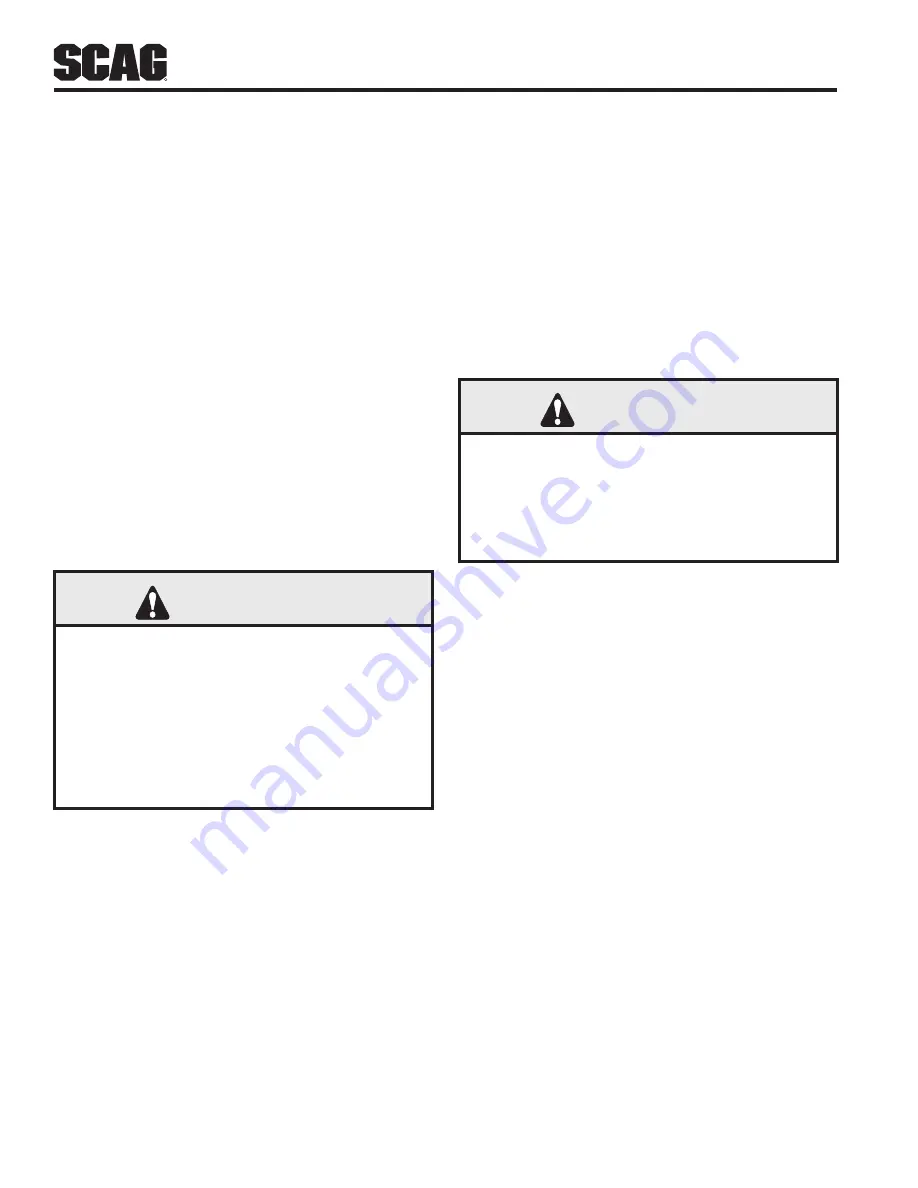
6
R
Section 2
11. Never direct the discharge of material toward
anyone. Avoid discharging material against a wall
or obstruction. Material may ricochet back toward
operator.
12. Before attempting to start the engine, with the
operator in the seat, disengage power to the cutter
deck, place the steering control levers in the neutral
position and engage the parking brake.
13. Shut off the engine, remove the ignition key, and
wait for all movement to stop before cleaning the
machine, removing grass catcher or unclogging the
discharge guard.
WARNING
DO NOT use your hand to dislodge the clogged
discharge chute. Use a stick or other device to
remove clogged material after the engine has
stopped running and the blades have stopped
turning.
14. Be alert for holes, rocks, roots and other hidden
hazards in the terrain. Keep away from any drop-offs.
Beware of overhead obstructions (low limbs, etc.)
and underground obstacles (sprinklers, pipes, tree
roots, etc.). Cautiously enter a new area. Be alert for
hidden hazards.
15. Disengage power to cutter deck before backing up.
Do not mow in reverse unless absolutely necessary
and then only after observation of the entire area
behind the mower. If you must mow in reverse,
maintain a constant lookout to the rear of the
machine and mow slowly.
16. DO NOT turn sharply. Use care when backing up.
17. Disengage power to cutter deck before crossing
roads, walks or gravel drives.
18. Watch for traffic when operating near or crossing
roadways.
19. Mow only in daylight or good artificial light.
20. NEVER raise the deck with the blades engaged.
21. NEVER leave the machine running unattended.
22. Disengage the mower, lower the attachments, set
the parking brake, stop the engine, and remove the
key before dismounting.
6. Keep flammable objects (cigarettes, matches, etc.),
open flames and sparks away from the fuel tank and
fuel container.
7. Use only approved containers. Use only non-
metal, portable fuel containers approved by the
Underwriter's Labratory (U.L.) or the American
Soceity for Testing & Materials (ASTM).
2.8 OPERATION CONSIDERATIONS
1. Know the function of all controls and how to stop
quickly.
2. NEVER operate the machine in a closed area.
3. Keep hands and feet away from cutter blades.
Contact can injure.
4. DO NOT put hands or feet near rotating parts or
under the machine.
5. Keep clear of the discharge opening.
6. Follow the manufacturer's recommendations for
wheel weights and counterweights.
WARNING
DO NOT operate on steep slopes. To check a slope,
attempt to back up it (with the cutter deck down).
If the machine can back up the slope without the
wheels slipping, reduce speed and use extreme
caution. Under no circumstances should the
machine be operated on slopes greater than 15
degrees. See Figure 2-1, Page 7 to determine
approximate slope of area to be mowed. ALWAYS
FOLLOW OSHA APPROVED OPERATION.
7. Reduce speed and exercise extreme caution on
slopes and in sharp turns to prevent tipping or loss
of control. Be especially cautious when changing
directions on slopes.
8. Stay two cut widths away from slopes, drop offs,
ditches and retaining walls.
9. To prevent tipping or loss of control, start and stop
smoothly, avoid unnecessary turns and travel at
reduced speed. Use caution when operating the
mower on an incline with the optional grass catcher
installed.
10. Immediately apply the parking brake if you lose
steering control while operating. Inspect the machine
and correct the problem before continuing to operate.