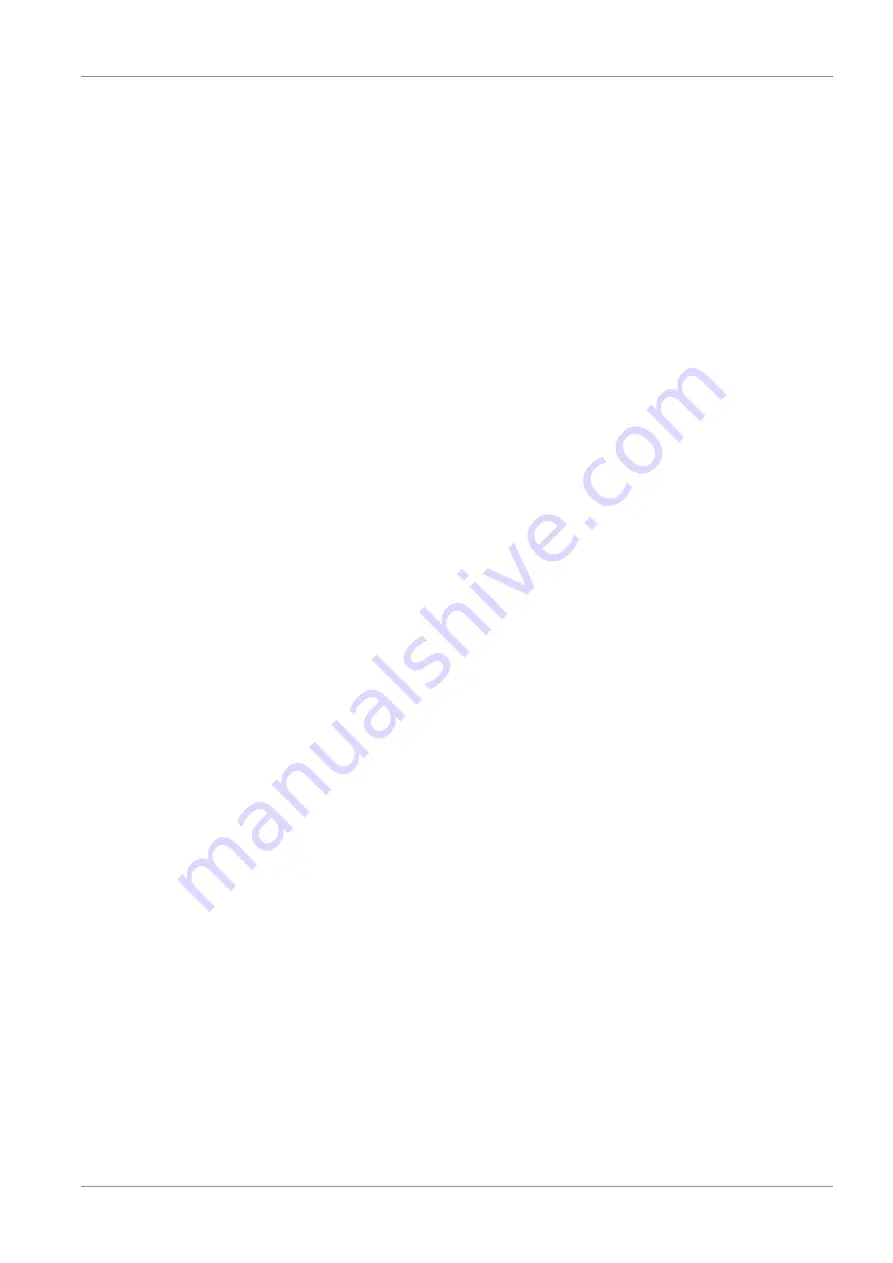
1 Important Information
EN-US · 30.30.00.00422 · 08 · 09/22
5 / 36
1 Important Information
1.1 Note on Using this Document
J. Schmalz GmbH is generally referred to as Schmalz in this document.
The document contains important notes and information about the different
operating phases of the product:
•
Transport, storage, start of operations and decommissioning
•
Safe operation, required maintenance, rectification of any faults
The document describes the product at the time of delivery by Schmalz and is aimed at:
•
Installers who are trained in handling the product and can operate and in-
stall it
•
Technically trained service personnel performing the maintenance work
•
Technically trained persons who work on electrical equipment
1.2 The technical documentation is part of the product
1. For problem-free and safe operation, follow the instructions in the documents.
2. Keep the technical documentation in close proximity to the product. The documentation must be ac-
cessible to personnel at all times.
3. Pass on the technical documentation to subsequent users.
ð
Failure to follow the instructions in these Operating instructions may result in injuries!
ð
Schmalz is not liable for damage or malfunctions that result from failure to heed these instructions.
If you still have questions after reading the technical documentation, contact Schmalz Service at:
www.schmalz.com/services