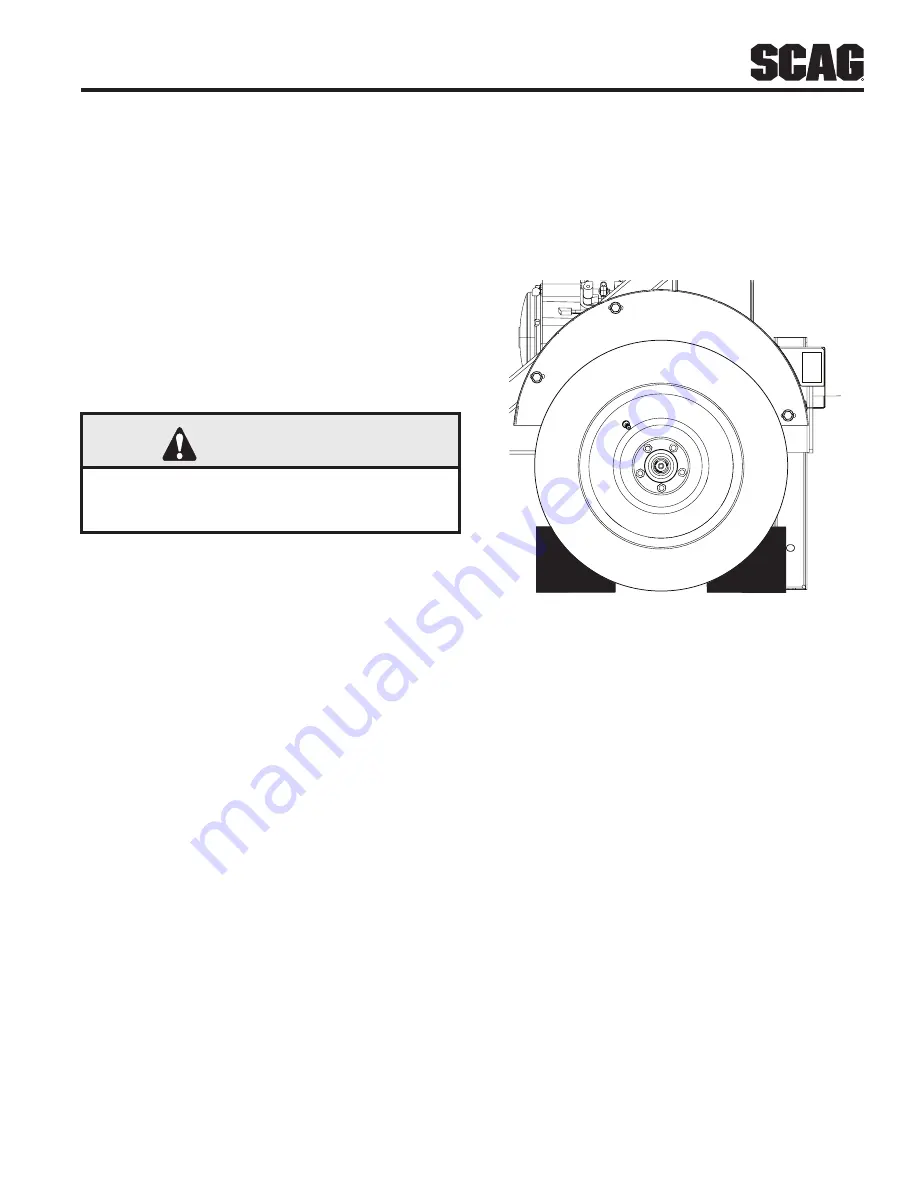
13
Section 4
R
10. Collecting debris into piles for the machine to
intercept prior to start up will save time and fuel as
well as wear and tear on the unit.
11. Keep the truck loader's intake nozzle and discharge
clean.
12. Use a slow travel speed when clearing heavy or
large amounts of material.
4.6 HILLSIDE OPERATION
Slopes are a major factor related to loss-of-control and tip
over accidents which can result in severe injury or death.
All slopes require extra caution.
WARNING
DO NOT operate on steep slopes. Poor footing
could cause a slip and fall accident. ALWAYS
FOLLOW OSHA APPROVED OPERATION.
1. Do not operate on slopes if you are uneasy or
uncertain. Ultimate responsibility for safe operation
on slopes rests with the operator.
2. Be sure of footing on slopes.
3. Caution must be used when operating on slopes,
especially when the grass is wet. Wet grass reduces
traction and control.
4. To prevent tipping or loss of control, keep all
movements on slopes slow and gradual.
5. Do not turn on slopes unless necessary, and then
turn slowly and down hill when possible.
6. Do not start or stop on slopes. If tires lose traction,
stop the unit and proceed slowly straight down the
slope.
7. Be alert for holes, rocks, roots, ruts and other hidden
hazards in the terrain. Uneven terrain could cause a
slip and fall accident.
8. Do not operate near drop-offs, ditches, or
embankments. The operator could lose footing or
balance or unit could suddenly turn over if a wheel is
over the edge of a cliff or ditch, or if the edge caves
in.
4.7 UNCOUPLING THE UNIT FROM THE TOW
VEHICLE
1. Park the machine on a flat, level surface only. Do not
park the machine on an incline.
2. Block the wheels to prevent the machine from
moving. See Figure 4-4.
Figure 4-4. Wheel Chocks
3. Disconnect the trailer wiring plug from the tow
vehicle.
4. Unhook the safety chains from the rear of the tow
vehicle.
5. Unlock the ball hitch coupler lever on the unit and flip
up.
6. Crank down the tongue jack until the ball hitch
coupler on the unit clears the ball hitch on the tow
vehicle.
7. Pull and turn the spring latch to unlock the pin
securing the rear support leg in the transport
position. See Figure 4-5.