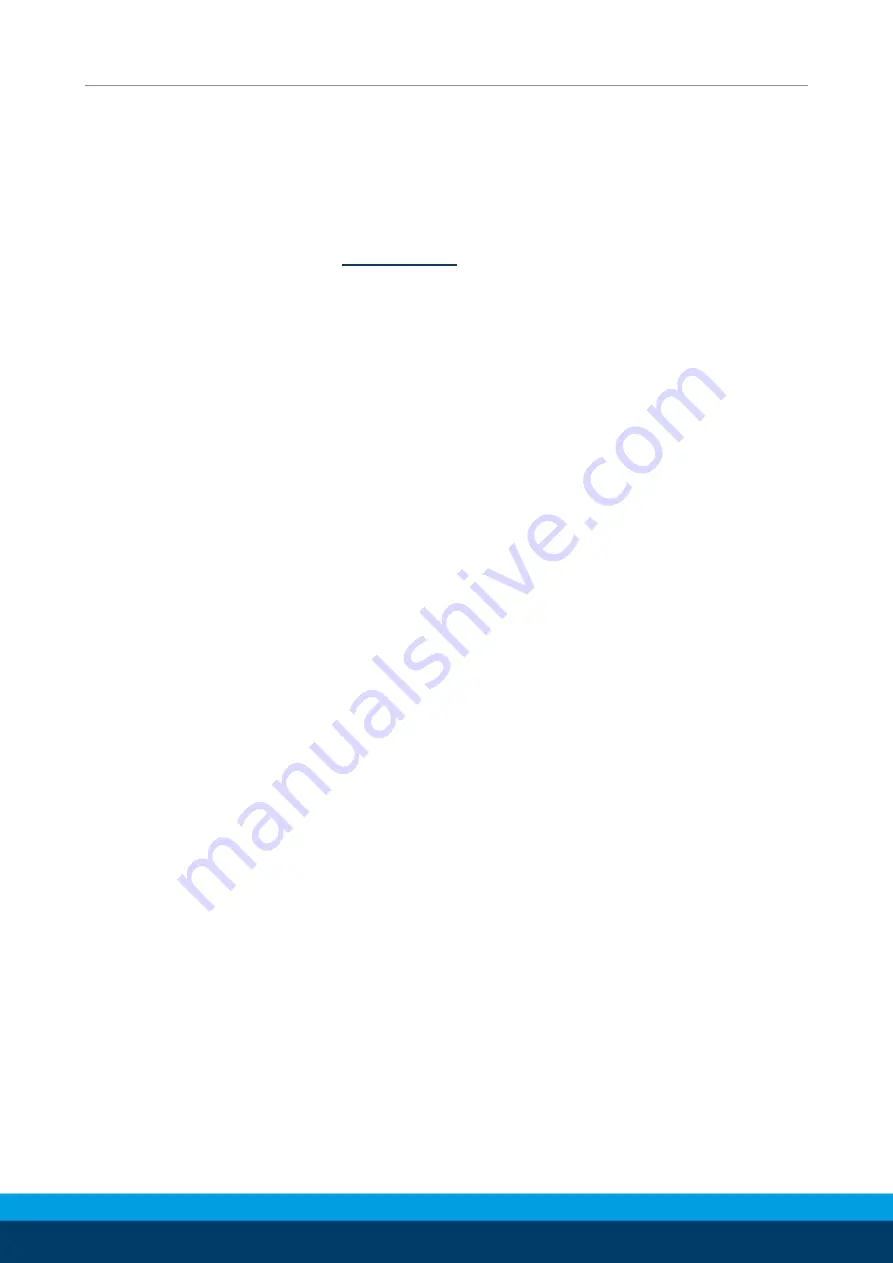
Basic safety notes
8
09.00 | MPG | Assembly and Operating Manual | en | 389213
2 Basic safety notes
2.1 Intended use
The product is designed exclusively for gripping and temporarily
holding workpieces or objects.
• The product may only be used within the scope of its technical
• When implementing and operating components in safety-
related parts of the control systems, the basic safety principles
in accordance with DIN EN ISO 13849-2 apply. The proven safety
principles in accordance with DIN EN ISO 13849-2 also apply to
categories 1, 2, 3 and 4.
• The product is intended for installation in a machine/system.
The applicable guidelines must be observed and complied with.
• The product is intended for industrial and industry-oriented use.
• Appropriate use of the product includes compliance with all
instructions in this manual.
2.2 Not intended use
It is not intended use if the product is used, for example, as a
pressing tool, stamping tool, lifting gear, guide for tools, cutting
tool, clamping device or a drilling tool.
• Any utilization that exceeds or differs from the appropriate use
is regarded as misuse.
2.3 Constructional changes
Implementation of structural changes
By conversions, changes, and reworking, e.g. additional threads,
holes, or safety devices can impair the functioning or safety of the
product or damage it.
• Structural changes should only be made with the written
approval of SCHUNK.