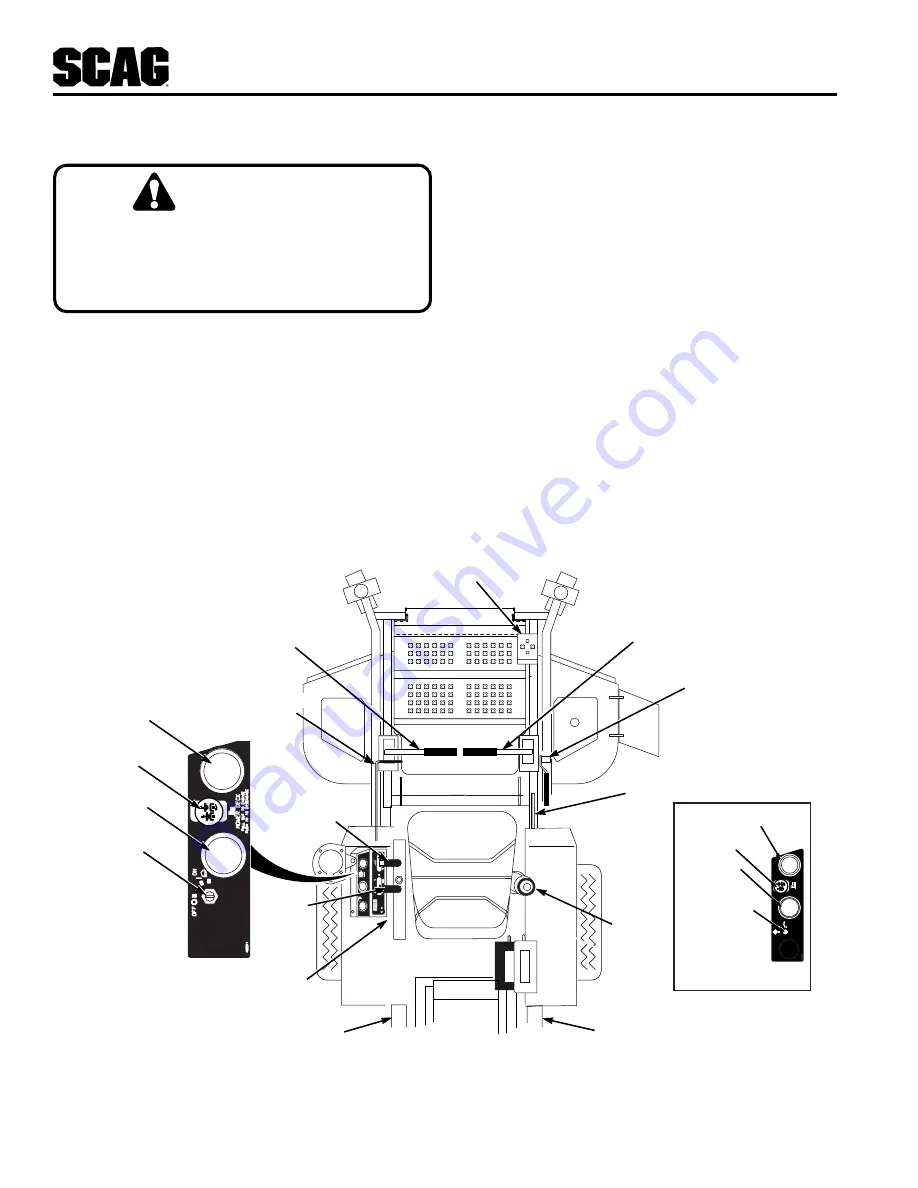
10
Section 4
OPERATING INSTRUCTIONS
Do not attempt to operate this mower unless you
have read this manual. Learn the location and
purpose of all controls and instruments before you
operate this mower.
4.1 CONTROLS AND INSTRUMENT
IDENTIFICATION
Before operating the mower, familiarize yourself with all
mower and engine controls. Knowing the location,
function and operation of these controls is important for
safe and efficient operation of the mower.
CAUTION:
1. Ignition Switch (Figure 4-1). The ignition switch
is used to start the engine and has three positions;
OFF, ON, and START.
2. Mower Deck Switch (Figure 4-1). Used to engage
and disengage the mower drive system. Pulling up
on the switch will engage the deck drive. Pushing
down on the switch will disengage the deck drive.
3. Engine Choke Control (Figure 4-1). Used to start
a cold engine.
4. Engine Throttle Control (Figure 4-1). Used to
control the engine speed. Pushing the lever forward
increases engine speed. Pulling the lever back
decreases engine speed. Full back position is the
IDLE position. Full forward is the cutting position.
Figure 4-1 Controls and Hour Meter Instruments
CH
O
K
E
48
13
48
F
LEFT STEERING
CONTROL
MOWER DECK
IGNITION SWITCH
FUEL GAUGE
DUMP VALVE
DUMP VALVE
FUSES
ENGINE
CHOKE
CONTROL
ENGINE THROTTLE
CONTROL
RIGHT STEERING
CONTROL
DECK LIFT
DECK RELEASE
390S0142A-1
PARKING BRAKE
CONTROL
CUTTING HEIGHT
ADJUSTMENT
PULL OUT
T
O
ENGA
GE
ON
ST
AR
T
PUSH IN
T
O
DISENGA
GE
OFF
481669
MO
WER DECK
AMMETER
MOWER DECK SWITCH
IGNITION SWITCH
TEMPERATURE GAUGE
KAWASAKI MACHINE ONLY
AMMETER
SWITCH
WATER TEMPERATURE