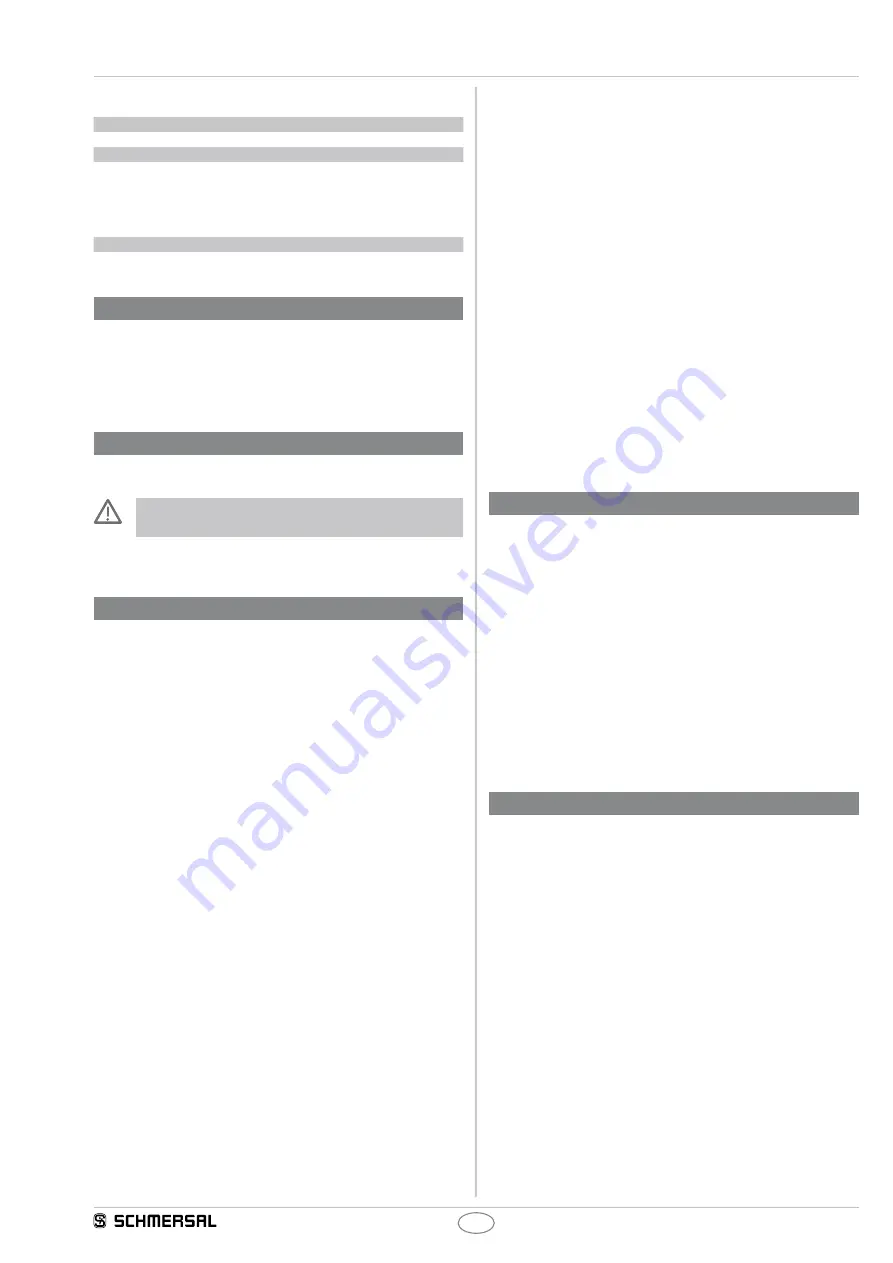
3
EN
FWS 1206
Operating instructions
Fail-safe standstill monitor
2.5
Safety classification
Standards:
EN ISO 13849-1; IEC 61508
PL:
up to d
Control category:
up to 3
PFH value:
1.0 x 10
-7
/ h; applicable for
applications with up to max.
50,000 switching cycles / year and
max. 80 % contact load. Diverging
applications upon request.
SIL:
up to 2
Service life:
20 years
3 Mounting
3.1 General mounting instructions
Mounting: snaps onto standard DIN rails to EN 60715.
3.2 Dimensions
Device dimensions (H/W/D): 100 x 22.5 x 121 mm
4 Electrical connection
4.1 General information for electrical connection
The electrical connection may only be carried out by
authorised personnel in a de-energised condition.
Wiring examples: see appendix
5 Operating principle and settings
Operating principle after the operating voltage is switched on
After the operating voltage is switched on, the initialisation is started.
After verification, the inputs of the fail-safe standstill monitor are
evaluated. The cyclic frequencies of the connected proximity switches
are compared to programmed limit frequencies.
To check the proximity switches, a second comparison between the
signal of the safety contact and the detected frequency is executed. If
the value drops below the programmed frequency and the contact of
the contactor indicates a standstill of the motor (contact closed), both
safety relays are actuated and the enabling paths are closed. If one of
the standstill conditions no longer is fulfilled (frequency or condition of
the contactor), the safety relays are disabled.
When the motor is started through the contactor, the function of the
proximity switches is tested. Five seconds after the contactor start-up,
the programmed limit frequency must be exceeded at the cyclic inputs.
If not, the fail-safe standstill monitor signals an error. Error messages
cause the safety relays to be disabled.
When two proximity switches are connected
If the programmed upper or lower limit frequency is exceeded, the fre-
quencies of both proximity switches are compared. A divergence of over
30% will be considered faulty and signalled. The yellow LED is flashing
(refer to ISD table).
Inputs X1-X4
X1: connection for proximity switch 1
X2: connection for proximity switch 2 or bridge to X1
X3: connection for reset button
The reset input has a double function
A rising flank (0/1) at X3 deletes all detected errors of the fail-safe
standstill monitor and causes the relays to be disabled. A static
High signal (closed contact) changes the function of output Y2.
Instead of a simple error message, the impulse sequence is
emitted for every detected error in accordance with the "Error
indication" table.
X4: connection for an additional standstill signal "high": standstill
Outputs
Enabling paths 13/14, 23/24
NO contacts for safety function
Additional outputs Y1/Y2
Y1: Authorized operation; the enabling path is closed
Y2: "error“ or impulse sequence to "Error indication" table
Note
The additional outputs Y1 and Y2 must not be integrated in the safety
circuit. If only one proximity switch is connected, the inputs X1 and X2
must be bridged.
6 Set-up and maintenance
6.1 Functional testing
The safety function of the safety-monitoring module must be tested.
The following conditions must be previously checked and met:
1. Proper fitting of the safety-monitoring module
2. Fitting and integrity of the power cable
6.2 Maintenance
In the case of correct installation and adequate use, the safety-monitor-
ing module features maintenance-free functionality.
A regular visual inspection and functional test, including the following
steps, is recommended:
• Check the correct fixing of the safety monitoring module
• Check the cable for damage.
Damaged or defective components must be replaced.
7 Disassembly and disposal
7.1 Disassembly
The safety monitoring module must be disassembled in the de-ener-
gised condition only.
7.2 Disposal
The safety monitoring module must be disposed of in an appropriate
manner in accordance with the national prescriptions and legislations.