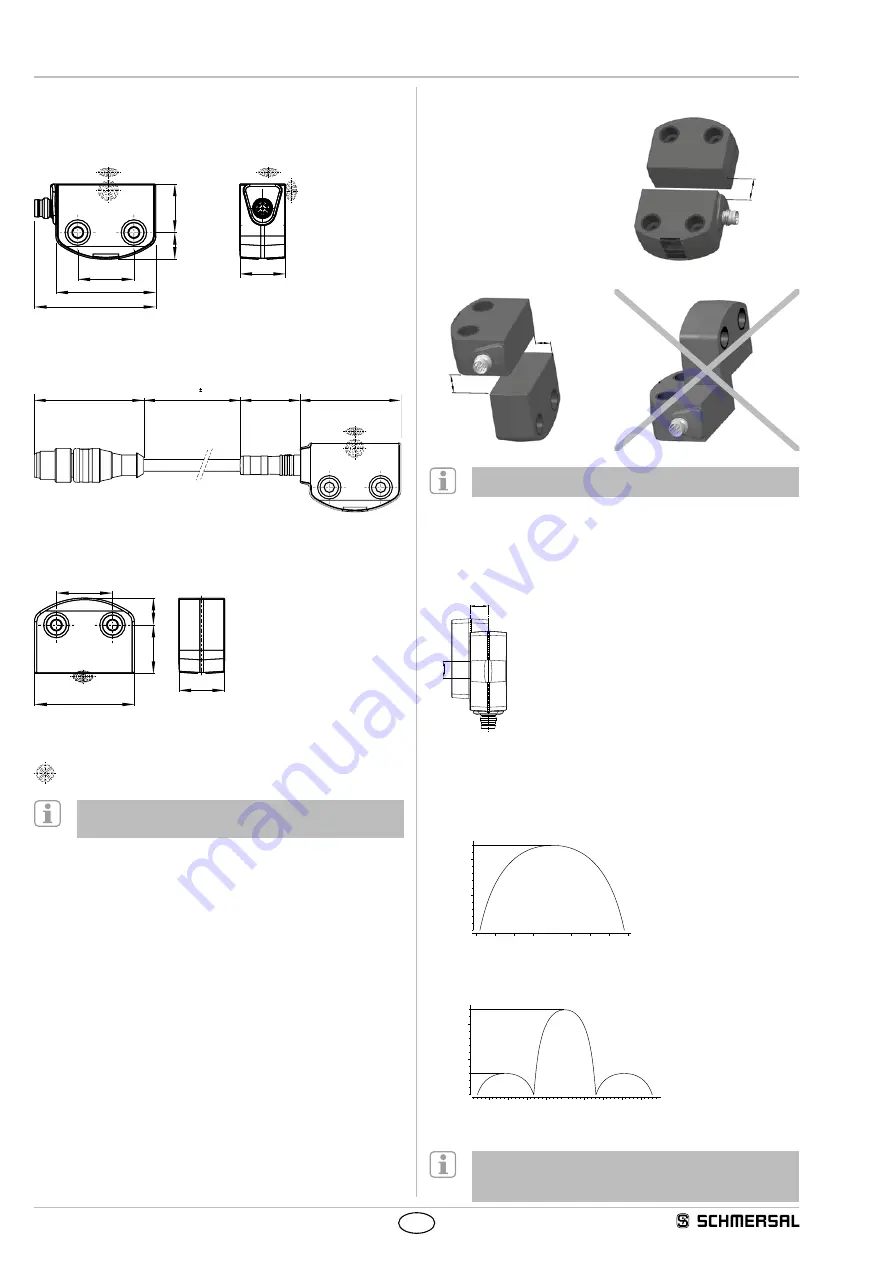
4
Operating instructions
Safety sensor
RSS260 AS
EN
3.3 Dimensions
All measurements in mm.
Safety sensor RSS260-…-ST-AS
19
10
.5
22
39.2
47.5
18
M4
Safety sensor RSS260-...-LSTM12-AS
43
25
47
250
10
Actuator RST260-1 / RST260-1-AD01 … 15
19
10.5
39
22
18
M4
Legend:
active area
Alternative suitable actuators with different design:
refer to www.schmersal.net.
3.4 Actuating directions
Actuation from front
12
Actuation from side
9
7
Lateral actuation only from the shown sensor side
3.5 Switching distance
The side allows for a maximum height misalignment (X) of sensor
and actuator of ± 8 mm (e.g. mounting tolerance or due to guard door
sagging). The axial misalignment (Y) is max. ± 18 mm.
Y
X
Actuating curves
The actuating curves represent the typical switching distance of
the safety sensor during the approach of the actuator subject to the
actuating direction
Transverse misalignment
-5
-20
5
10 15
-15
20
-10
0
Y [mm]
S [mm]
0
5
10
12
Height misalignment
-5
-20
-24
5
10 15
-15
20 24
-10
0
X [mm]
S [mm]
0
5
10
12
Preferred actuation directions: from front or from side
In case of a lateral actuation, the switching distances are
reduced by approx. 3 mm.