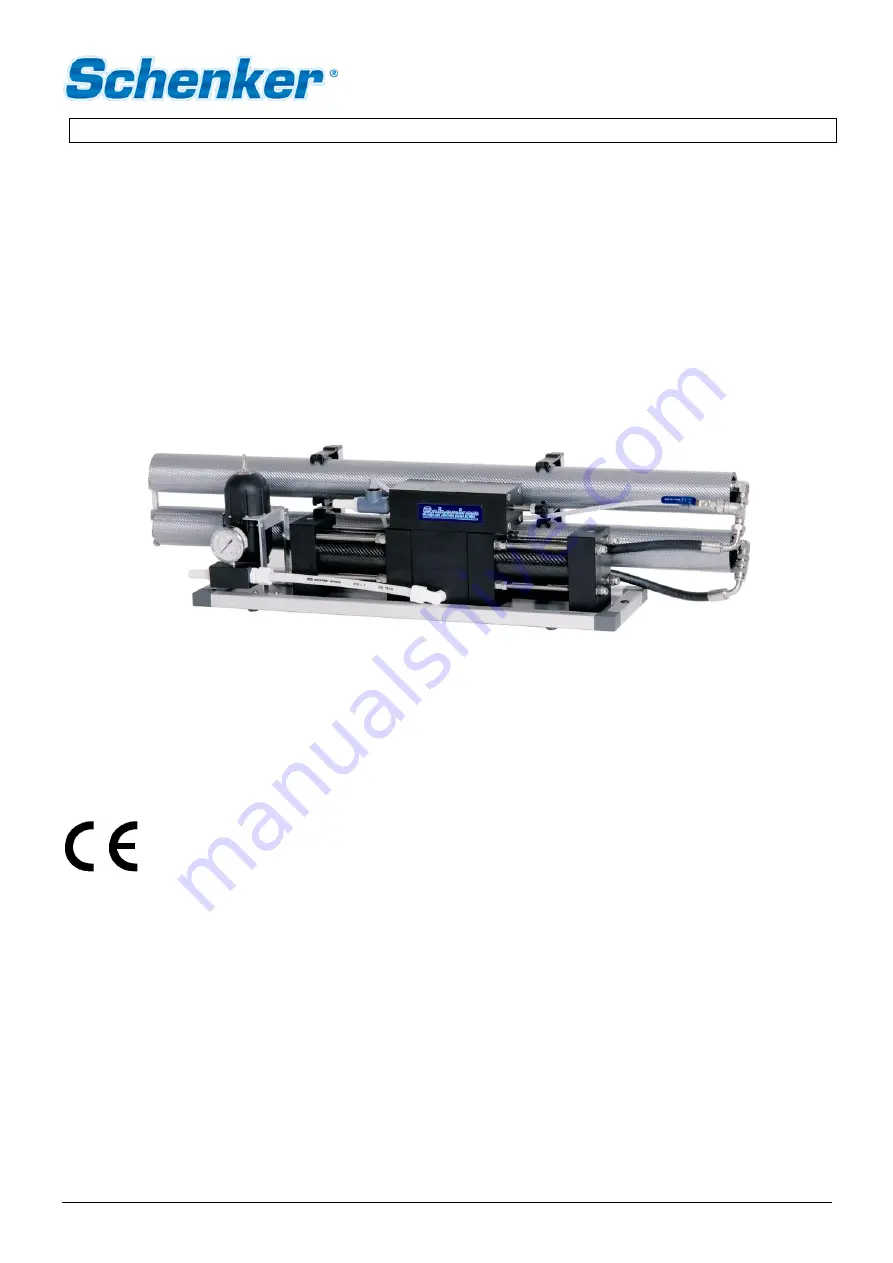
COD: 80S12/24.D.2018
Installation, use and maintenance manual
Model.: SMART 80
Matriculation number: 80S12/24D
Year of construction: 2006
Schenker Italia
Via Delle Repubbliche Marinare, 67
80147 Naples Italy
Tel. +39 081 5593505
Fax. +39 081 5597372
E-mail: [email protected]
WWW.schenkerwatermakers.com
THE PRESENT MANUAL BELONGS TO -
Schenker Italia
- ALL RIGHTS RESERVED
SMART 80
Digital 12/24 V dc