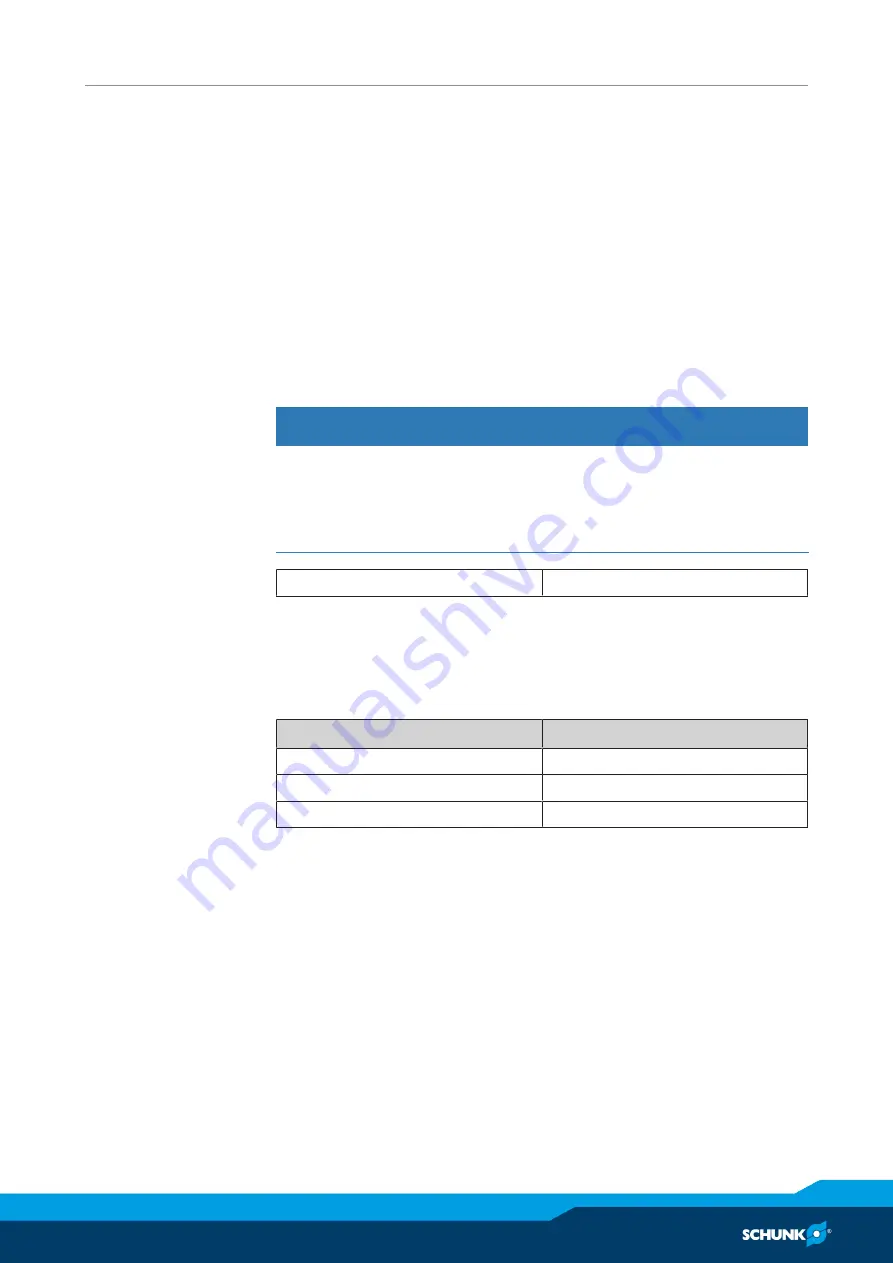
Maintenance
02.00 | PZH-SF 350 | Assembly and Operating Manual | en | 389485
29
6 Maintenance
6.1 Notes
Original spare parts
Use only original spare parts of SCHUNK when replacing spare and
wear parts.
Exchange of housing and base jaws
The base jaws and the guidance in the housing are matched. To
exchange these parts, send the product with a repair order to
SCHUNK or order the housing with the base jaws as a set.
6.2 Maintenance interval
NOTICE
Material damage due to hardening lubricants!
Lubricants harden more quickly at temperatures above 60°C,
leading to possible product damage.
•
Reduce the lubricant intervals accordingly.
Interval [Mio. cycles]
5
6.3 Lubricants/Lubrication points
SCHUNK recommends the lubricants listed.
During maintenance, treat all greased areas with lubricant. Thinly
apply lubricant with a lint-free cloth.
Lubricant point
Lubricant
Metallic sliding surfaces
microGLEIT GP 360
All seals
Renolit HLT 2
Bore hole at the piston
Renolit HLT 2