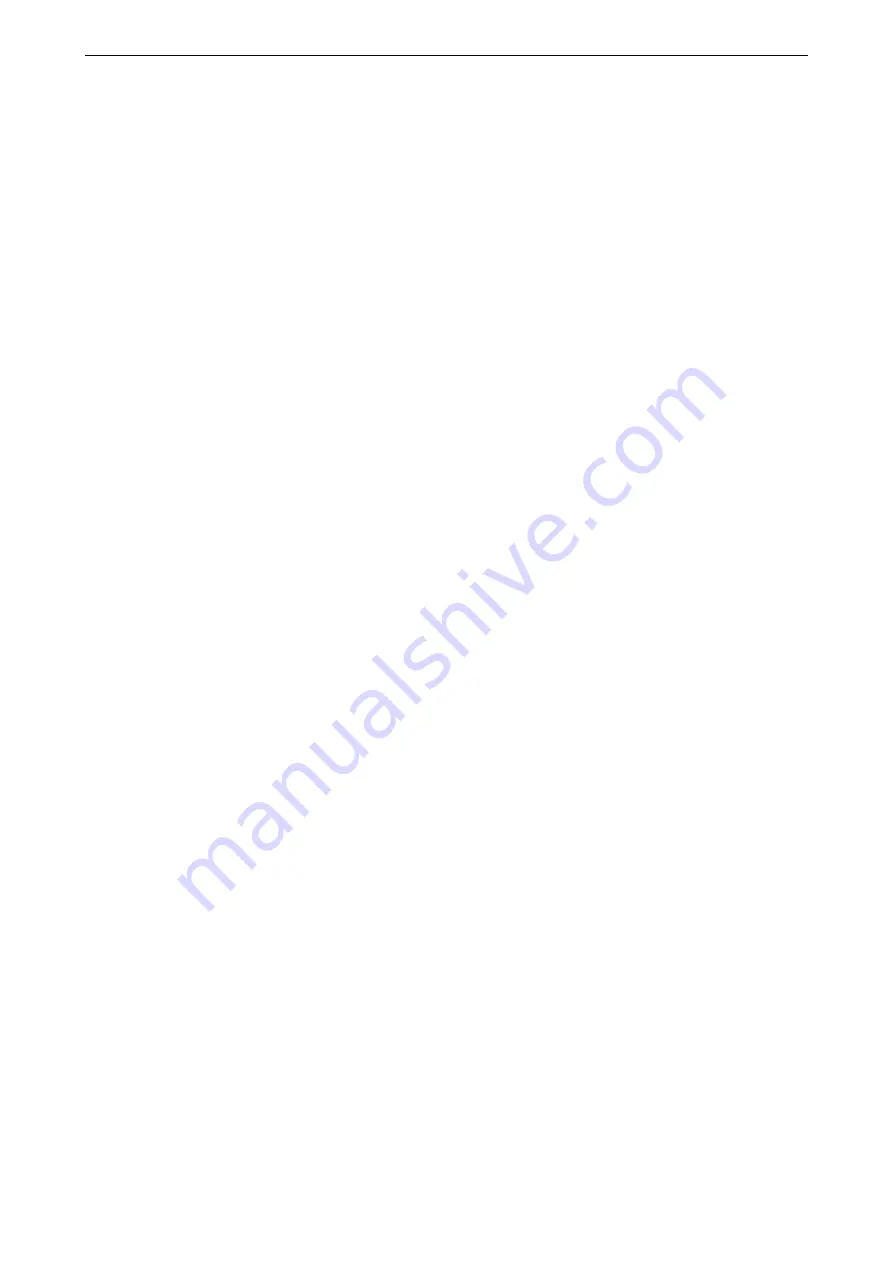
Scania Assistance
OPM 320 en-GB
71
©
Scania CV AB 2019, Sweden
Scania Assistance
Wherever you are, you can always get assistance
from the Scania service organisation, Scania As-
sistance, all day, every day of the year.
Always call the contact for your country.
Other countries: +46 8 52 24 24 24
Calls will be recorded for training purposes.
AR
0800 999 722 642
LU
+32 226 400 000
AT
+43 1 256 44 11
MA
+32 2264 0000
AU
1300 SCANIA
ME
+381 60 8484 122
1300 722 642
MW
+27 11 2265005
BA
+387 61 225 917
MY
1800 08 8500
BE
+32 2 264 00 00
+603 55909077
BG
+359 886 660 001
MX
01 800 4SCANIA
BR
0800 019 42 24
NA
+27 11 226 5005
BW
+27 11 226 5005
NL
+31 76 52 54 111
CA
+1-800-2-SCANIA
NO
+47 223 217 00
CH
+41 800 55 24 00
PE
0800 51 727
CL
188 800 722 642
PL
+48 22 331 22 33
CZ
+420 225 020 225
PT
+34 91 678 9237
DE
+49 261 887 8888
RO
+40 723 27 27 26
DK
+45 333 270 44
RS
+381 60 8484 122
EE
+372 5153 388 (Tallinn)
SE
+46 42 100 100
+372 5126 333 (Tartu)
SG
(65) 6591 7180
+372 5071 477 (Pärnu)
+65 6861 9181
+372 5047 655 (Rakvere)
SI
+386 1 2427 606
ES
+34 91 678 80 58
SK
+421 903 722 048
FI
+358 10 555 24
TR
+90 444 72 44
FR
+33 2 41 41 32 32
TZ
+27 11 226 5005
GB
0 800 800 660
US
1-800-2-SCANIA
+44 1274 301 260
UY
0800 8351
GR
+30 6944 420 410
ZA
0800 005 798
HU
+36 209 727 197
+27 11 226 5005
IE
+353 71 963 4000
ZM
+27 11 2265005
IT
+39 0461 996 222
ZW
+27 11 2265005
KR
+82 1588 6575