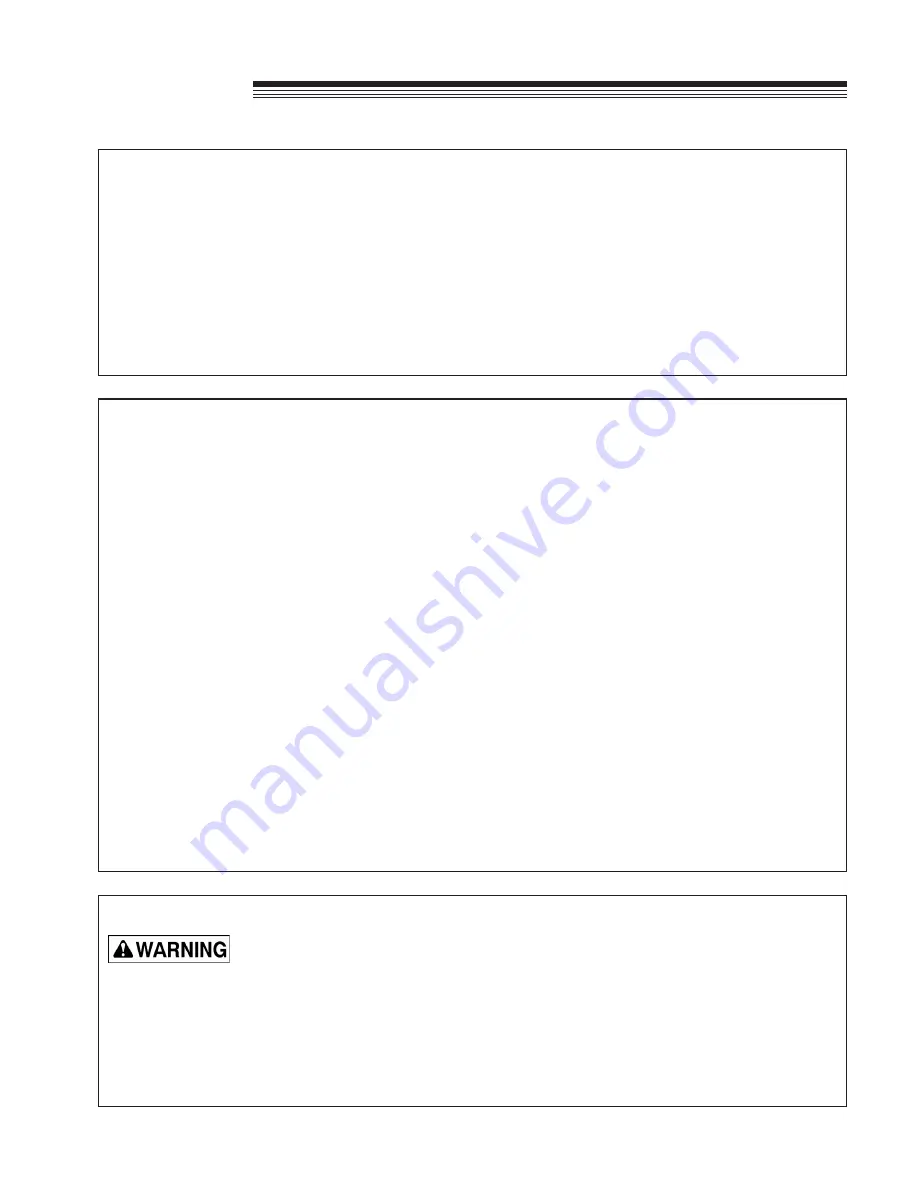
9
Classic
Pro
OPERATION
FUEL TANK
GASOLINE IS HIGHLY FLAMMABLE!
•
Fill fuel tank with good quality, clean, regular unleaded gasoline.
•
Do not use hi-test fuel.
•
Do not smoke.
•
Do not spill fuel.
•
Fill outdoors.
•
Do not overfill. Fill to 1" below bottom of filler neck to allow room for expansion.
•
USE A FUNNEL TO FILL GAS TANK.
BEFORE STARTING THE ENGINE
•
Disengage cutterdeck drive.
•
Lock traction locks in neutral/parking brake position.
•
Shift gearbox to neutral.
1. Check the oil level and add if necessary. Open the fuel valve under the middle of the fuel tank.
2. For cold starts, pull knob (I) to choke.
3. Pull the rope operated recoil starter firmly to start the engine. Allow the rope to recoil slowly before
releasing the handle.
4. As soon as the engine starts, gradually push in until the engine is warm enough to run with no choke at
all.
OPERATING THE MACHINE
•
Practice at slow engine and gearbox speeds with the blade control disengaged until completely familiar
with the controls.
•
For normal use the throttle should be kept fully open. By using the gearshift lever to speed up or slow
down the machine during use, maximum control and cutting efficiency can be maintained.
•
Using the machine at less than full throttle in heavy conditions will cause the engine to labor and result in
excessive wear.
•
For maneuvering where the gearbox does not give the required speed, partial throttle may be used.
•
Steering is controlled by the operation of the traction control levers. To steer the machine to the left, dis-
engage drive to the LH wheel by pulling up the LH traction control lever. To steer to the right, disengage
drive to the RH wheel by pulling up the RH traction control lever.
•
To shift into gear or change speeds, depress the operator present controls then raise the traction control
levers to the nuetral position to disengage the drive to both wheels and remove the load from the drive
system. Shift to the desired speed.
IMPORTANT:
The Peerless Model 700 transmission installed in this machine will provide good service. Like any manual
transmission the Peerless Model 700 must be declutched when it is shifted. Failure to declutch the wheel
drive with the traction control levers when shifting can cause failure of the shifting mechanism. Such abusive
failure is not covered under warranty by either Schiller Grounds Care, Inc. or Peerless.
•
Abusive failure of the shifting mechanism is easy to spot. Units will produce a ratcheting or clicking sound
when shifted into gear and the machine will not move. Upon disassembly of the gearbox, shifter keys will
show rounded corners, or units will become difficult to shift due to burrs on the shifter keys. Attempts to
force the machine to shift may bend the shifter fork assembly.