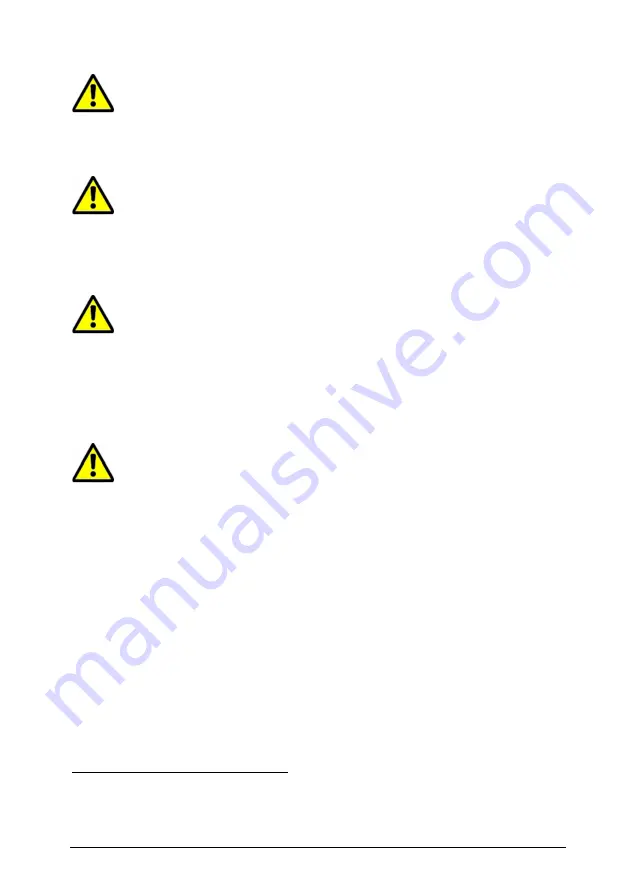
Instructions for Use
– SCHMIDT
®
Flow Sensor SS 20.700
Page 18
The analog signals have an own AGND reference potential.
Make sure that no supply voltage is active during electrical instal-
lation and that it cannot be switched on inadvertently.
The metal sensor enclosure is indirectly coupled to GND (with a varistor
15
,
parallel to 100 nF) and should be connected to a protective potential, e.g.
PE (depending on the shielding concept).
The appropriate protection class III (SELV) respective PELV
(according EN 50178) has to be considered.
Module connector
The module connector (M12, A-coded, female, 5-pin; see Figure 4-1) is
used to connect additional, optional expansion modules.
Only expansion modules from
SCHMIDT Technology
may be
connected to the module connector.
Operating voltage
The flow sensor
SS 20.700
is protected against reverse polarity of the
operating voltage. For its intended operation, it requires a DC voltage of
24 V
DC
with a tolerance of ±20 %.
Operate the sensor only within the specified voltage range of
24 V
DC
± 20 %.
Undervoltage may result in malfunction; overvoltage may lead to
irreversible damage.
Specifications of supply voltage apply to the connector of the sensor. Volt-
age drops generated due to line resistances must be taken into account
by the customer.
The operating current of the sensor (analog signal currents included, with-
out any of the pulse outputs) is normally approx. 80 mA. With pulse out-
put
16
, the required current value increases to max. 200 mA
17
.
Wiring of analog outputs
Both analog outputs for flow and temperature are designed as high-side
driver with “Auto-U/I” feature and are permanently short-circuit protected
against both rails of the operating voltage.
15
Voltage-dependent resistor (VDR); breakthrough voltage 30 V @ 1 mA
16
Without signal current of the semiconductor relay
17
Both signal outputs with 22 mA (maximum measurement values); supply voltage minimal