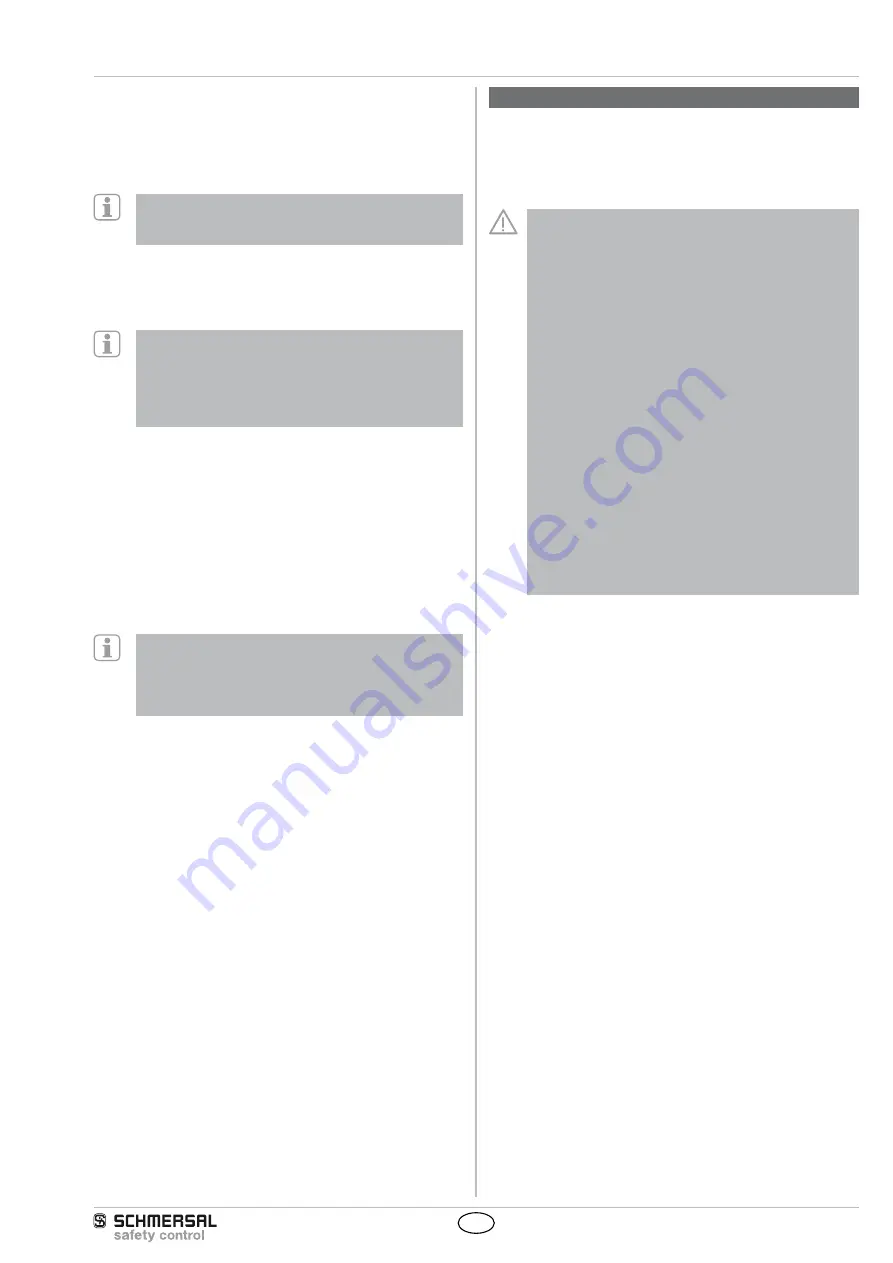
5
EN
SLC 220 IP 69 K
SLG 220 IP 69 K
Operating instructions
Safety light curtain / safety light grid
2.8.5 Start interlock
The start interlock prevents an automatic start of the machine when the
supply voltage is switched on. After enabling of the start interlock - by
the one-time interruption of the protection field -, this protective function
is deactivated until the next power reset.
The start interlock is not activated upon delivery. This function
is activated by means of the NSR-0700 BUS converter and a
PC or laptop.
2.8.6 Testing
The system performs a complete self-test within 2 seconds after the
operating voltage has been switched on. After this self-test, the system
switches to the ON state, if the protection field is clear.
The system will check all safety-technical functions in the
background within a cycle time of 2 seconds. Within this time,
a check of all functional components as well as a complete
memory test will take place. The main advantage for the user
is the omission of the system test (test before each machine
cycle).
In this operating mode, both outputs (OSSD1 and OSSD2) must be
integrated in the application, separated from each other (second switch-
off path - refer to wiring diagram 4.1).
External test
The system can trigger a test cycle by means of the external test input.
By applying a signal (+ +24 VDC) at the test output, a complete self-test
is executed within 150 ms. After 15 ms, the outputs change to OFF
state and are re-enabled after 150 ms if no fault is detected. The test
cycle must be triggered by the machine control. The signal change at
the outputs of the SLC/SLG 220 series must be monitored. In case of a
fault, the outputs will not be re-enabled until the fault is rectified.
If the test cycle of the application/machine cannot be comple-
ted within 150 ms, the restart interlock of the SLC/SLG 220
series must be activated (refer to wiring diagram 4.1). The
max. test time of 150 ms must be observed to the standard
EN 61496.
3. Mounting
3.1 General conditions
The following guidelines are provided as preventive warning notices
to ensure a safe and appropriate handling. These guidelines are an
essential part of the safety instructions and therefore must always be
observed and respected.
• The SLC/SLG must not be used on machines, which can be
stopped electrically in case of emergency.
• The safety distance between the SLC/SLG and a hazardous
machine movement must always be observed and respec-
ted.
• Additional mechanical safety guards must be installed so that
the operator has to pass by the protection field to reach the
hazardous machine parts.
• The SLC/SLG must be installed so that the personnel always
must be within the detection zone when operating the machi-
ne. An incorrect installation can lead to serious injuries.
• Never connect the outputs to +24VDC. If the outputs are
wired to +24VDC, they are in ON state, as a result of which
they are unable to stop a hazardous situation occuring on the
application/machine.
• The safety inspections must be conducted regularly.
• The SLC/SLG must not be exposed to inflammable or explo-
sive gasses.
• The connecting cables must be connected in accordance
with the installation instructions.
• The fixing screws of the end caps and the mounting angle
must be firmly tightened.
• When fitting the sensors, please observe that the cable
output is at the bottom in order not to affect the functionality
of the membrane.
3.2 Protection field and approach
The protection field of the SLC/SLG consists of the entire range located
between the protection field markings of transmitter and receiver. Addi-
tional protective devices must ensure that the operator has to pass by
the protection field to reach the hazardous machine parts.
The SLC/SLG must be installed so that the personnel is always located
within the detection zone of the safety device when operating the hazar-
dous machine parts to be secured.