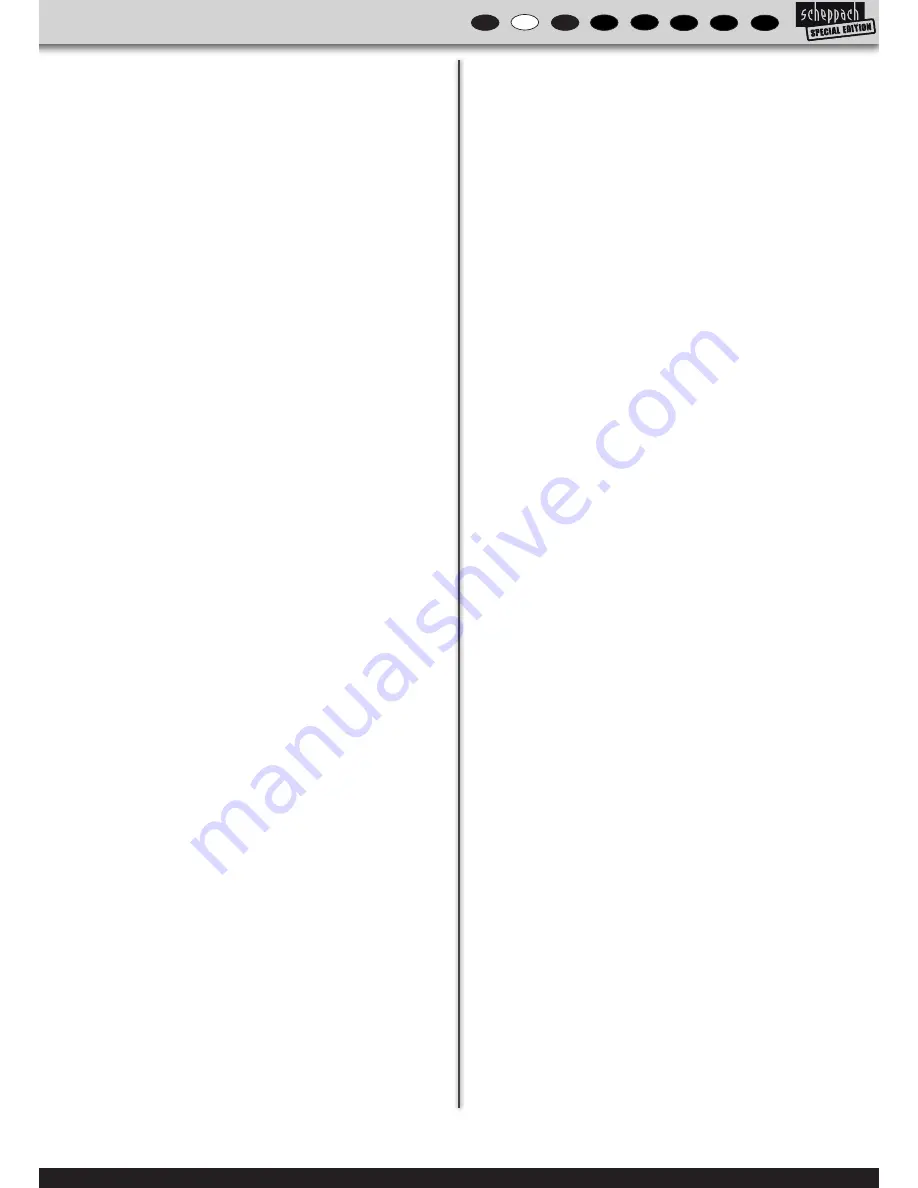
www.scheppach.com /
+(49)-08223-4002-99 /
+(49)-08223-4002-58
switch under the pressure switch cover. When the
maximum pressure set is reached, the pressure switch
is activated and the motor switched off. The pressure
is reduced as the air is consumed by the connected
tool, until the minimum pressure set is reached. Then
the pressure switch re-engages the motor. The opera-
tor at the compressor should take care that the motor
engages and disengages dictated by the influence of
the increasing and decreasing pressure in the tank.
The motor engages without any previous warning.
2
The maximum and minimum pressure have been set
in the works. These settings may not be altered.
3
All accessories were connected to the adjustable drain
valve (5).
4
As shown on the adjustable output pressure gauge
(3), the pressure of the adjustable exit can be altered
by turning the adjustable button (4).
Attention:
In order to read the correct output at the
output gauge, air must flow through the output. The
adjustable valve must be set and the pressure gauge
read with the valve open, while the air flows from the
output set through the accessory.
In order to increase the air pressure, turn the valve
clockwise. In order to reduce the air pressure, turn the
valve anti-clockwise.
Attention:
The absence of air flow during setting pro
-
duces an incorrect display. For a correct display, air
must flow.
5
Upon termination of your work, or when you leave the
compressor unattended, switch it off as follows:
•
Press the ON/OFF switch (2).
• Wait until the compressed air has escaped via the
drain valve (5) under the switch cover.
Attention:
On pressing the button you should hear a
short air exit (about half a second).
8.5 After operation Fig. 5
• Switch the machine off and pull the mains plug.
•
Pull the ring on the safety valve (6) in order to make
sure that the compressed air has escaped from the
tank, or open the drain plug of the tank in order to let
the pressure escape.
9. Electrical connection
The electrical motor installed is connected and
ready for operation. The connection complies with
the applicable VDE and DIN provisions.
The customer‘s mains connection as well as the
extension cable used must also comply with these
regulations.
Damaged electrical connection cable
The insulation on electrical connection cables is often
damaged.
This may have the following causes:
•
Passage points, where connection cables are
passed through windows or doors.
•
Kinks where the connection cable has been improp-
erly fastened or routed.
to the transport company which was used to deliver
the compressor.
•
Install the compressor near the point of consumpti-
on.
•
Avoid long air lines and supply lines (extension ca
-
bles).
•
Make sure that the intake air is dry and dustfree.
•
Do not install the compressor in a damp or wet
room.
•
The compressor may only be used in suitable rooms
(with good ventilation and an ambient temperature from
+5 °C to 40 °C). There must be no dust, acids, vapors,
explosive gases or inflammable gases in the room.
•
The compressor is designed to be used in dry
rooms. It is prohibited to use the compressor in are-
as where work is conducted with sprayed water.
8. Attachment and operation
n
Important!
You must fully assemble the appliance before us-
ing it for the fi rst time!
8.1 Wheels, Fig. 2
1
For fixing the wheels (12), first put one axle pin through
the wheel. Then place the spacer washer to the un-
derside of the wheel.
2
Fasten the wheel unit through the hole in the bracket
underneath the tank.
3
Fasten the flat washer, the split washer, and the nut.
Tighten the nut from the underside of the wheel and
attach the wheel cover.
4
Repeat the procedure for the second wheel.
8.2 Rubber feet, Fig. 3
Fix the rubber feet to the bracket on the front of the tank
using the screws, washers and nuts supplied.
Warning:
Make sure the place of setting up is clean, dry, and well
vented.
Warning:
As compressed air comes off the output, the
output may not be directed towards the operator or peo-
ple in the vicinity. The air coming off the exit may not be
inhaled. Daily check the pressure control valve.
8.3 Switching on and off the compressor
1
Check the model plate on the compressor: 230 – 240
V (or 110 – 120 V).
2
Plug the compressor cable into a standard socket (240
V or 120 V) and switch the compressor on.
3
For switching the compressor on, lift the ON/OFF
switch (3) on the pressure switch cover (2).
4
For switching the compressor off, depress the ON/
OFF switch.
8.4 Commissioning Fig. 4.1 + 4.2
1
The pressure in the tank is controlled by the pressure
19 / 76
GB
FR
IT
CK
DE
SK
PL
HU