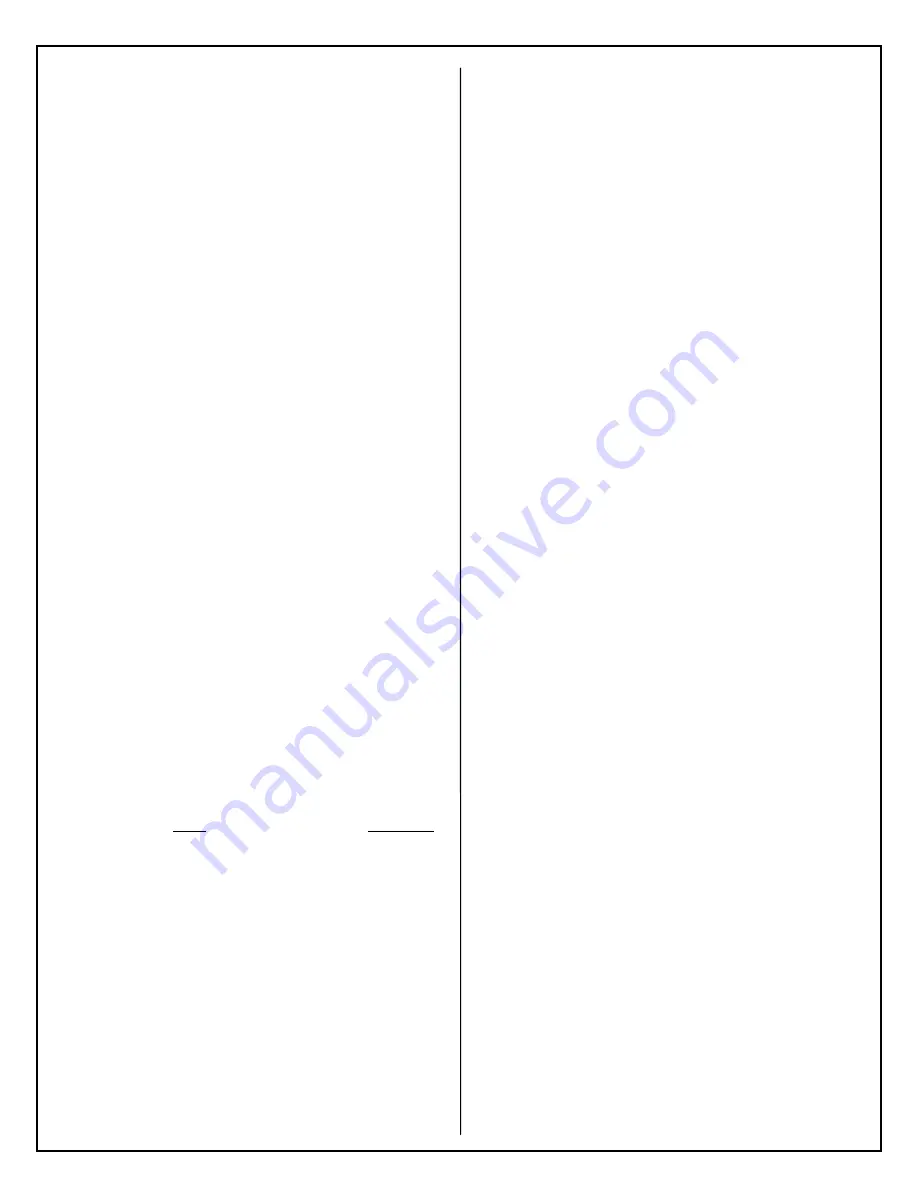
SAVANNAH STOKER v3 INSTRUCTION MANUAL
2015.01 Copyright © Sound Solutions, LLC. All Rights Reserved. Find us on Facebook.com/SavannahStoker , Pelletheads.com and LetsTalkBBQ.com
7
Operational Parameters Defined,
continued from page 6
6.3.1
“IGN” and “HY” Control the Igniter’s ON/OFF Temperatures
The parameters IGN and HY are used together to control the igniter’s
functions.
IGN
parameter: The Igniter’s ON temperature.
HY
parameter: The Hysteresis Band is used to protect the igniter from
cycling ON/OFF to rapidly.
How it works:
When smoker starts from cold, the Igniter will be on. As the pellets
light and the temperature inside the cooking chamber rises the Igniter
will go OFF when temperature inside the cooking chamber reaches
IGN + HY
. If the fire goes out due to an un-intentional reason, the
temperature will drop. The Igniter will turn back ON when
temperature drops to below the IGN setting and will go off again
when the temperature reaches IGN + HY.
6.3.2
“At”Auto-Tune
Parameter
“AT”
is used to start the Auto-tune process.
At=1
Sets Auto-Tune in delayed start. The Auto-tune process is
delayed until the A/M KEY is pressed. This is the preferred
method to start auto-tune.
At=2
Auto-tune will start in 10 seconds.
At=3
Normal controller operation. After auto-tune is complete the
controller automatically sets the value to 3.
When to Run Auto-tune:
In most cases the controller is very adaptive and works well with the
default parameter values for P,I,D, but every grill and cooking
conditions are different. If temperature swings at 250°F are
consistently greater than 10-15° then running Auto-tune may improve
the controller’s performance by determining new values for the PID
parameters.
Preferred Method to Start Auto-tune:
1)
Write down you current values for I, P, and D for future reference.
2)
Set the target temperature (SV) in the 250°to 275°F range.
3)
Let the grill’s temperature stabilize for 20-30 minutes.
4)
Set At=1
5)
Start Auto-tune by pressing the “A/M” KEY when the temperature
reading (PV) is above the target temperature but is descending.
6)
The “At” symbol will blink in the lower display (SV) during the
Auto-tune process.
7)
If you need to stop the Auto-tuning process, press and hold the
“A/M” KEY for about 2 seconds until the "At" symbol stops
blinking in the lower display window.
During the Auto-tune process the controller will execute 2-3 cycles.
The microprocessor in the controller will analyze the period,
amplitude, and waveform of the temperature oscillations and
calculate the optimal PID control parameter values. When Auto-tune
is complete the controller will return to performing accurate artificial
intelligence control using the new values.
If the Auto-tune results are not satisfactory, you can manually fine-
tune the PID constants for improved performance. Or perform auto
tune again. Sometimes the controller will get better parameters.
6.3.3
PID Control Parameters Explained.
Please note the controller uses an enhanced version of PID control
algorithms. Tuning of the controller is different than traditional PID
controllers. The parameters are explained below.
Before adjusting any of the PID parameters, we recommend running
Auto-tune as outlined in section 6.3.2. Before making adjustments to the
PID parameters always write down your current settings.
After making
changes let the grill stabilize for 30-45 minutes and evaluate the results.
What works best at 250° may not give the same result @180°. Keep
good notes.
Proportional Band “P”
The unit is in degrees.
This parameter controls the output of the controller based on the
difference between the measured and set temperatures. The larger
the “P” value means the weaker the action (lower gain). For
example, if P=20, the proportional band is 20 degrees. When the
PV reading is 20 degrees or more below the set point (SV), the
controller will have 100% output (or the value of OutH, see 6.3.7).
When the temperature is 10 degrees below the set point, the output
is 50%. When the temperature is equal to the setting, the controller
will have 0% output (assuming integral and derivative functions are
turned off). This constant also affects both integral and derivative
action. Smaller P values will make both integral and derivative
action stronger.
Typical values for “P” would be in the range of 20-40°F
If you change from Fahrenheit to Celsius, divide “P” by 1.8.
When changing “P” use small steps of 1 or 2.
Integral time “I”
The unit is in seconds.
This parameter controls the output of controller based on the
difference between the measured and set temperature integrated
with time. Integral action is used to eliminate temperature offset
(both above and below set point, SV). A larger number means
slower action. e. g. assuming the difference between the measured
and set temperature is 10 degrees and remains unchanged, the
output will increase continuously with time until it reaches 100%.
When the temperature fluctuates more than 15° (when above 250°)
an increase of the integral time may be needed. Decrease if the
controller is taking too long to eliminate the temperature offset.
When I=0, the system becomes a PD controller.
Typical values for “I” would be in the range of 80-300 seconds, but
the recommend setting for “I” is 4 times the value of “D”, I=Dx4.
If you change “D” also change “I”
Derivative time “D”
The unit is in seconds.
Derivative action contributes to the output power based on the rate
of temperature change. Derivative action can be used to minimize
the temperature overshoot by responding to the rate of change. The
larger the number, the faster the action will be, e.g. when the
cooking chamber door is opened, the temperature will drop at very
high rate. The derivative action will change the controller output
based on the rate of change rather than the net amount of change.
This will allow the controller to act sooner.
Increases to “D” will decrease overshoot, and improve settling time,
Typical values for “D” would be in the range of 20-75 seconds.
When changing “D” use small steps of 2-3.
If you change “D” also change “I” to 4 times the value of “D”, I=Dx4.