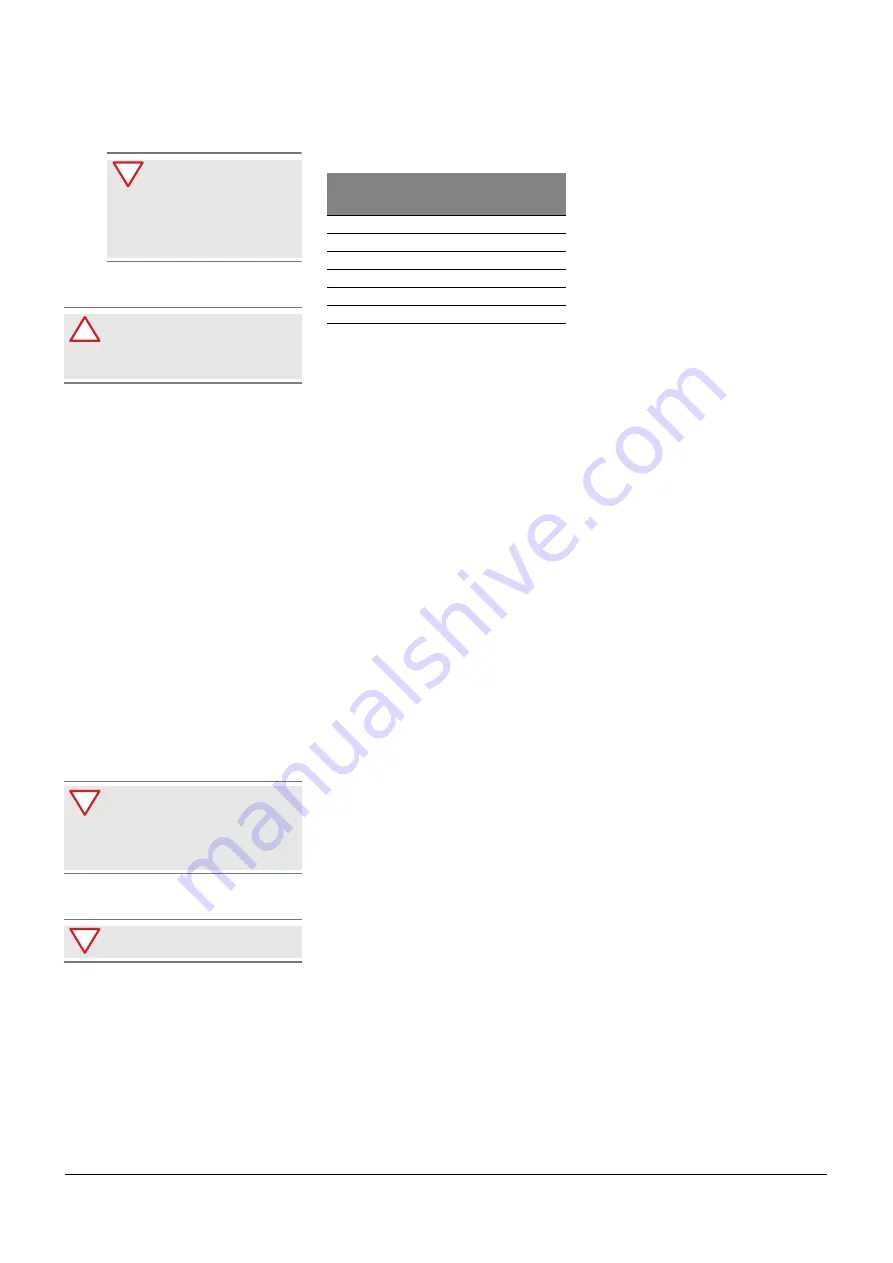
6
NovAx™
axial flow fan types ACN-ACW ATEX and ACW EX
amount and interval.
6.7 Dismount of motor
Switch off the power and
disconnect the motor cable in
the terminal box, before
beginning work on the rotor and motor.
The below procedure is with reference to
figure 10 on page 10.
Dismount of motor
1. Dismount any ducts on the inlet and
outlet sides.
2. Remove the centre screw (item 1) and
disc (item 2) that hold the hub cover
and rotor.
3. Remove the hub cover (item 3).
4. Dismount the rotor (item 4) by means
of a puller fastened in the two
threaded holes of the hub boss (item
5).
5. Disconnect the motor cable from the
motor.
6. Support the motor. See table 7 on
page 9 for max. motor weights.
7. Detach the motor from the motor shell
(item 8) by removal of the bolts (item
6) and washers (item 7).
8. Remove the motor (item 11) and
motor flange (item 10).
Do not expose fans and motor
parts to shocks that can result in
imbalance and deformations.
Motor bearings and fan components
are vulnerable parts.
6.8 Mount of motor
Replace lock washers and nuts
during assembly.
The below procedure is with reference to
figure 10 on page 10.
Mount of motor
1. Mount the motor (item 11) and make
sure the motor shaft is centred in the
fan casing.
2. Insert the bolts and washers (items 6
and 7). Tighten the bolts.
3. Mount the rotor (item 4) on the motor
with a tool fastened in the threaded
hole of the motor shaft. The rotor hub
must rest against the motor shaft
collar.
4. Use a feeler gauge to check that the
clearance between the rotor blade tips
and fan casing is the same throughout
the circumference and meets the
below requirements.
• Minimum 2 mm
• 10% of the motor shaft diameter
• Maximum 13 mm
Refer to the motor manufacturer’s
documentation for the shaft diameter.
5. Adjust the motor position with
reference to step 4.
6. Mount the hub cover (item 3), centre
disc (item 2) and centre screw (item 1).
7. Connect the motor cable (item 13) to
the motor (item 11) and the external
power cable in the terminal box (item
12).
8. Reconnect any ducts.
Follow the procedure in section “5. Start
of operation” to start the fan.
6.9 Blade angle adjustment
The rotor blade angles are set in the
factory to deliver the required
performance.
If the fan performance needs to be
changed, it is possible to change the
angles. This requires knowledge of the
motor load and of the max. permissible
blade angle with relation to the motor
rating. If the blade angles are changed,
the rotor has to be re-balanced.
Consult Novenco, before changing the
blade angles. A blade angle tool for angle
adjustment along with instructions for
use is available from Novenco.
7. Troubleshooting
Check for the below faults in case of
breakdowns or lack in performance. Call
for service, if problems persist.
Lack in performance
• Inlets blocked
• Outlets blocked
• Dampers blocked
• Supply air reduced
• Motors defective
• Motors disconnected
• Wrong fan rotation direction
Noises and vibrations
• Motor bearings defective
• Rotors out of balance
• Rotors damaged or worn
• Bolts or components loose
• Wrong pitch angles of rotor blades
Fans that operate in the stall area are
more likely to suffer breakdowns.
8. Inspection and test
It is recommended to test and inspect the
fans at regular intervals with regard to
operability and operation conditions.
Inspect the fans twice a year to ensure
satisfactory function and long life.
Extent of inspection
• Measure power consumption
• Verify torques of fixation bolts
• Cleaning
- inside with pressurised air
- outside with a lint-free cloth with
a mild soapy water solution
• Visual inspection
- Rotors
- Fan casings
- Electric connections
Enter all values and observations in a
log.
9. Sound
The sound emissions depend on the
installation and operation conditions,
hence no general data can be given.
Refer to the fan specifications from the
AirBox calculation program for specific
emissions and to the product catalogue
for more general data.
10. Safety
The installation must be in accordance to
Novenco’s, the current and the local
safety regulations. At a minimum these
include EN 13850.
Use only a manual
grease gun for
lubrication.
Excess grease causes bearings
to overheat and results in
failure.
Sizes
Torque [Nm]
Motor bolts (6)
Centre screw (1)
M6
9.4
6
M8
23
12
M10
45
20
M12
78
20
M16
190
25
M20
370
25
Table 4.
Motor fixation torques