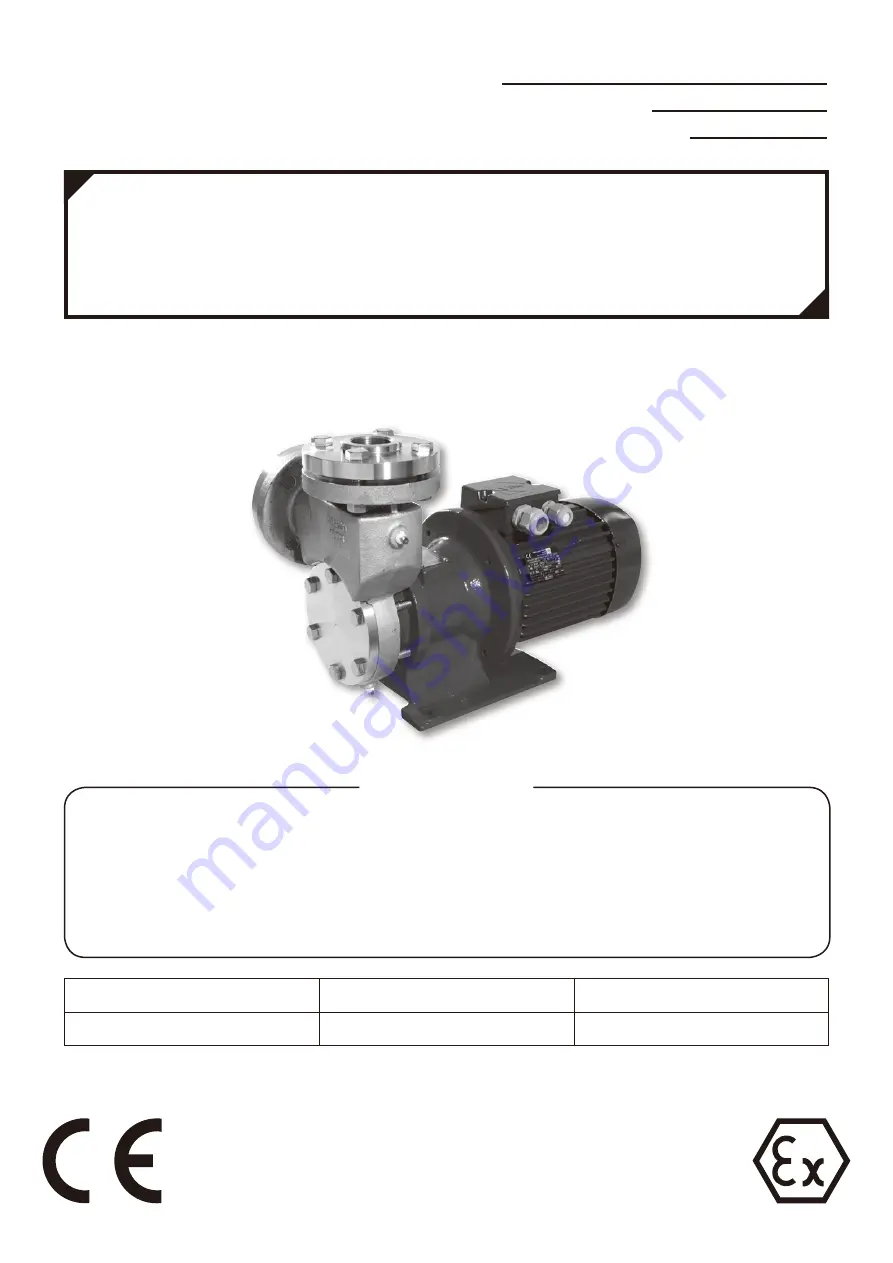
Machine Number
Code
MFG No.
INSTRUCTION MANUAL
Manual No.MEK01C(E)/1612ATEX
Original Instruction
Europe Edition
SANWA HYDROTECH CORPORATION
STAINLESS STEEL MAGNET DRIVE PUMP
SELF-PRIMING TURBINE PUMP
MEK
This instruction manual is for the person who actually operates the pump.
Please be sure this manual is provided to and understood by the operator on
the scene. If the instruction manual is also needed by personnel who install
the pump or by a staff of a plant constructor, please let us know. We will
supply another copy.
To the on-site operator: please enter the pump’s code and lot number above and for future
parts order and inquiry.
Requirements