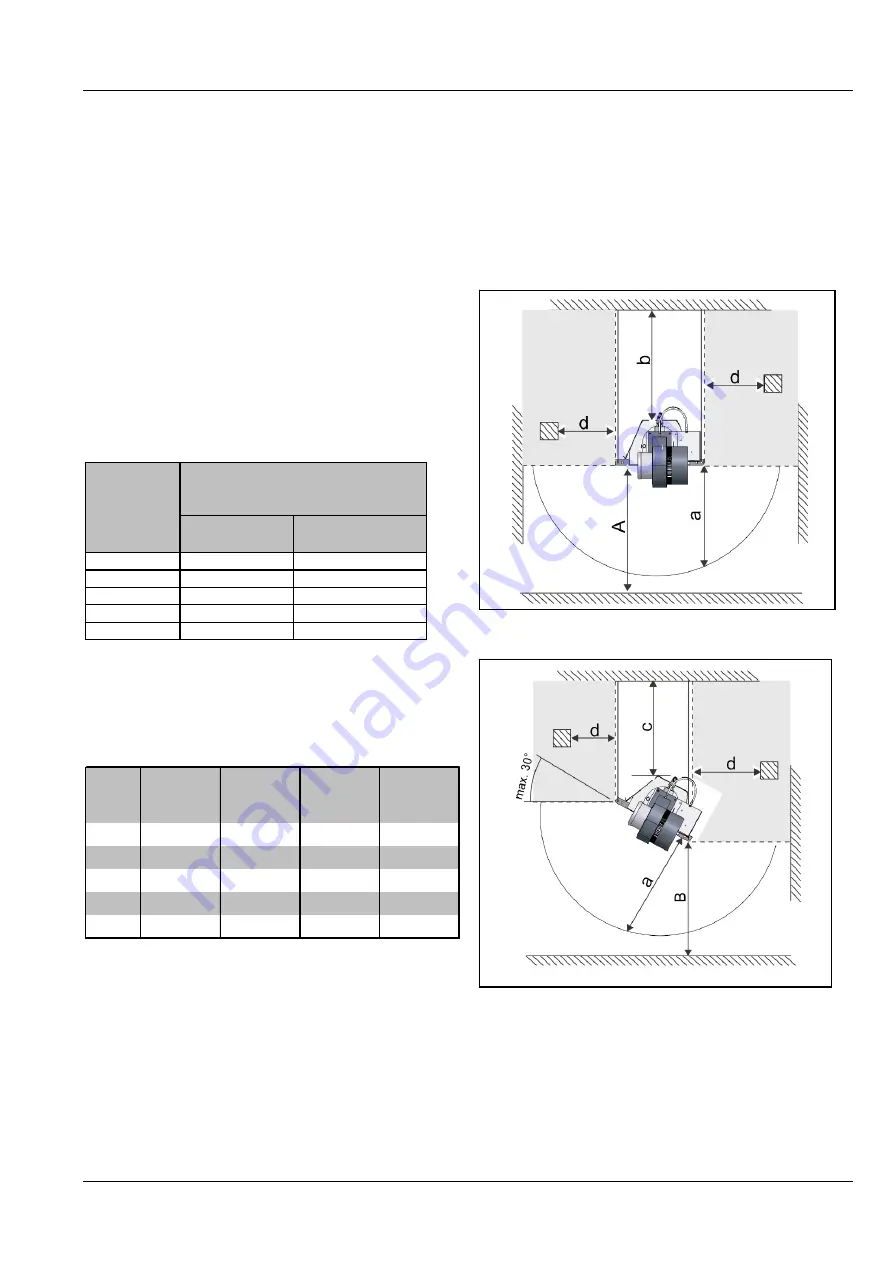
novoSchwank shape L
7
Version 008 nov
o
shape L 38/19
_I
N
T Te
chnical speci
ficati
o
n subjec
t t
o
change
4 Planning
Room temperature control
Radiant tube heating-systems must be equipped
with a temperature control.
Section heating is allowed without temperature
control.
Position of suspension
Suspension height
Radiant tubes must be positioned so that no one in
the radiation area is exposed to an extreme high
heat level. This is ensured when the minimum
suspension heights shown in the following table are
adhered to:
Tab 1: Minimum suspension heights
Key:
A = Minimum height when hanging horizontally
B = Minimum height when hanging angled
Type
a
[cm]
b
[cm]
c
[cm]
d
[cm]
20S L
110
20
15
15
25S L
110
20
15
15
35S L
130
20
15
15
45S L
170
25
25
25
55S L
230
35
35
35
Tab 2: Safe distances
Key:
a = Minimum radial safety distance [inside radiation area]
b = Minimum upper safety distance when hanging horizontally
c = Minimum upper safety distance when hanging angled
d = Minimum lateral distance to supply pipes outside radiation
area
Distances to flammable materials in the
radiant area
Radiant tubes must be positioned so that the
surface temperature of:
components with flammable materials,
flammable equipment, stored flammable
materials
never rises above 85° C.
Fig. 3: Suspension heights and distances for horizontal
application
Fig. 4: Suspension heights and distances for angled application
Direction of radiation
Radiant tubes novoSchwank can be positioned
horizontal or at an angle [max. 30° from vertical].
For this purpose suspension steel chains and cables
are installed at the suspension brackets.
Nominal
thermal load in
kW - gross
[net]
Suspension height in m
[max. radiation intensity 200 W/m
2
]
A = horizontal
B = angled
[30°]
16.7 [15]
3.5 m
3.1 m
21.1 [19]
4.0 m
3.6 m
32.2 [29]
4.8 m
4.3 m
43.3 [39]
5.5 m
4.9 m
54.4 [49]
6.8 m
6.2 m