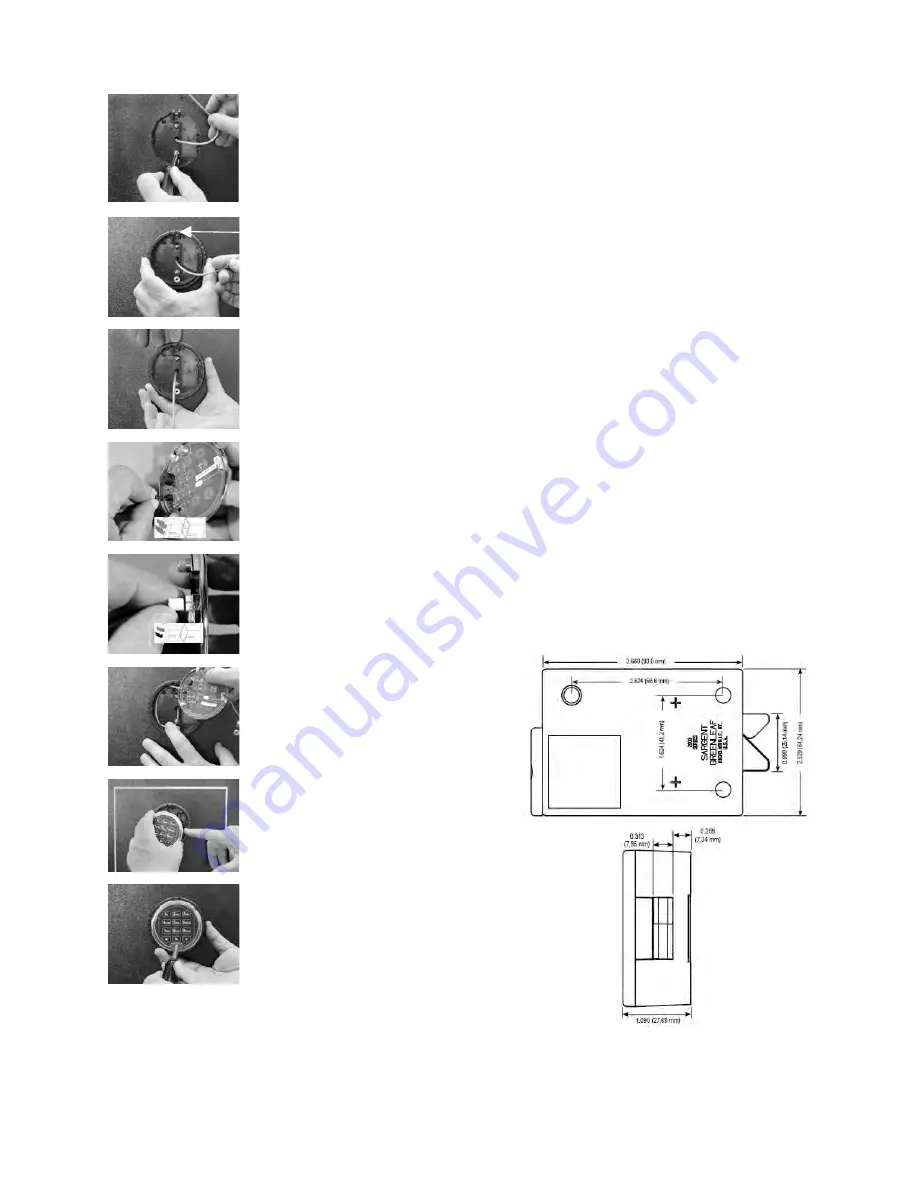
2008 Sargent & Greenleaf, Inc.
Document 630-650
Revised 6/6/2008
Sargent & Greenleaf, Inc.
Sargent & Greenleaf S.A.
A Wholly Owned Subsidiary of Stanley Security Solutions, Inc.
9, chemin du Croset
PO Box 930, Nicholasville, KY 40356
1024 Ecublens, Switzerland
Phone: (800)-826-7652 Fax: (800)-634-4843
Phone: +41-21 694 34 00
Phone: (859)-885-9411 Fax: (859)-887-2057
Fax: +41-21 694 34 09
7. Bring the lock cable through the center hole
in the mounting base, then fasten the base to
the safe door, using either the silver colored
pair of 8-32 machine screws or the reddish
colored pair of M4 screws, whichever is
appropriate for the prepared holes in the safe
door.
8. Place the keypad ring onto the base. Note
that there is a spring-loaded tab at the top of
the ring (see white arrow). Orient it as shown
when placing the ring on the base.
9. Once the ring is against the base, rotate it
clockwise until the tab is straight up. You may have
to pull the spring-loaded tab forward before you can
rotate the ring into position. When the tab is straight
up, it will snap into position.
10. Plug the lock cable into the receptacle on the
underside of the keypad. Note that the features of
the plug and receptacle can only align when the
plug is correctly oriented.
11. If the power leads (red and black wires and
white connector) are not already connected to the
keypad, plug the white connector into the white
receptacle on the back of the keypad. Align the
connector’s single ridge with the slot in the
receptacle.
12. The lock cable should be routed inside the
keypad assembly as shown in the photo. Make sure
the cable is not crimped or pinched.
13. The battery wires should be routed as shown
here. Proper cable placement keeps wires from
being crushed or pinched when the keypad is
installed.
14. Install the keypad into the base. Seat the raised
ridge at the top of the keypad into the matching
recess in the top of the previously installed ring first,
then secure the assembly by installing one of the
provided 8-32 machine screws at the bottom, as
shown. One screw is a standard Phillips style, to be
used when keypad removal is anticipated at some
time in the future. The other screw is a one-way
style, to be used for more secure EN1300 compliant
installations. When the screw is installed, cover it
with the self-stick S&G logo to finish the installation.
Z
02
Specifications
Attaching Screws:
Use only the screws provided with the lock. They
must engage the mounting plate by at least four full threads. Do not use
lock washers or thread sealing compounds.
Recommended Attaching Screw Torque:
30 to 40 inch-
pounds (33,9 to 45,2 dNm).
Minimum Lock Cable (Spindle) Hole Diameter:
0.312 inch
(7,9 mm).
Maximum Lock Cable (Spindle) Hole Diameter:
0.5 inch
(12,7 mm).
Lock is Designed to Move:
0.0 lbs. (0 Newtons).
Lock Bolt Maximum Free Movement:
0.352 inch (8,95 mm)
0.109 inch outside the edge of the lock case.
Maximum Bolt End Pressure:
lock is designed to withstand at
least 225 lbs. (1000 Newtons).
Maximum Bolt Side Pressure:
safe and container boltwork or
locking cam designs must never apply more than 225 lbs. (1000 Newtons)
of side pressure on the lock bolt.
Mounting Environment:
The lock body is designed to be mounted
inside a secure container. The container must be constructed to offer
protection against physical attack directed at the lock. The amount of
protection is dependent on the desired level of security for the system as a
whole. Lock protection may include barrier materials, relock devices,
thermal barriers, thermal relock components, or any combination of these.
Code Restrictions:
Personal data that can be related to a code
holder, such as a birth date, street number, or phone number, should not
be used in creating a lock code. Avoid codes that can be easily guessed.
After the lock is changed to a new code, the lock function must be checked
by locking and unlocking it several times with the container door open.
Make sure it functions correctly before closing the door.
Note:
Every installation of this product must comply with these
requirements and those in the product installation instructions to qualify for
the manufacturer’s warranty and to comply with EN1300 requirements.