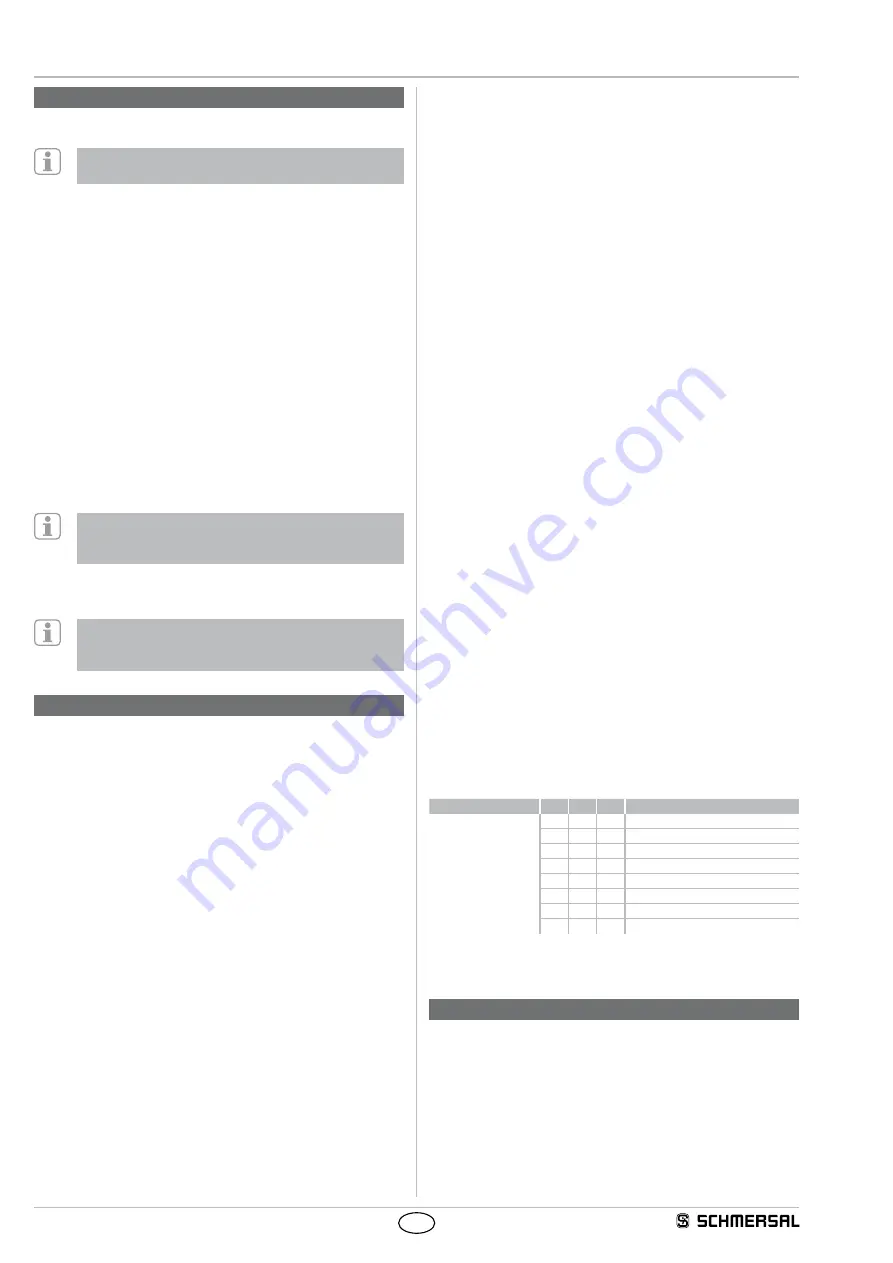
4
Operating instructions
Safety switch with interlocking function
MZM 120
EN
4. Electrical connection
4.1 General information for electrical connection
The electrical connection may only be carried out by
authorised personnel in a de-energised condition.
The voltage inputs A1, X1, X2 and IN must have a protection against
permanent overvoltage. Therefore, the use of PELV supply units ac-
cording to IEC 60204-1 is recommended.
The safety outputs can be integrated in the safety circuit of the control
system. For applications of PL e / control category 4 to EN ISO 13849-1,
the safety outputs of the safety switchgear or the chain of components
must be connected to a safety-monitoring module of the same category.
(see wiring examples)
Requirements for the connected safety-monitoring module:
• Dual-channel safety input, suitable for 2 p-type semi-conductor
outputs
•
Test function
The safety-monitoring module must tolerate internal functional tests of
the sensors with cyclic switch-off of the sensor outputs for max. 2 ms
(typically < 1 ms). The switch-off stage of the test cycle is temporarily
reduced by an active ohmic discharge of the cable. The safety-
monitoring module does not need to have a cross-wire short monitor-
ing function, if necessary, the cross-wire short monitoring function
must be disabled.
Information for the selection of suitable safety-monitoring
modules can be found in the Schmersal catalogues or in
the online catalogue on the Internet: www.schmersal.net.
If the safety component is wired to relays or to non-safety relevant
control components, a new risk analysis must be carried out.
When wiring SD devices, please observe the voltage
drop on the cables and the current carrying capacity of
the individual components.
5. Operating principles and latching force adjustment
5.1 Mode of operation of the safety outputs
MZM 120 B
Due to the permanent monitoring of the closed magnetic circuit, the
safety outputs Y1/Y2 are only enabled during the latching, when the
magnetic circuit is properly closed and the latching force F can also be
obtained when activated. If the metal surfaces are soiled or damaged,
the enabling signal is not transmitted.
The unlocking of the MZM 120 safety switch with interlocking function
does not lead to a switch-off.
MZM 120 BM
The safety outputs are enabled when the actuator is present on the
safety switch and the magnet control is activated. The unlocking of the
safety switch causes the safety outputs to be disabled within the dura-
tion of risk. As long as the actuator is inserted into the safety switch, the
unlocked safety switch with interlocking function can be relocked. In this
case, the safety outputs are re-enabled.
The latching force F is permanently measured and checked. In this way,
soiling of the solenoid interlock can be detected. If the latching force
drops below 300 N, the release signal for the safety outputs Y1 and Y2
is not given.
Description of the MZM 120 latching force adjustment
The latching force of the MZM 120 can be set in 8 steps each within
a range of approx. 30 N to approx. 80 N. To this end, the adjustment
target MZM 100 TARGET is used directly on the fitted MZM 120.
Adjustment of the latching force
1.) Open the safety guard and isolate the MZM 120 from the voltage
supply. Either switch off the voltage supply or pull out the connector.
2.) Put the adjustment target with the active side on the identification
plate of the MZM 120.
3.) Switch the voltage supply of the MZM 120 back on and wait at least
10 seconds before removing the adjustment target. The component
searches for the adjustment target. When the adjustment mode is
active, the safety outputs remain disabled.
4.) Remove the adjustment target again from the component.The yel-
low LED of the MZM 120 will repeatedly flash briefly to show the
currently set latching force level (e.g. 4 flashes = 4
th
latching force
level approx. 51 N).
5.) Put the adjustment target approx. 1 second back on the solenoid
interlock with the safety guard open to gradually increase the latch-
ing force by each time one step. The number of flashes will increase
accordingly.
The modified latching force can be checked directly on the safety
guard. If necessary, the latching force can be increased by another
step. When latching force level 8 is reached, level 1 will be activated
when the adjustment target is placed back on the component.
6.) Switch off the voltage supply of the MZM 120 once more to
permanently save the chosen latching force.
When the component is switched off, the adjustment mode is quit.
After the voltage supply is switched back on, the MZM 120 is ready for
operation.
Latching force indication
If the voltage supply of the MZM 120 is switched on when the safety
guard is open, the yellow LED will show the set latching force for
10 seconds by means of repeated brief flashes (e.g. 4 flashes =
4
th
latching force level approx. 50 N).
Description of the latching force adjustment for the MZM 120-...-
SD with serial diagnostic function
The latching force can be set through the latching force bits 1-3 of the
request bytes in 8 steps within a range of approx. 30 - 80 N.
Latching force bit
3
2
1
Latching force RE
0
0
0
30 N
0
0
1
37 N
0
1
0
44 N
0
1
1
51 N
1
0
0
58 N
1
0
1
65 N
1
1
0
72 N
1
1
1
80 N
6. Diagnostic functions
6.1 Diagnostic LED's
The safety switch signals the operational state as well as errors through
three coloured LED’s installed at the front side of the device.
green
Supply voltage on
red
Fault (s. Table: flash codes of the red diagnostic LED
yellow
Operating condition