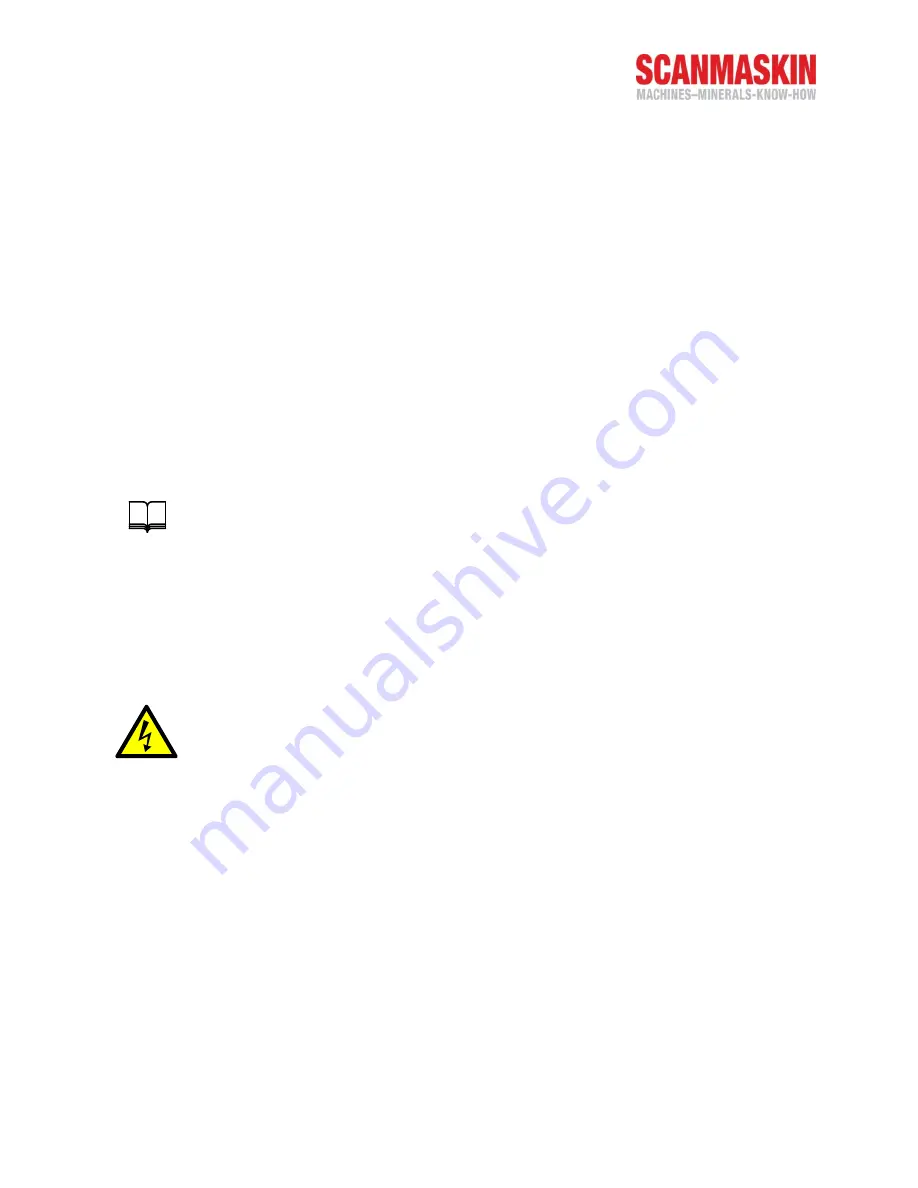
Scan Combiflex 800 – Manual
Chapter 0
- 10 -
Secure the work area around the machine in public areas providing a safety distance of at
least 10 m (3.3 ft) from the machine.
Faults must be immediately rectified.
Carry out the switch on, and switch off operations in accordance with this user guide.
Before switching on the machine make sure that no-one can be endangered when the
machine starts up.
Never operate the machine when not in its upright position.
Do not switch off or remove the exhaust and or the ventilation devices whilst the machine is
running!
All persons in the proximity of the machine must wear ear and eye protection as well as
safety shoes. In addition the machine operator must wear close-fitting protective clothing.
Only use extension cables that are sized and marked in accordance with the overall power
consumption of the machine and the valid VDE guidelines.
See “2.6Electrical safety” for further information.
Make sure there is no debris in the work area.
Check the work area for screws or other hard objects in the concrete. Don’t use the machine
if there are any foreign objects stuck into the surface. Such objects must be removed prior to
operation of machine
2.6 Electrical safety
The power source must be equipped fuses according to the table in “
1.1Electrical
specifications
”. All cables used must be marked and rated according to the fuses used.
Never connect the machine to a power source that does not provide protective earth!
Work on electrical equipment may only be undertaken by a skilled electrician or by trained
persons under the supervision of a skilled electrician as well as in accordance with the local
electrical engineering regulations.
Use only extension cables, that are used for extending the main cable, that are sized and
marked in accordance with the overall power consumption of the machine and the valid
VDE guidelines.
The electrical equipment for the plant must be inspected regularly. Defects such as loose
connections or scorched cables must be rectified immediately. Call as skilled electrician or
out customer services.
A second person must be in attendance whilst the electrical engineer is working on the
equipment.