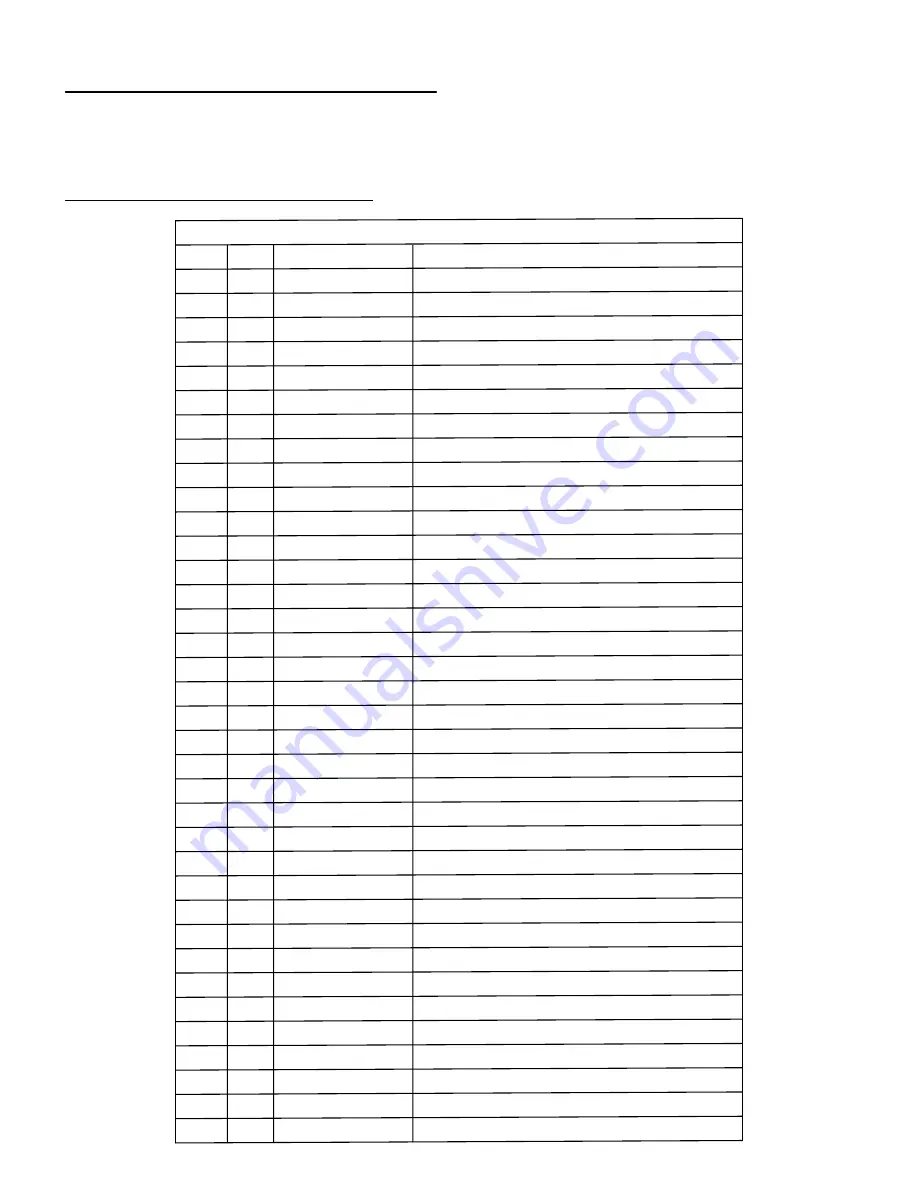
Page 54
Drag Link
402290
2
M-12 HHCS
205425
2
Pressure Block
412311
1
Punch Barrel (Includes H)
400615
1
Punch Barrel Guide
401464
1
Punch Barrel Guide (Ser.#1038 & Prior)
012325
1
M12 X 25MM HHCS S/N 2400PF0717 and up
201410
1
Stripper Clip
401479
1
Punch Jam Nut
000624
Die Holder (IncludesY & DD)
401470
1
Die Holder Spacer
001472
1
Punch Plate
400726
1
M-8 FSHCS
230107
2
M-10 HHCS
201220
1
M-12 x 55 HHCS
205422
2
1
Jam Nut Wrench
000628
Washer Reid
162005
2
M-10 x 12 SS
219047
1
Spring Clip
312361
1
Punch Beam (Includes B, F, G, H, I, & J)
012305
1
Stripper
401490
1
3/4 x 1 Spring
500040
1
M-6 x 12 SHCS
221005
1
M-5 RHMS
233315
2
M-5 Hex Nut
234008
2
Bushing
012304
1
M12 X 130 HHCS S/N 2400PF0717 and up
203450
4
M-12 Nut
208014
4
Stripper Plate
401492
1
M-6 x 12 FSHCS
230005
2
Grease Zerk
243101
DESCRIPTION
PART NUMBER
QTY
ITEM
B
C
E
D
A
Punch Pin S/N 2400PF0717 and up
012331
1
Punch Pin S/N 2376PF07/17 & Prior
012321
C1
1
D1
1
Grease Bolt S/N 2376PF07/17 & Prior
006018
F
G
H
I
J
M-12 Greer Nut
215014
2
K
L
N
O
P
P1
M-12 x 140 HHCS S/N 2376PF07/17 & Prior
203455
4
Q
Q1
R
1
R1
S
T
U
V
W
X
Y
Z
BB
AA
CC
DD
EE
3
M
E1
1
212014
M12 Lock Washer
9.0 MACHINE PARTS LISTS
The Following Sections Contain The Ironworker And Optional Tooling Parts Lists And Drawings.
For Your Own Convenience, Always Give Your Complete Serial Number When Ordering Parts.
9.1 PUNCH ASSEMBLY
Summary of Contents for Porta-Fab 45
Page 8: ...Page 7 FIGURE 1 ...
Page 16: ...Page 15 FIGURE 4 ...
Page 24: ...MADE IN THE USA BEST IN THE BUSINESS WARRANTY S C O T C H M A N ...
Page 55: ...MADE IN THE USA BEST IN THE BUSINESS WARRANTY S C O T C H M A N ...
Page 58: ...Page 53 FIGURE 22 080061 A B C D E Detail Cylinder ...
Page 64: ...Page 59 FIGURE 25 ...
Page 70: ...Page 65 FIGURE 28 ...
Page 72: ...Page 67 FIGURE 29 ...
Page 77: ...Page 72 10 2 ELECTRICAL BOX WIRING DIAGRAMS FIGURE 33 ...
Page 78: ...Page 73 FIGURE 34 ...
Page 79: ...Page 74 FIGURE 35 ...