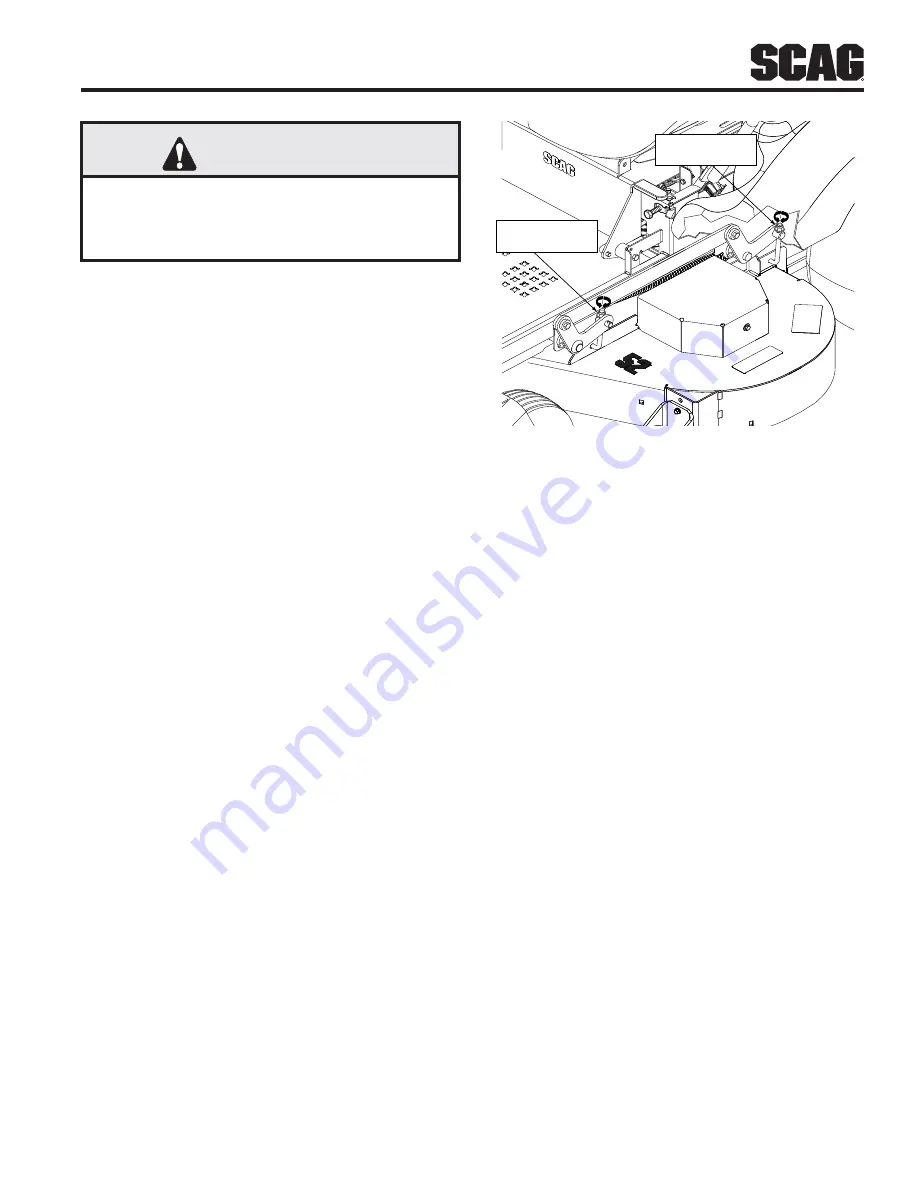
25
R
Section 6
WARNING
If the pump drive belt fails, steering control will be
lost which could result in serious injury or death.
Replace the pump drive belt as needed or every
400 hours / 2 years, whichever occurs fi rst.
6.5 BELT ALIGNMENT
Belt alignment is important for proper performance of
your Scag mower. If you experience frequent belt wear
or breakage, see your authorized Scag service center for
belt adjustment.
6.6 CUTTER DECK ADJUSTMENTS
Cutter deck level, pitch and height are set at the factory.
However, if these adjustments should ever need to be
made, the following procedures will aid in obtaining the
proper cutter deck adjustment.
- NOTE -
Before proceeding with the cutter deck adjustments,
be sure that all tires are properly inflated. If any
of these procedures do not achieve proper cutter
deck level, pitch or height, please contact your
authorized Scag dealer.
CUTTER DECK LEVEL
The cutter deck should be level from side-to-side for
proper cutting performance. To check for level, be sure
that the mower is on a flat, level surface, the tires are
properly inflated and the cutter deck is set at the most
common cutting height that you will use. On the RH side
of the machine, check the distance from the top of the
cutter deck to the floor. Next check the distance from the
top of the cutter deck to the floor on the LH side of the
machine. Both measurements should be the same. If the
two measurements are different, the cutter deck level must
be adjusted as follows:
1. If the cutter deck is lower on one side, locate the
elastic stop nuts on the front and rear of the lower
side of the cutter deck. See Figure 6-4.
ADJUSTMENT
NUT
ADJUSTMENT
NUT
Figure 6-4. Cutter Deck Level Adjustment
2. Turn the elastic stop nuts on the front and rear deck
level links clockwise until the cutter deck is level
between both sides. See Figure 6-4
3. Tighten the two (2) elastic stop nuts to secure the
cutter deck in the proper position.
CUTTER DECK PITCH
The pitch of the cutter deck should be equal between
the front and rear of the cutter deck for proper cutting
performance. To check for proper deck pitch, be sure
that the mower is on a flat, level surface and the tires are
properly inflated.
Check the distance from the top of the cutter deck to the
floor at the rear RH side of the cutter deck directly behind
the cutter deck hanging link. Next check the distance from
the top of the cutter deck to the floor at the front RH side of
the cutter deck directly in front of the cutter deck hanging
link. The measurement at the front of the cutter deck
should be the same as the rear of the deck. Make these
measurements at the LH side of the cutter deck also. If the
measurement at the front of the deck is not the same, the
cutter deck pitch must be adjusted as follows:
1. Loosen the elastic stop nuts securing the deck level
links on the front of the cutter deck on both sides.
See Figure 6-5 and 6-6.