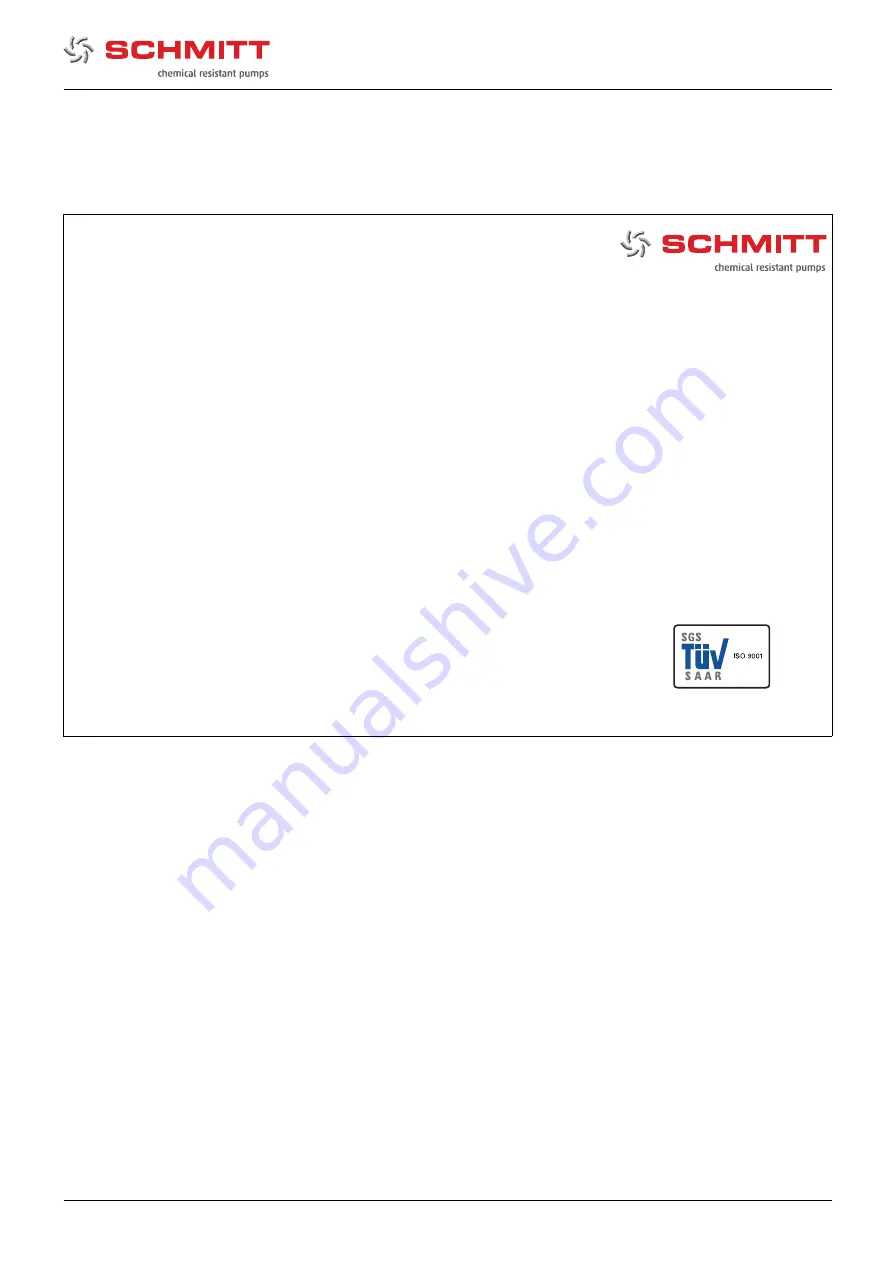
Appendix
9.4
Declaration of conformity in
accordance with EC machinery
directive
EU Declaration of Conformity
Manufacturer
SCHMITT-Kreiselpumpen GmbH & Co.KG
Einsteinstrasse 33
D-76275 Ettlingen
Type of pump
Centrifugal pump
Pump type
MPN 80, MPN 101, MPN 115, MPN 130, MPN 150, MPN 170 MPN 180H and MPN 190
We declare that the design of the listed pumps satisfies the provisions of the EU Directives.
The relevant points satisfy the requirements of the
EC Machinery Directive
2006 / 42 / EC
Low Voltage Directive
2014 / 35 / EU
Electromagnetic Compatibility
2014 / 30 / EU
Harmonized standards applied
EN ISO 12100:2010
EN 809:1998+A1:2009+AC:2010
D. Brandt
Einsteinstrasse 33a, 76275 Ettlingen
Managing Director / Documentation Officer
SCHMITT-Kreiselpumpen GmbH & Co.KG
This declaration was generated by EDP
and is valid without signature!
11333/0519
MPN
31