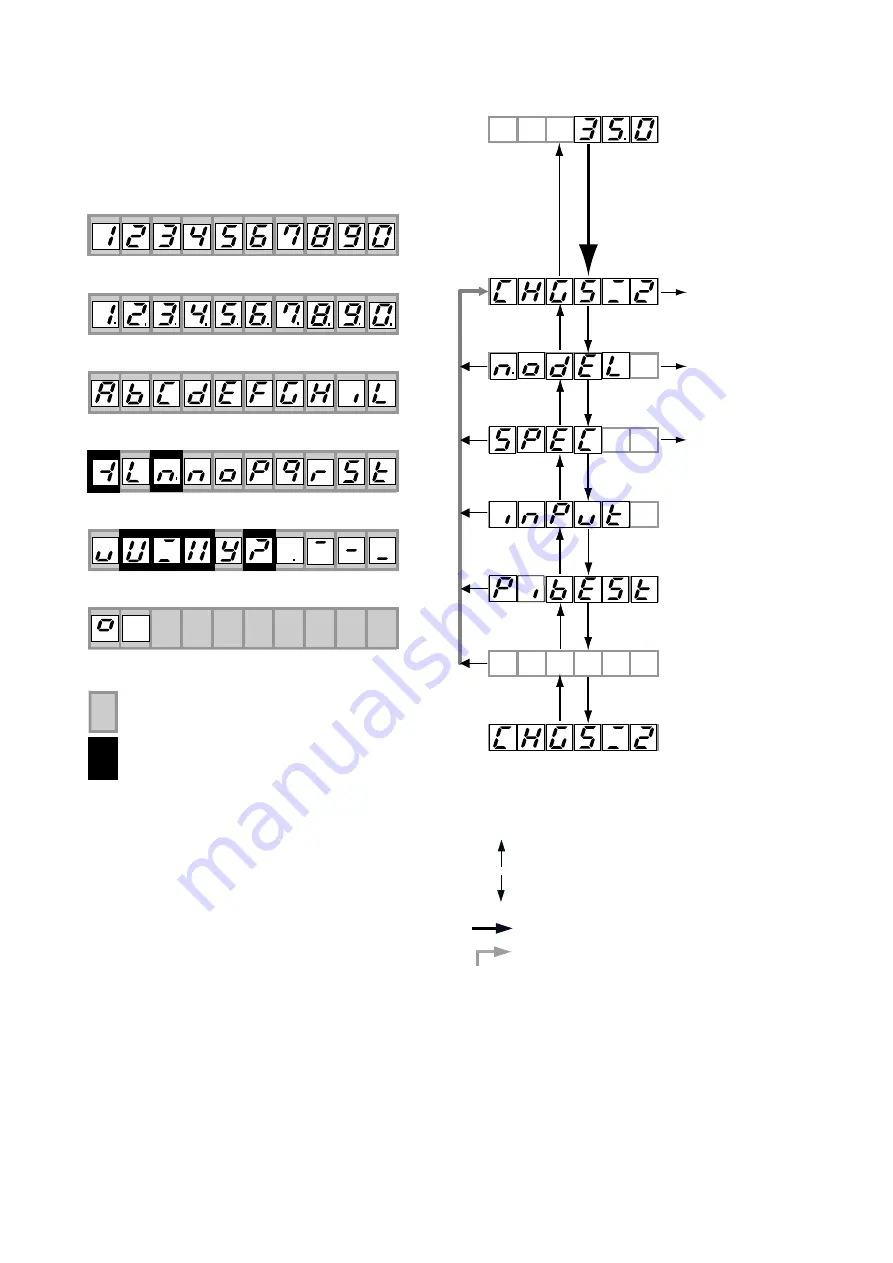
1 2 3 4 5 6 7 8 9 0
1. 2. 3. 4. 5. 6. 7. 8. 9. 0.
A
B C D
E
F
G H
I
J
K
L M N O P Q R
S
T
U
V W X
Y
Z
.
-
_
o
_
Displayed digit
Non-standard digit display
Legend
4.8.2 - Instructions to verify operation board parameters
Fig. 27
refer to chapter 4.8.3.
Specification setting.
Push the "set" and "
q
" keys
simultaneously for about 2 seconds.
Generator temperature (35°C)
refer to chapter 4.8.4.
Input setting.
refer to chapter 4.8.5
PID setting.
Push "
b
ACK" key
.
4.8 - exhibit LI
4.8.1 - Character recognition table for digital display
Fig. 26
Push "
p
" key.
Push "
q
"key.
Push the "SEt" key for about 2 seconds.
Push the "bACK" key.
Legend
Summary of Contents for Carrier 16LJ Series
Page 51: ...51 ...