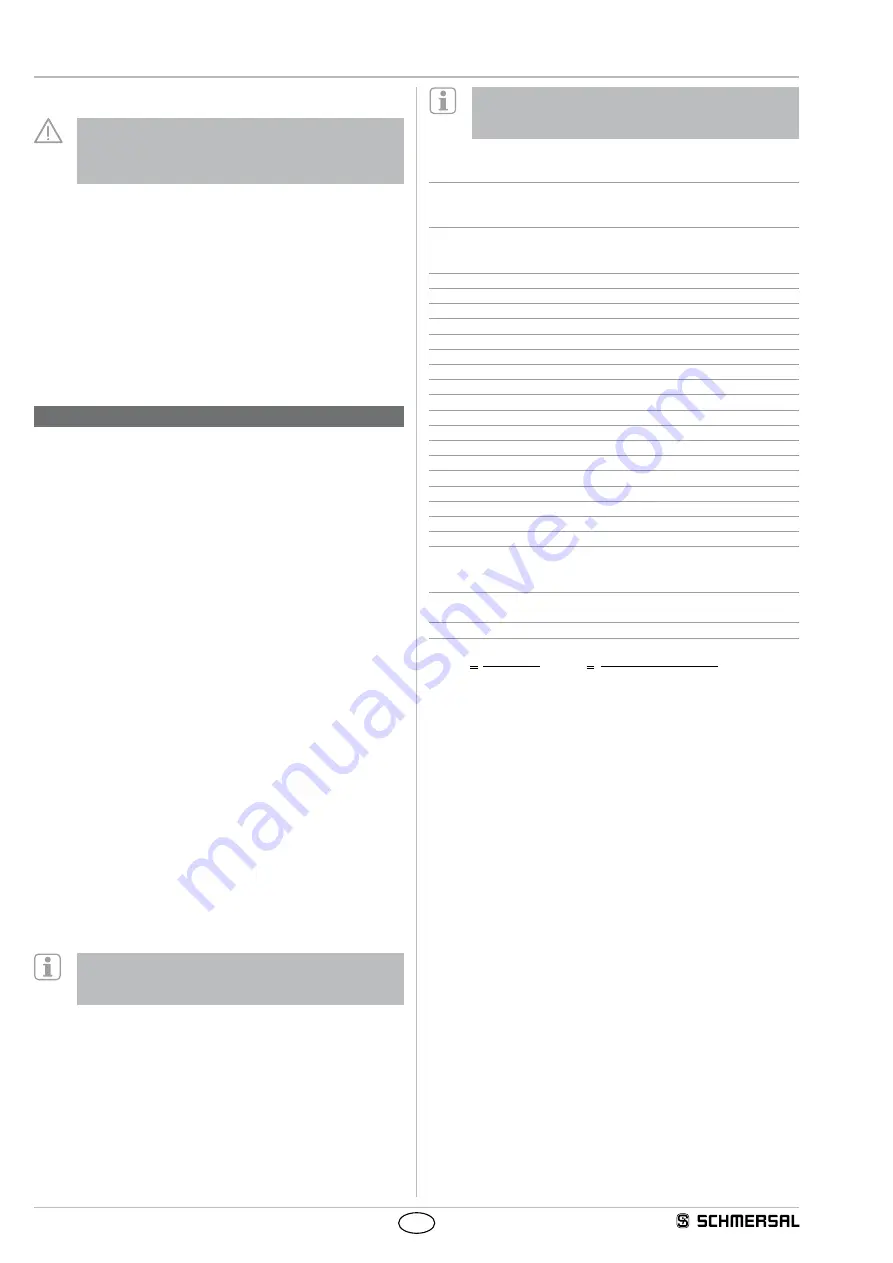
2
Operating instructions
Safety sensor
EX-BNS 250-2187
EN
1.6 Warning about misuse
In case of inadequate or improper use or manipulations of the
safety switchgear, personal hazards or damage to machin-
ery or plant components cannot be excluded. The relevant
requirements of the standard EN 1088 must be observed.
1.7 Exclusion of liability
We shall accept no liability for damages and malfunctions resulting from
defective mounting or failure to comply with this operating instructions
manual. The manufacturer shall accept no liability for damages result-
ing from the use of unauthorised spare parts or accessories.
For safety reasons, invasive work on the device as well as arbitrary re-
pairs, conversions and modifications to the device are strictly forbidden;
the manufacturer shall accept no liability for damages resulting from
such invasive work, arbitrary repairs, conversions and/or modifications
to the device.
2. Product description
2.1 Ordering code
This operating instructions manual applies to the following types:
EX-BNS 250-12Z-2187-3G/D
2.2 Special versions
For special versions, which are not listed in the order code below 2.1,
these specifications apply accordingly, provided that they correspond to
the standard version.
2.3 Destination and use
The safety sensor can be used for monitoring the position of movable
guards and flaps in explosion-endangered areas of Zone 2 and 22
category 3GD. The installation and maintenance requirements to the
standard series EN 60079 must be met. For the actuation of the safety
sensors, only the EX-BPS 250 actuator can be used.
The safety switches are used for applications, in which the hazardous
situation is terminated without delay when the safety guard is opened.
Only the entire system consisting of the safety sensor (EX-BNS 250),
the actuator (EX-BPS 250) and the safety-monitoring module (AES/
AZR or SRB) meets the requirements of the standard EN 60947-5-3.
Connecting multiple sensors to one AES/AZR safety-monitoring module
is technically possible. To connect multiple safety sensors (check if au-
thorised!), the NC contacts of channel 1 are wired in series and the NC
contacts of channel 2 are wired in series. The channels 1 and 2 must
be wired separatedly to the safety-monitoring module.
Recommended suitable safety-monitoring modules
The following safety monitoring modules of the AES, AZR and SRB
series are recommended for use with the safety sensor:
Information for the selection of suitable safety-monitoring
modules can be found in the Schmersal catalogues or in the
online catalogue on the Internet: www.schmersal.net.
Conditions for safe operation
Due to their specific impact energy, the components must be fitted with
a protection against mechanical stresses. The specific ambient temper-
ature range must be observed. The user must provide for a protection
against the permanent influence of UV rays. The energy restriction for
LED versions (24 V/10 mA) must be ensured by the user.
The user must evaluate and design the safety chain in ac-
cordance with the relevant standards and the required safety
level.
2.4 Technical data
Equipment category:
L
II 3GD
Ex protection:
- EX-BNS 250:
Ex nC IIC T6 Gc X; Ex t IIIC T80°C Dc X
- EX-BPS 250:
c 80°C
Standards:
IEC 60947-5-3, EN 60079-0, EN 60079-15,
EN 60079-31, EN 13463-1, EN 13463-5,
BG-GS-ET-14
Design:
rectangular
Enclosure:
glass-fibre reinforced thermoplastic
Max. impact energy:
1 J
Protection class:
IP67 to EN 60529
Connection:
Boflex cable
Cable section:
6 x 0.25 mm²
Operating principle:
magnetic
Actuating magnet:
EX-BPS-250, coded
s
ao
:
4 mm
s
ar
:
14 mm
Max. switching voltage:
24 VDC
Switching current: max.:
100 mA
Max. switching capacity:
1 W
Ambient temperature:
−25 °C ... +70 °C
Storage and transport temperature:
−25 °C ... +70 °C
Max. switching frequency:
5 Hz
Resistance to shock:
30 g / 11 ms
Resistance to vibration:
10 ... 55 Hz, amplitude 1 mm
2.5 Safety classification
Standards:
EN ISO 13849-1
B
10d
(NC/NO contact):
25.000.000
at 20 % contact load
Service life:
20 years
MTTF
B
d
x
x
h
s/h
3600
d
10d
op
op
op
n
0,1 x n
op
t
cycle
(Specifications can vary depending on the application-specific param-
eters h
op
, d
op
and t
cycle
as well as the load.)