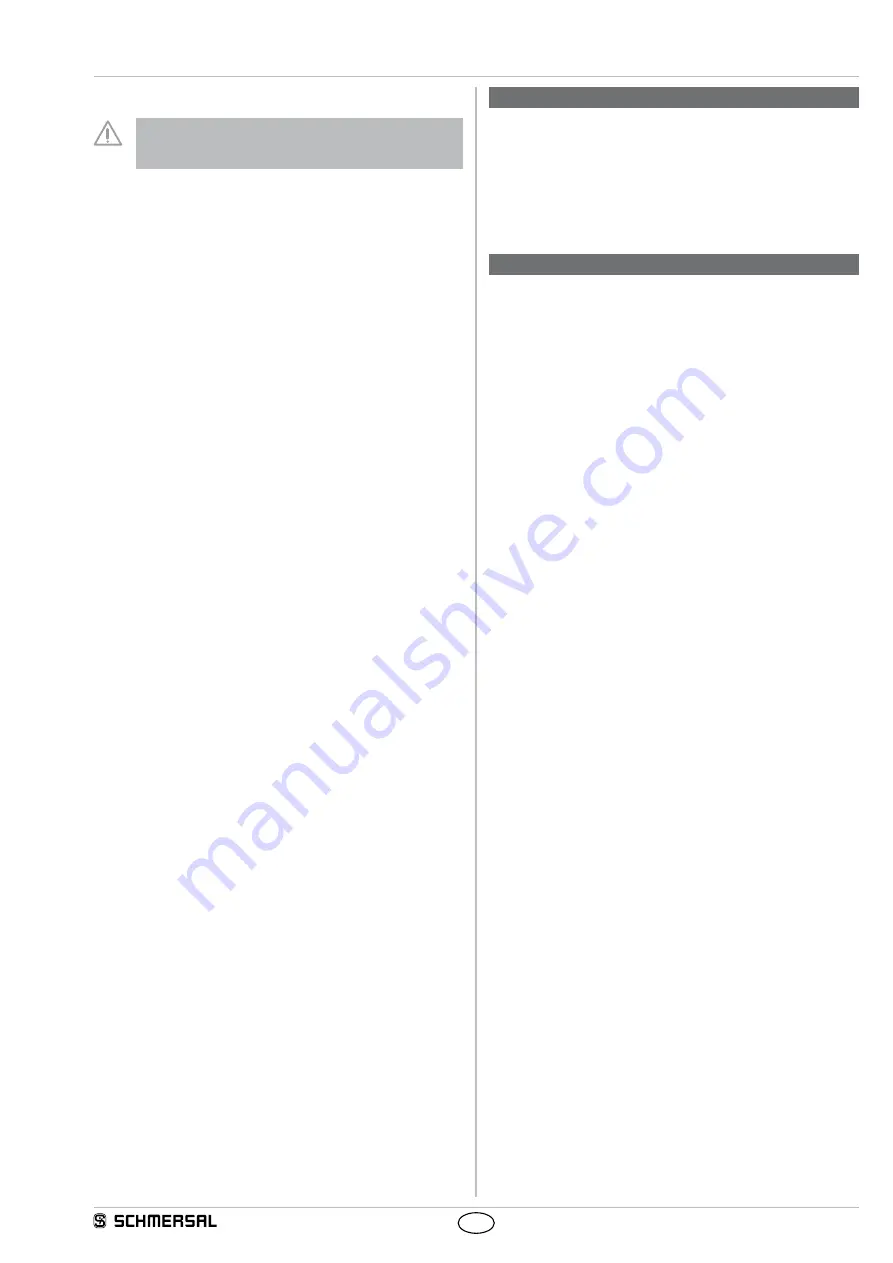
15
SLC440AS
SLG440AS
Operating instructions
Safety light curtain/safety light grid
EN
7.2 Maintenance
Do not use the SLG before the next inspection is
terminated An incorrect inspection can lead to serious
and mortal injuries
Conditions
For safety reasons, all inspection results must be archived The
operating principle of the SLC/SLG and the machine must be known
in order to be able conducting an inspection If the fitter, the planning
technician and the operator are different persons, please make sure
that the user has the necessary information at his disposal to be able
conducting the maintenance
7.3 Regular check
A regular visual inspection and functional test, including the following
steps, is recommended:
1 The component does not have any visible damages
2 The optics cover is not scratched or soiled
3 Hazardous machinery parts can only be accessed by passing
through the protection field of the SLC/SLG
4 The staff remains within the detection area, when works are
conducted on hazardous machinery parts
5 The safety distance of the application exceeds the mathematically
calculated one
Operate the machine and check whether the hazardous movement
stops under the hereafter-mentioned circumstances.
1 Hazardous machine parts do not move when the protection field is
interrupted
2 The hazardous machine movement is immediately stopped, when
the protection field is interrupted with the test rod immediately before
the transmitter, immediately before the receiver and in the middle
between the transmitter and the receiver
3 No hazardous machine movement when the test rod is within the
protection field
4 The hazardous machine movement comes to standstill, when the
voltage supply of the SLC/SLG is switched off
7.4 Half-yearly inspection
The following items must be checked every six months or when a
machine setting is changed
1 Machine stops or does not inhibit any safety function
2 No machine modification or connection change, which affects the
safety system, has taken place
3 The outputs of the SLC/SLG are correctly connected to the machine
4 The total response time of the machine does not exceed the
response time calculated during the first putting into operation
5 The cables, the connectors, the caps and the mounting angles are in
perfect condition
7.5 Cleaning
If the optics cover of the sensors is extremely soiled, the OSSD outputs
can be disabled Clean with a clean, soft cloth with low pressure
The use of agressive, abrasive or scratching cleaning agents, which
could attack the surface, is prohibited
8. Disassembly and disposal
8.1 Disassembly
The safety switchgear must be disassembled in a de-energised
condition only
8.2 Disposal
The safety switchgear must be disposed of in an appropriate manner in
accordance with the national prescriptions and legislations
9. Appendix
9.1 Contact
Consultancy / Sales
KA Schmersal GmbH & Co KG
Möddinghofe 30
D-42279 Wuppertal
Tel +49 (0) 202 64 74 -0
Fax +49 (0) 202 64 74- 100
You will also find detailed information regarding our product variety on
our website: wwwschmersalnet
Repair handling / shipping
Safety Control GmbH
Am Industriepark 11
D-84453 Mühldorf/ Inn
Tel +49 (0) 8631-18796-0
Fax +49 (0) 8631-18796-1