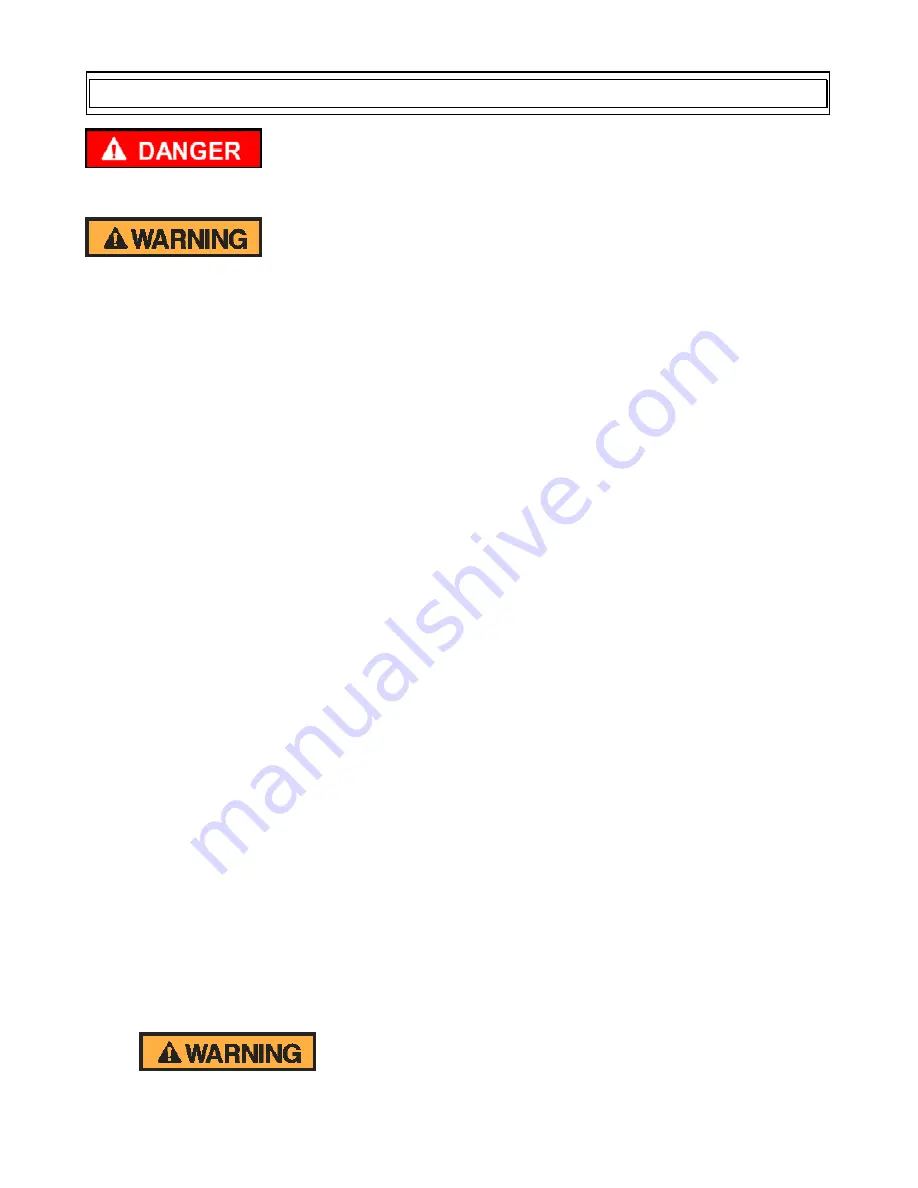
46
Copyright © 2021 Axxiom Manufacturing, Inc.
The MV3 Valve abrasive blaster is a Pressurized Vessel. Propelled objects will cause serious injury or
death. Depressurize vessel before performing any maintenance. See Section 6.2.
For proper operation, maintenance should be performed with the assistance of a qualified serviceman.
8.1.
Blaster Pressure Vessel:
The ASME Code is a standard covering materials, design, fabrication,
and installation. Vessel integrity after purchase is the responsibility of the owner and/or user. At
intervals required by state law and/or local authorities, the vessel should be subjected to a
hydrostatic test as described in the ASME Code, Section VIII, Division 1. Do Not subject the
abrasive blaster pressure vessel to a pneumatic proof test exceeding the maximum allowable
working pressure. In no case should the hydrostatic test pressure exceed 1.3 times the maximum
allowable working pressure (MAWP) shown on the pressure vessel nameplate (#24).
Thoroughly clean and dry the vessel before re-assembly. Moisture or debris left in vessel can
cause equipment malfunction.
8.2.
Blaster Pressure Vessel:
Any damage to an abrasive blaster can make it unsafe. Inspect the
exterior of the abrasive blast vessel weekly for corrosion, pitting, or other damage (i.e., dents,
gouges, or bulges). If damaged, take out of service immediately and have it inspected and/or
repaired by a qualified facility. Contact Axxiom Manufacturing, Inc. for technical support.
8.3.
Blaster Pressure Vessel:
The interior condition of the abrasive blast vessel (#1) should be
inspected quarterly. Pitting caused by corrosion will reduce the wall thickness of the vessel. If
excessive corrosion is found, have the abrasive blast vessel inspected by a qualified facility.
Contact Axxiom Manufacturing, Inc. for technical support. Refer to the ASME Data Report for
the vessel minimum thickness.
Check the pressure vessel internal piping for corrosion, cracks, wear, holes, or any other
damage. Repair or replace damaged components. See Figure 8.1 and Section 9.11.
8.4.
Popup Assembly:
The popup alignment and operation are tested by the manufacturer, however
vibration and creeping during shipment may cause the internal popup support piping to shift
resulting in misalignment. Check the popup gap and alignment prior to initial usage and weekly
thereafter. Inspect the popup as follows:
a)
Depressurize the abrasive blaster per Section 6.2.
b)
Disconnect air supply hose from the crowfoot (#2).
c)
Inspect the popup gasket (#6) and popup head (#5) sealing surfaces for wear or
deformations. Replace either if necessary.
d)
Check that the popup is centered within the gasket opening. If necessary, use a pry bar
as a lever between the popup and gasket to deflect the internal support piping and shift
the popup to the center of the gasket opening.
e)
Check the popup gap (distance between the popup surface and the gasket). It should be
between 5/8” and 7/8”. See Figure 8.1. An excessive gap is created by a vertical nipple
that is too short. An excessive gap will expose the top of the vertical nipple to abrasive
when the popup closes which could result in premature wear to the popup.
f)
After checking the alignment and gap, the blast vessel can be re-pressurized and the
popup is then checked for leaks. If a leak is present, repeat the above steps to isolate the
problem.
Pinch point hazard. Vessel pressurization will close the popup. Keep hands and fingers away
from popup. Disconnect air supply prior to performing popup maintenance.
8.0 Maintenance and Inspection Instructions
Summary of Contents for MV3
Page 18: ...18 Copyright 2021 Axxiom Manufacturing Inc 2 7 Abrasive Blaster Strapping Packing Detail ...
Page 36: ...36 Copyright 2021 Axxiom Manufacturing Inc THIS PAGE IS INTENTIONALLY BLANK ...
Page 58: ...58 Copyright 2021 Axxiom Manufacturing Inc 9 4 MICROVALVE ...
Page 59: ...59 Copyright 2021 Axxiom Manufacturing Inc 9 5 a MV2 Valve ...
Page 60: ...60 Copyright 2021 Axxiom Manufacturing Inc 9 5 b MV3 Valve ...
Page 61: ...61 Copyright 2021 Axxiom Manufacturing Inc 9 6 COMBOVALVE ...
Page 62: ...62 Copyright 2021 Axxiom Manufacturing Inc 9 7 Control Valves pneumatic and electric ...
Page 63: ...63 Copyright 2021 Axxiom Manufacturing Inc 9 8 a G2 Pneumatic Deadman ...
Page 64: ...64 Copyright 2021 Axxiom Manufacturing Inc 9 8 b Deadman Valves Pneumatic ...
Page 66: ...66 Copyright 2021 Axxiom Manufacturing Inc 9 10 Volumetric Blowdown Suppression System VBS II ...
Page 77: ...77 Copyright 2021 Axxiom Manufacturing Inc NOTES ...
Page 78: ...78 Copyright 2021 Axxiom Manufacturing Inc NOTES ...