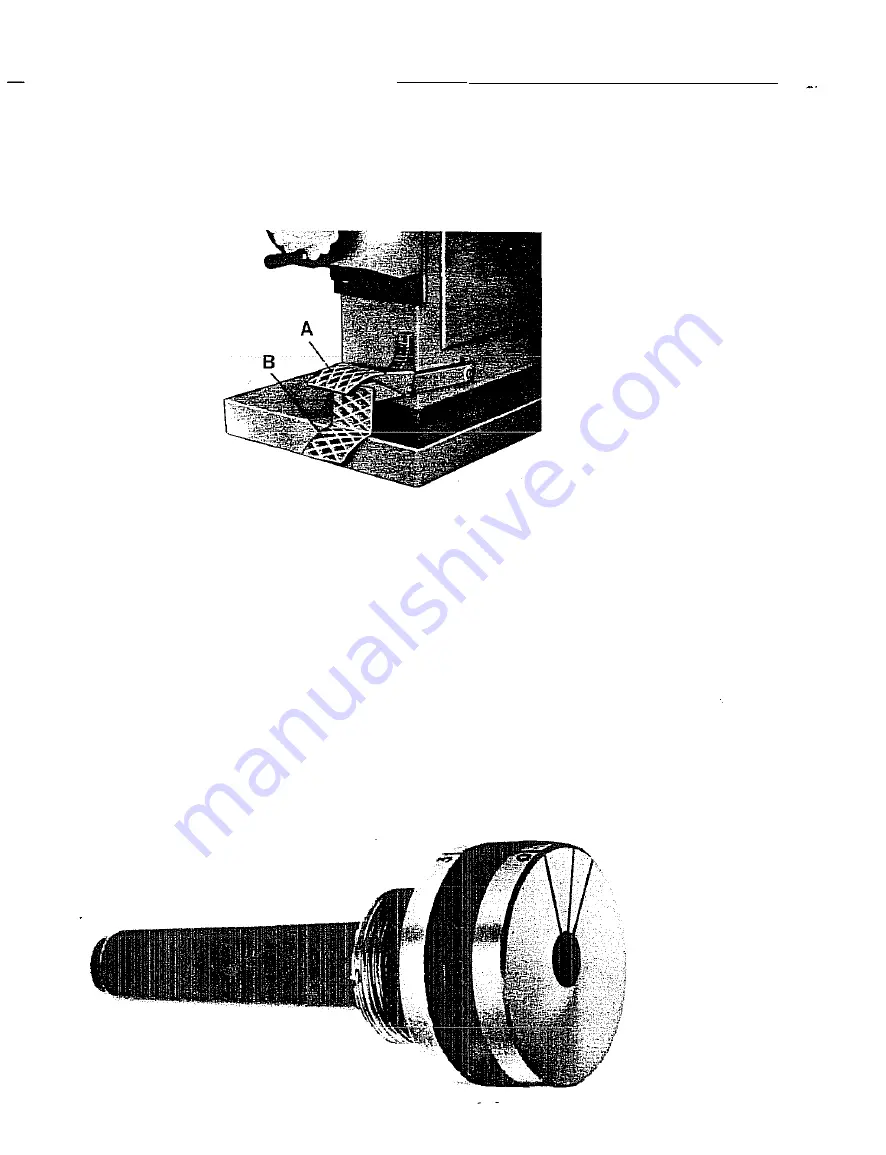
To release the pedal allowing the head to lift off again. it is necessary
to press the red upper pedal (A).
N.B. PEDALS ARE TO BE USED ONLY WHEN THE MACHINE IS RUNNING.
Fig. 9
j) BALANCING OF ECCENTRIC CHUCKS (fig. 10)
The balancing of the eccentric chuck is effected as follows:
a) Mount tile cutter and collet in the chuck with the cutting edge between
the two lines marked on the face of the same. The angle formed by
the cutting edge with the line marked " 0,, on the chuck. gives the
dimensions of the hole in compliance with the eccentricity of the chuck
and the diam of the cutter. To obtain the required milling diam. it is
necessary .to consult the table.
For instance: having a 8 mm diam. hole to execute; a chuck; n.
2
and
a
6.5
mm. diam. cutter. According to the table, the angle that the
cutter has to perform with the line marked with a
,,0.
is 47".
Fig. 10